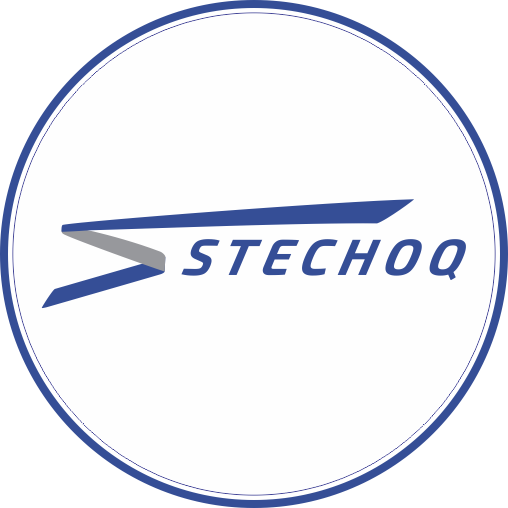
DAY 2
KONSEP DASAR
A. Proses Additive Manufacture
AM melibatkan sejumlah langkah yang bergerak dari deskripsi CAD virtual ke bagian fisik yang dihasilkan. Produk yang berbeda akan melibatkan AM dengan cara dan derajat yang berbeda. Produk kecil dan relatif sederhana hanya dapat menggunakan AM untuk model visualisasi, sementara produk yang lebih besar dan lebih kompleks dengan konten teknik yang lebih besar mungkin melibatkan AM selama berbagai tahap dan iterasi selama proses pengembangan. Selain itu, tahap awal proses pengembangan produk mungkin hanya memerlukan bagian kasar, dengan AM digunakan karena kecepatan pembuatannya. Pada tahap selanjutnya dari proses, bagian mungkin memerlukan pembersihan dan pasca-pemrosesan yang cermat (termasuk pengamplasan, persiapan permukaan, dan pengecatan) sebelum digunakan, dengan AM berguna di sini karena kompleksitas bentuk yang dapat dibuat tanpa harus mempertimbangkan perkakas. Selanjutnya, kita akan menyelidiki secara menyeluruh berbagai tahapan proses AM, tetapi untuk merangkum, sebagian besar proses AM melibatkan, setidaknya sampai tingkat tertentu, delapan langkah berikut ini.
a. Langkah CAD
Untuk memulai semua bagian AM (Additive Manufacturing) dari sebuah model perangkat lunak yang menggambarkan geometri eksternal secara menyeluruh (bentuk dan struktur objek yang akan dicetak menggunakan teknik manufaktur aditif).
Untuk memenuhi persyaratan ini, pengguna dapat menggunakan berbagai perangkat lunak pemodelan padat CAD (Computer-Aided Design) profesional. Penggunaan hampir semua perangkat lunak CAD profesional ini diperbolehkan, tetapi keluarannya harus berupa representasi padat atau permukaan 3D yang dapat digunakan dalam proses pencetakan 3D.
Secara garis besar, kalimat tersebut menyatakan bahwa untuk menggunakan teknik manufaktur aditif, semua bagian harus dimulai dari model perangkat lunak yang menggambarkan geometri eksternal, yang dapat dibuat dengan perangkat lunak CAD atau dengan menggunakan peralatan rekayasa balik untuk menciptakan representasi 3D dari objek fisik yang ada.
b. STL Convert
Format file STL yang banyak digunakan dalam mesin AM (Additive Manufacturing) dan juga kemampuan sistem CAD dalam menghasilkan format file tersebut. Hampir setiap mesin AM menerima format file STL sebagai input. Format file ini digunakan untuk menggambarkan permukaan tertutup eksternal dari model CAD asli.
Sistem CAD, atau perangkat lunak pemodelan padat Computer-Aided Design, saat ini memiliki kemampuan untuk menghasilkan format file STL. File STL ini menjadi dasar untuk perhitungan irisan (slicing) yang dilakukan dalam proses manufaktur aditif. Dalam proses slicing, objek 3D dibagi menjadi lapisan-lapisan tipis, dan informasi geometri dalam file STL digunakan untuk menghasilkan instruksi cetak layer-by-layer yang diperlukan oleh mesin AM.
c. File Transfer to Machine
Setelah file STL yang menjelaskan bagian yang akan dicetak dibuat, file tersebut harus ditransfer ke mesin AM (Additive Manufacturing) untuk proses pencetakan. Dalam proses transfer file STL ke mesin AM, ada kemungkinan beberapa manipulasi umum yang perlu dilakukan pada file tersebut. Manipulasi ini bertujuan untuk memastikan bahwa ukuran, posisi, dan orientasi bangunan yang benar sesuai dengan kebutuhan pencetakan.
Manipulasi ukuran dapat dilakukan untuk mengubah skala objek dalam file STL agar sesuai dengan ukuran yang diinginkan dalam pencetakan. Misalnya, jika objek perlu diperbesar atau diperkecil, ukuran file STL dapat disesuaikan.
d. Machine Setup
Pentingnya melakukan pengaturan yang tepat pada mesin AM (Additive Manufacturing) sebelum proses pembuatan atau pencetakan dimulai. Pengaturan ini berkaitan dengan parameter build atau parameter pembangunan yang meliputi berbagai aspek seperti kendala material, sumber energi, ketebalan lapisan, pengaturan waktu, dan sebagainya. Pengaturan yang tepat pada mesin AM diperlukan untuk memastikan bahwa proses pembuatan berjalan dengan baik dan menghasilkan hasil yang diinginkan.
e. Build
Proses pembangunan bagian pada mesin AM (Additive Manufacturing) sebagian besar dilakukan secara otomatis, dan mesin tersebut dapat melanjutkan proses pembuatan dengan sedikit atau tanpa pengawasan manusia. Namun, pemantauan dangkal mesin masih perlu dilakukan untuk memastikan tidak terjadi kesalahan atau gangguan yang dapat mempengaruhi proses pencetakan.
Meskipun mesin AM dapat beroperasi secara otomatis, pengawasan dangkal atau pemantauan yang terbatas masih diperlukan. Pemantauan ini dilakukan untuk memastikan bahwa proses berjalan dengan baik dan menghindari kemungkinan terjadinya masalah yang dapat mempengaruhi hasil pencetakan.
f. Removal
Setelah mesin AM (Additive Manufacturing) menyelesaikan proses pembuatan, yaitu bagian-bagian yang telah dicetak perlu dilepas. Proses pelepasan ini mungkin memerlukan interaksi dengan alat bantu. Pelepasan bagian-bagian yang dicetak dari mesin AM bisa melibatkan penggunaan alat bantu seperti alat pemotong, penjepit, atau alat lainnya. Hal ini dikarenakan bagian yang telah dicetak dapat terhubung dengan sisa bahan atau struktur penyangga yang perlu dihapus untuk mendapatkan bagian yang siap digunakan. Dengan menggunakan alat bantu yang tepat dan dilengkapi dengan interlock pengaman, proses pelepasan bagian dari mesin AM dapat dilakukan dengan aman dan efisien setelah selesai proses pembuatan.
g. Post-Process
Setelah komponen selesai dicetak dan dikeluarkan dari mesin AM (Additive Manufacturing), mungkin diperlukan beberapa tahapan pembersihan tambahan sebelum bagian tersebut siap digunakan. Pembersihan tersebut dapat melibatkan perbaikan kelemahan, penghapusan fitur pendukung, dan kebersihan permukaan. Proses pembersihan ini membutuhkan waktu dan manipulasi manual yang hati-hati dan berpengalaman agar bagian yang dicetak mencapai kualitas yang diinginkan.
h. Application
Beberapa hal terkait dengan penggunaan dan perawatan komponen yang telah dicetak menggunakan mesin AM (Additive Manufacturing).
1. Perlakuan tambahan
Meskipun komponen mungkin sudah siap digunakan setelah dicetak, terkadang mereka memerlukan perlakuan tambahan sebelum dapat diterima untuk digunakan.
2. Perawatan mesin AM
Mesin AM umumnya memerlukan perawatan yang cermat. Banyak mesin AM menggunakan teknologi laser atau printer yang rapuh dan memerlukan pemantauan yang hati-hati.
3. Standar material dan proses
Proses AM umumnya tidak diatur oleh standar material dan proses yang umum. Oleh karena itu, ada upaya untuk mengatasi masalah ini melalui komite teknis ASTM F42 tentang teknologi manufaktur tambahan. Mesin-mesin AM umumnya disarankan untuk menggunakan pola tes yang disediakan oleh pabrikan untuk memastikan bahwa mesin beroperasi dalam batas yang dapat diterima.
4. Penanganan material
Selain mesin, material yang digunakan dalam proses AM juga perlu ditangani dengan hati-hati. Bahan baku yang digunakan dalam beberapa proses AM memiliki umur simpan terbatas dan mungkin memerlukan kondisi penyimpanan yang mencegah terjadinya reaksi kimia yang tidak diinginkan.
B. Pengaplikasian Additive Manufacture
Manufaktur aditif memasuki dekade ketiga pengembangan teknologi komersial mengalami sejumlah perubahan signifikan yang telah menghasilkan peningkatan akurasi, sifat mekanik yang lebih baik, jangkauan aplikasi yang lebih luas, serta pengurangan biaya mesin dan bagian yang dibuat dengan teknologi tersebut.
1. Biaya, karena beberapa mesin menggunakan teknologi yang lebih mahal, seperti laser, harganya pasti akan lebih mahal daripada yang lain.
2. Rentang bahan, beberapa mesin hanya dapat memproses satu atau dua bahan, sementara yang lain dapat memproses lebih banyak, termasuk komposit.
3. Pemeliharaan, dengan beberapa mesin yang lebih kompleks daripada yang lain, persyaratan perawatan akan berbeda. Beberapa perusahaan akan menambahkan biaya ke mesin mereka untuk memastikan bahwa mereka didukung dengan lebih baik.
4. Kecepatan, karena teknologi yang diterapkan, beberapa mesin akan membangun suku cadang lebih cepat daripada yang lain.
5. Keserbagunaan, beberapa mesin memiliki parameter pengaturan yang kompleks di mana kualitas komponen dapat diseimbangkan dengan parameter lain, seperti kecepatan pembuatan. Mesin lain memiliki variasi pengaturan yang lebih sedikit yang membuatnya lebih mudah digunakan tetapi mungkin kurang serbaguna.
6. Ketebalan lapisan, beberapa mesin memiliki batasan ketebalan lapisan karena parameter pemrosesan material. Membuat lapisan ini lebih tipis pasti akan memperlambat kecepatan pembuatan.
7. Akurasi, selain ketebalan lapisan, resolusi in-plane juga berdampak pada akurasi. Hal ini terutama dapat mempengaruhi ukuran fitur minimum dan ketebalan dinding suatu bagian. Misalnya, sistem berbasis laser memiliki ukuran fitur minimum yang didasarkan pada diameter sinar laser.
Pengaplikasian Additive Manufacturing di berbagai bidang, yaitu:
a. Penggunaan Additive Manufacturing di Bidang Medis
Gambar di atas menunjukkan contoh aplikasi dalam setiap kategori, termasuk (a) model praoperasi tengkorak dan jantung, (b) implan kraniomaksilofasial, (c) panduan pengeboran gigi, pinset reduksi, swab hidung dan tenggorokan, (d) dukungan eksternal yang dipersonalisasi dan mobil, dan (e) scaffold untuk penggantian tulang zigomatik dan implan orbital yang dapat terurai.
1. Medical models
Model medis didasarkan pada anatomi pasien, dan dapat digunakan untuk perencanaan dan pelatihan operasi pra dan pascaoperasi; pelatihan mahasiswa kedokteran; dan memberikan informasi kepada pasien dan keluarga pasien. Geometri dapat diubah, misalnya dengan mengambil bagian yang menarik atau mengubah skala menjadi lebih besar atau lebih kecil. Jika model digunakan untuk pelatihan, seperti pengeboran tulang, respons haptik yang mendekati tulang mungkin diinginkan. Jika ini digunakan di ruang operasi, disarankan agar model-model tersebut disterilkan, tetapi biasanya opsi material dapat dipilih dengan bebas, yang juga menunjukkan bahwa ini adalah salah satu aplikasi yang paling umum. Gambar di bawah menunjukkan alur kerja proses tipikal untuk manufaktur model medis yang dimulai dari anatomi pasien yang diambil melalui pencitraan medis, seperti tomografi komputer (CT), pencitraan resonansi magnetik (MRI), atau ultrasonografi, kemudian diikuti dengan pembuatan geometri model 3D untuk AM menggunakan algoritma segmentasi. Setelah AM, seringkali diperlukan pemrosesan lanjutan seperti penghilangan struktur pendukung.
2. Implants
Implan dibuat dengan teknologi manufaktur tambahan (AM) untuk menggantikan jaringan yang rusak atau hilang secara langsung atau tidak langsung. Kelas ini juga mencakup aplikasi kedokteran gigi seperti mahkota dan jembatan gigi. Bahan yang digunakan harus kompatibel dengan jaringan dan memiliki persyaratan yang ketat, sehingga proses persetujuan memakan waktu lama. Sifat permukaan dapat mempengaruhi pelekatan sel. Beberapa penelitian terbaru telah menjelajahi bagaimana cara menyisipkan bahan ke dalam implan, misalnya sebagai sistem penghantaran obat. Pada implan yang dipersonalisasi, AM adalah solusi yang menguntungkan, dan proses yang khas melibatkan pemindaian anatomi pasien yang serupa dengan model medis. Kemudian, model 3D digital dari anatomi pasien ini digunakan sebagai referensi desain untuk mencapai kesesuaian yang spesifik pada pasien. Sebagian besar implan yang umum dibuat dari logam menggunakan proses penyatuhan bed powder, yang memerlukan tahapan pasca-produksi yang berbeda seperti pemesinan penyangga, poles, dan perlakuan panas. Sebelum digunakan secara klinis, implan harus disterilkan. Gambar di bawah menunjukkan alur proses tipikal untuk pembuatan implan dengan teknologi manufaktur tambahan, dimulai dari pencitraan medis dan segmentasi, diikuti oleh pemodelan 3D implan, proses AM, pasca-produksi, dan sterilisasi.
3. Tools, Instruments and Parts for Medical Devices
Alat, instrumen, dan bagian-bagian untuk perangkat medis memungkinkan atau meningkatkan operasi klinis. Mereka dapat menggunakan dimensi dan bentuk yang spesifik untuk setiap pasien, misalnya pada panduan pengeboran, dan dapat bersifat invasif dan memerlukan proses sterilisasi, karena mereka dapat berkontak dengan cairan tubuh, membran, jaringan, dan organ dalam waktu terbatas. Kelas ini mencakup alat bedah dan alat ortodontik. Salah satu bisnis terbesar dan paling sukses dalam kelas ini menggunakan proses fotopolimerisasi VAT untuk menciptakan cetakan untuk pembentukan vakum pada alat penyesuai gigi ortodontik transparan. Ketika dimensi yang spesifik untuk setiap pasien digunakan, prosesnya mirip dengan implan dan model praoperasi dari pencitraan medis atau pemindaian 3D. Pemodelan 3D dapat dilakukan dengan mengacu pada model 3D anatomi pasien atau membuatnya dari awal jika geometri atau kesesuaian yang spesifik untuk pasien tidak diperlukan. Pasca-produksi mungkin meliputi penghilangan penyangga, perlakuan panas, pemesinan, dan sterilisasi. Alat, instrumen, dan bagian-bagian untuk perangkat medis biasanya dibuat dengan alur proses yang ditunjukkan pada gambar di bawah. Misalnya, proses dimulai dengan mengambil cetakan gigi pasien, pemindaian 3D, diikuti oleh pemodelan 3D, AM fotopolimerisasi VAT, pasca-produksi, dan menggunakan bagian yang dibuat sebagai cetakan untuk alat penyesuai gigi ortodontik transparan.
4. Medical Aids, Supportive Guides, Splints and Prostheses
Dalam kelas ini, bagian-bagian yang dibuat dengan manufaktur tambahan berada di luar tubuh, dan ini dapat dikombinasikan dengan peralatan standar untuk memungkinkan personalisasi. Dukungan jangka panjang dan pascaoperasi, panduan gerakan, fiksator, prostesis eksternal, soket prostesis, pelindung khusus, dan aplikasi ortopedi adalah contoh aplikasi dalam kelas ini. Proses dapat dimulai dari pencitraan medis yang diikuti oleh segmentasi, pemindaian 3D, atau pengukuran 3D yang dapat memberikan data langsung untuk digunakan dalam fase pemodelan 3D. Metode manufaktur alternatif untuk manufaktur tambahan sering kali menggunakan teknologi kontrol numerik komputer (CNC). Bagian-bagian mungkin memerlukan jenis-jenis pasca-produksi yang berbeda tergantung pada aplikasinya, seperti penghilangan penyangga, perlakuan panas, dan pengecatan atau pelapisan. Alur proses yang khas untuk alat bantu medis, panduan dukungan, pelindung, dan prostesis menggunakan manufaktur tambahan ditunjukkan pada gambar di bawah. Kasus contoh adalah dukungan eksternal yang dipersonalisasi dan dapat digerakkan untuk patah pilon, di mana pemodelan 3D didasarkan pada pengukuran gerakan pergelangan kaki pasien dan penyesuaian bagian manufaktur tambahan untuk menempatkan engsel sehingga mengendalikan gerakan di bawah tekanan yang mendekati gerakan bebas pergelangan kaki.
5. Biomanufacturing
Biomanufaktur adalah kombinasi antara additive manufacture dan rekayasa jaringan. Bahan-bahan yang digunakan perlu kompatibel secara biologis dan seringkali aktif dengan tubuh, sehingga banyak jenis polimer, keramik, dan material komposit yang digunakan. Struktur berpori dengan kultur dan matriks 3D dapat mempengaruhi spesialisasi sel. Bahan-bahan tersebut dapat bersifat osteoinduktif, osteokonduktif, atau dapat diresorbsi . Bentuk-bentuk dapat dipersonalisasi sesuai dengan kecacatan yang ada. Untuk bentuk yang dipersonalisasi, geometri pasien perlu ditangkap menggunakan pencitraan medis atau pemindaian 3D. Pada fase pemodelan 3D, struktur mikro dan makro dimodelkan, dan struktur berpori sering digunakan untuk menarik sel dan pertumbuhan sel. Proses ini sering perlu dilakukan dengan kondisi steril atau bagian-bagian yang dibuat memiliki kemampuan untuk disterilkan setelah dicetak. Sebelum aplikasi akhir, mungkin juga diperlukan pertumbuhan sel in vitro atau in vivo. Gambar di bawah menunjukkan contoh pemasangan implan resorbable pada lantai orbita dengan mengacu pada geometri pasien menggunakan CT dan segmentasi, dilanjutkan dengan pemodelan 3D dan manufaktur tambahan implan. Setelah proses manufaktur, implan tersebut disterilkan.
Meskipun tidak diragukan lagi bahwa model medis adalah bantuan yang berguna dalam memecahkan masalah bedah yang kompleks, terdapat banyak kekurangan dalam teknologi AM yang ada terkait penggunaannya untuk menghasilkan model medis. Salah satu alasan untuk hal ini adalah karena peralatan AM awalnya dirancang untuk memecahkan masalah dalam pengembangan produk manufaktur yang lebih luas, dan bukan khususnya untuk memecahkan masalah medis. Oleh karena itu, perkembangan teknologi tersebut telah difokuskan pada peningkatan untuk memecahkan masalah produsen daripada masalah dokter dan ahli bedah. Namun, peningkatan teknologi AM yang baru-baru ini dan di masa depan dapat membuka pintu untuk jangkauan aplikasi yang lebih luas di industri medis. Masalah utama yang dapat mengubah kekurangan ini demi menggunakan AM meliputi:
● Kecepatan
Pembuatan model AM seringkali memerlukan waktu yang cukup lama, bisa mencapai satu hari atau bahkan lebih. Hal ini disebabkan karena data medis perlu melalui proses segmentasi dan pengolahan untuk mencocokkan dengan fitur anatomi yang diinginkan. Ironisnya, persiapan data ini kadang memakan lebih banyak waktu daripada proses pemrosesan sebenarnya menggunakan teknologi AM.
● Biaya
Menggunakan model AM dalam konteks pemecahan masalah manufaktur dapat memberikan manfaat yang signifikan dalam hal penghematan biaya produksi volume tinggi, bahkan jika hanya ada penghematan beberapa sen per unit. Namun, ketika membahas aplikasi manufaktur produk medis yang melibatkan kustomisasi massal, biaya mesin tidak menjadi faktor penentu utama. Sebagai contoh, dalam penggunaan model medis untuk diagnosis, perencanaan bedah, dan pengembangan prostetik, tujuannya adalah untuk mengoptimalkan waktu perencanaan oleh para ahli bedah serta meningkatkan kualitas, efektivitas, dan efisiensi proses tersebut. Meskipun masalah-masalah ini sulit diukur secara langsung dalam hal biaya, jelas bahwa hanya kasus-kasus yang lebih kompleks yang bisa membenarkan pengeluaran untuk pembuatan model tersebut.
● Ketepatan
Sejumlah proses AM sedang dalam tahap pengembangan untuk meningkatkan akurasi komponen yang dihasilkan. Namun, saat ini banyak aplikasi medis yang tidak membutuhkan tingkat akurasi yang sangat tinggi karena data yang digunakan dari sistem pencitraan 3D masih memiliki tingkat akurasi yang lebih rendah dibandingkan dengan mesin AM yang digunakan. Meskipun demikian, hal ini tidak berarti bahwa pengguna di bidang medis harus puas dengan tingkat akurasi yang rendah. Seiring dengan kemajuan teknologi CT dan MRI yang semakin akurat dan canggih, persyaratan untuk menggunakan AM dalam aplikasi medis akan menjadi lebih menantang.
● Bahan
Hanya sedikit jenis bahan polimer dalam AM yang dapat dianggap aman untuk digunakan di ruang operasi, dan jumlahnya semakin terbatas bagi bahan yang dapat ditempatkan di dalam tubuh. Mesin AM yang mampu menghasilkan bahan dengan sifat yang paling sesuai umumnya memiliki harga yang lebih tinggi. Selain itu, penggunaan sistem berbasis bubuk dalam AM juga memiliki tantangan tersendiri terkait potensi kontaminasi, sehingga membatasi aplikasi yang dapat digunakan dalam pembuatan model medis. Meskipun demikian, banyak produsen mesin AM saat ini telah mengembangkan berbagai bahan yang telah disetujui secara klinis untuk digunakan di ruang operasi.
● Kemudahan penggunaan
Mengoperasikan mesin AM umumnya membutuhkan tingkat keahlian teknis yang tinggi untuk menghasilkan model dengan kualitas yang baik. Terutama pada mesin yang lebih besar, kompleks, dan serbaguna, keahlian tersebut menjadi semakin penting. Namun, mesin-mesin yang lebih besar ini tidak selalu cocok untuk lingkungan laboratorium medis. Selain itu, persiapan data yang memerlukan keterampilan dalam penggunaan perangkat lunak tambahan juga menunjukkan bahwa setiap perusahaan medis yang ingin menggunakan AM harus melakukan investasi yang signifikan dalam pelatihan. Meskipun perangkat lunak merupakan tantangan umum di semua teknologi AM, kompleksitas pengaturan mesin, penanganan bahan, dan persyaratan perawatan umum yang sering kali terkait dengan mesin AM juga tidak membantu situasi tersebut.
b. Penggunaan Additive Manufacturing di Bidang Aerospace
Seperti yang telah disebutkan sebelumnya, industri kedirgantaraan merupakan salah satu industri yang telah lama menerapkan AM sejak teknologi ini diperkenalkan. Salah satu keuntungan utama penggunaan AM dalam aplikasi produksi di industri kedirgantaraan adalah kemampuannya untuk menghasilkan geometri rekayasa yang kompleks dengan langkah pemrosesan yang terbatas. Perusahaan-perusahaan dalam industri kedirgantaraan umumnya memiliki akses ke anggaran yang lebih besar dibandingkan dengan industri lainnya. Namun, hal ini sering kali diperlukan mengingat produk-produk yang dihasilkan harus memiliki kinerja yang tinggi.
1. Karakteristik yang Mendukung Additive Manufacturing (AM)
Manfaat signifikan dapat diperoleh jika komponen-komponen kedirgantaraan ditingkatkan dengan mempertimbangkan salah satu atau lebih dari karakteristik berikut ini:
a) Ringan
Segala sesuatu yang terbang memerlukan energi untuk mengangkatnya dari tanah. Semakin ringan komponen-komponen tersebut, semakin sedikit energi yang diperlukan. Ini dapat dicapai dengan menggunakan bahan-bahan ringan dengan rasio kekuatan terhadap berat yang tinggi. Bahan seperti titanium dan aluminium telah menjadi pilihan tradisional dalam industri kedirgantaraan. Selain itu, komposit yang diperkuat serat karbon juga semakin populer.
b) Tahan Suhu Tinggi
Pesawat terbang dan wahana antariksa beroperasi dalam berbagai suhu ekstrem, termasuk suhu tinggi dan rendah. Komponen mesin seringkali terkena suhu yang sangat tinggi, sehingga diperlukan solusi pendinginan inovatif. Bahkan komponen internal harus tahan terhadap api. Oleh karena itu, dalam aplikasi kedirgantaraan, bahan-bahan yang digunakan dalam AM perlu disesuaikan secara khusus untuk memenuhi persyaratan tersebut.
2. Geometri Kompleks
Aplikasi kedirgantaraan seringkali memerlukan komponen dengan fungsi ganda. Sebagai contoh, komponen struktural juga dapat berfungsi sebagai saluran atau bilah turbin mesin yang memiliki struktur internal untuk mengalirkan cairan pendingin. Selain itu, spesifikasi geometris komponen dapat ditentukan berdasarkan rumus matematika kompleks yang melibatkan aliran fluida dan lainnya.
3. Keuntungan Ekonomi
AM memungkinkan produksi dengan volume rendah yang ekonomis, yang sangat berguna di industri kedirgantaraan, karena tidak diperlukan pembuatan perkakas yang mahal. Desainer dan insinyur manufaktur tidak perlu merancang dan membuat cetakan, cetakan, atau peralatan khusus, serta tidak perlu menghabiskan waktu untuk perencanaan proses yang rumit seperti proses konvensional.
4. Komponen Digital
Banyak pesawat memiliki masa pakai yang sangat panjang, sehingga pabrikan harus menyediakan suku cadang untuk jangka waktu yang lama (20-50 tahun atau lebih). Dalam hal ini, penggunaan AM memungkinkan perusahaan untuk menyimpan model digital suku cadang. Hal ini lebih mudah dan lebih murah dibandingkan dengan menyimpan komponen fisik atau peralatan manufaktur dalam jangka waktu yang panjang.
5. Produksi Manufaktur
Semua perusahaan terkemuka dalam industri kedirgantaraan di Amerika Serikat dan Eropa telah lama mengejar aplikasi produksi menggunakan Additive Manufacturing (AM). Sebagai contoh, Boeing telah menggunakan puluhan ribu suku cadang AM di pesawat militer dan komersial mereka. Dilaporkan bahwa lebih dari 200 bagian yang berbeda digunakan pada setidaknya 16 model pesawat [18]. Hingga saat ini, bagian-bagian ini terutama terbuat dari polimer nonstruktural dan digunakan untuk aplikasi militer atau ruang angkasa. Untuk pesawat komersial, bagian-bagian polimer harus memenuhi persyaratan ketahanan terhadap api, sehingga adopsinya harus menunggu perkembangan bahan polimer tahan api menggunakan metode Powder Bed Fusion (PBF). Sementara itu, untuk bahan logam, proses kualifikasi material dan sertifikasi suku cadang membutuhkan waktu bertahun-tahun untuk dicapai. Selain memproduksi suku cadang, perusahaan-perusahaan kedirgantaraan juga mengembangkan bahan baru yang memiliki kinerja tinggi dalam logam dan polimer, serta metode pemrosesan yang lebih baik.
Salah satu contoh skala besar pertama dari aplikasi manufaktur produksi komponen logam menggunakan AM muncul dalam industri kedirgantaraan. Pada tahun 2012, GE membeli Morris Technologies sebagai bagian dari investasi besar mereka dalam AM logam untuk memproduksi komponen mesin turbin gas. Salah satu komponen yang paling menonjol adalah desain baru nosel bahan bakar untuk mesin turbofan CFM LEAP (Leading Edge Aviation Propulsion), seperti yang ditunjukkan pada Gambar dibawah. Desain nosel bahan bakar baru ini mengaplikasikan konsep konsolidasi suku cadang ke tingkat yang baru, dengan menggabungkan 18-20 suku cadang menjadi satu desain terintegrasi dan mengurangi penggunaan sambungan brazed dan operasi perakitan yang banyak. Desain baru ini diperkirakan memiliki masa pakai lima kali lipat dari desain sebelumnya, mengurangi beratnya sebesar 25%, dan menghasilkan penghematan biaya tambahan melalui optimalisasi desain dan proses produksi. Selain itu, nosel bahan bakar ini dirancang untuk mengurangi penumpukan karbon, sehingga membuatnya lebih efisien dalam penggunaan bahan bakar.
Airbus sedang melakukan penelitian mengenai aplikasi optimasi topologi untuk mengembangkan desain bagian yang jauh lebih ringan dibandingkan dengan desain yang cocok untuk proses manufaktur konvensional. Pada gambar dibawah terlihat braket engsel nacelle A320 yang awalnya dirancang sebagai bagian dari baja cor, namun telah direkayasa ulang untuk diproduksi menggunakan paduan titanium melalui metode Powder Bed Fusion (PBF) [20]. Kabarnya, dengan perubahan tersebut, berhasil mengurangi massa braket sebanyak 10 kg, yang menghasilkan penghematan berat sekitar 40%. Penelitian ini dilakukan sebagai bagian dari upaya yang lebih besar untuk membandingkan dampak lingkungan pada siklus hidup desain bagian tersebut.
c. Penggunaan Additive manufacturing di bidang Otomotif
Seperti yang telah disebutkan, industri otomotif menjadi salah satu pengguna awal teknologi manufaktur aditif, dan para profesional di perusahaan-perusahaan tersebut memimpin dalam pengembangan berbagai aplikasi AM dalam pengembangan produk. Industri otomotif secara konsisten menjadi pengguna terbesar AM, menyumbang sekitar 17% dari total pengeluaran AM pada tahun 2013. Meskipun demikian, industri otomotif masih berada di belakang industri mesin industri/bisnis (18,5%) dan produk konsumen/elektronik (18%), yang merupakan industri yang lebih besar dan luas dalam hal penggunaan AM.
Volume produksi di industri otomotif sering kali tinggi, mencapai angka 100.000 unit per tahun, AM seringkali dianggap terlalu mahal untuk produksi manufaktur massal, berbeda dengan industri kedirgantaraan. Oleh karena itu, sebagian besar produsen otomotif belum sepenuhnya mengadopsi penggunaan suku cadang AM pada model mobil produksi massal mereka. Namun, masih ada aplikasi AM di segmen niche yang perlu dieksplorasi.
Seperti yang telah disebutkan dalam sejarah perkembangannya, perusahaan otomotif dan pemasok mereka telah mengembangkan berbagai aplikasi prototyping cepat menggunakan AM. Selain itu, pemasok untuk industri otomotif menggunakan suku cadang AM untuk mendeteksi dan memperbaiki masalah dalam jalur perakitan mereka. Dengan menggunakan suku cadang AM untuk menguji operasi perakitan dan alat bantu, mereka dapat mengidentifikasi potensi masalah sebelum memulai produksi massal. Menghindari masalah dalam produksi dapat menghasilkan penghematan yang signifikan mengingat investasi yang diperlukan untuk mengganti lini produksi model mobil.
Dalam hal teknologi Powder Bed Fusion (PBF) untuk logam, Concept Laser, sebuah perusahaan asal Jerman, baru-baru ini memperkenalkan mesin X line 1000R yang memiliki ruang cetak yang cukup besar untuk membuat blok mesin V6 otomotif. Mesin ini dikembangkan dalam kerjasama dengan Daimler AG. Meskipun tidak jelas apakah pelanggan otomotif mereka akan menggunakan mesin ini untuk produksi blok mesin, Concept Laser mengklaim bahwa mesin ini dikembangkan dengan mempertimbangkan kemampuan produksi. Menurut Concept Laser, mesin X line 1000R mampu mencetak dengan kecepatan 65 cm3 per jam, yang merupakan kecepatan yang tinggi dibandingkan dengan beberapa mesin PBF logam lainnya. Selain itu, mesin ini dirancang dengan dua kotak bahan (kotak bubuk) pada meja putar tunggal, sehingga satu kotak bahan dapat digunakan untuk pembuatan bagian sementara kotak lainnya dapat digunakan untuk pendinginan, pelepasan bagian, pemanasan awal, atau kegiatan non-pembuatan bagian lainnya.
Untuk mobil yang khusus atau diproduksi dalam volume rendah, teknologi manufaktur aditif (AM) dapat menjadi pilihan yang ekonomis untuk beberapa bagian. Aplikasi ini dapat mencakup suku cadang khusus pada mobil mewah atau pengganti suku cadang pada mobil antik. Sebagai contoh, Bentley Motors memberikan contoh dalam Bab 17. Mereka menggunakan metode Powder Bed Fusion (PBF) polimer untuk membuat beberapa komponen interior khusus, seperti bezel, yang kemudian dilapisi dengan kulit dan bahan lainnya. Volume produksi Bentley biasanya kurang dari 10.000 mobil untuk model tertentu, sehingga memenuhi syarat sebagai produksi dalam volume rendah.
Local Motors adalah sebuah perusahaan kecil yang mengadopsi pendekatan crowdsourcing dan metode pengembangan kendaraan baru lainnya. Mereka berpartisipasi dalam proyek pengembangan kendaraan militer DARPA FANG, sebagai contoh. Mereka menggunakan teknologi AM ketika relevan untuk aplikasi mereka. Dalam inisiatif terpisah, mereka juga telah melakukan proyek desain mobil yang melibatkan partisipasi massa, dengan persyaratan bahwa sebagian besar mobil akan diproduksi menggunakan AM. Mereka berencana untuk membuat komponen bodi dan struktural menggunakan mesin ekstrusi bahan dengan kerangka besar yang dikembangkan oleh Oak Ridge National Laboratories, yang kemudian ditampilkan di International Machine Technology Show pada bulan September 2014.
Di antara organisasi balap, Formula 1 telah menjadi pelopor dalam mengadopsi teknologi AM. Awalnya digunakan untuk prototyping cepat, beberapa tim mulai menggabungkan bagian AM pada mobil balap mereka pada awal hingga pertengahan 2000-an. Biasanya, bagian yang menggunakan teknologi PBF adalah bagian polimer nonstruktural. Tim Formula 1 juga menggunakan model AM untuk pengujian di terowongan angin dengan model skala, serta untuk suku cadang pada mobil balap ukuran penuh. Tim dari organisasi balap lainnya, seperti Indy dan NASCAR, juga telah menjadikan AM sebagai aspek penting dalam proses pengembangan mobil mereka.