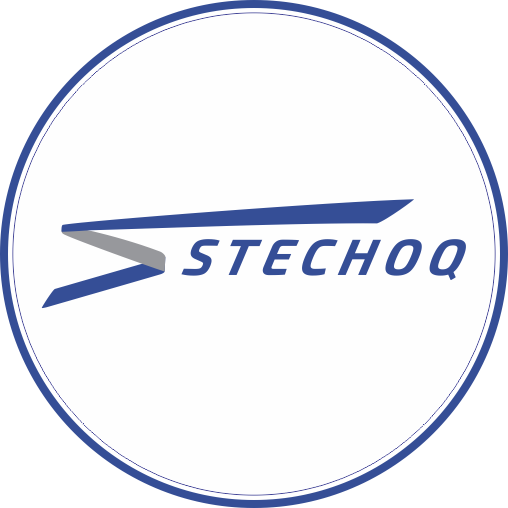
DAY 3
TEKNOLOGI ADDITIVE MANUFACTURING
Realisasi teknis dari manufaktur aditif dilakukan melalui proses manufaktur lapisan (juga disebut proses manufaktur lapisan langsung). Berdasarkan metode yang berbeda untuk menghasilkan lapisan padat dan menyatukan dan mengikat lapisan-lapisan yang bersebelahan untuk membentuk suatu bagian. Terdapat lima keluarga proses manufaktur lapisan yang digunakan dalam manufaktur aditif yang tersedia secara komersial. Mesin-mesin yang tersedia secara komersial yang sesuai dengan proses-proses ini disajikan bersama dengan contoh bagian-bagian yang umum.
Prinsip dasar manufaktur aditif (AM) sangat sederhana. Proses ini didasarkan pada data CAD 3D virtual yang merepresentasikan objek dalam bentuk padat. Data tersebut kemudian diiris menjadi lapisan-lapisan dengan ketebalan tertentu, mendekati bentuk permukaan bebas, dan lapisan-lapisan tersebut dibangun secara berurutan dengan ketebalan yang seragam.
Proses manufaktur yang sebenarnya (proses AM) fokus pada pembentukan dan pengikatan lapisan-lapisan fisik secara berurutan. Proses ini terdiri dari dua langkah yang berulang sampai bagian selesai:
1. Pembentukan satu lapisan tunggal dengan bentuk yang sesuai dengan kontur dan ketebalan lapisan yang telah ditentukan berdasarkan data irisan.
2. Pengikatan setiap lapisan baru di atas lapisan sebelumnya.
Seperti yang dapat dilihat secara teoritis dalam skema gambar di bawah, bagian yang dihasilkan juga menunjukkan tangga-tangga, yang merupakan karakteristik dari proses AM.
Ketebalan lapisan standar sekitar 0,1 mm tetapi dapat dikurangi menjadi 0,016 mm, sehingga meningkatkan presisi bagian dan jumlah lapisan serta waktu pembuatan. Hal ini juga tergantung pada bahan yang diproses, karena tangga-tangga yang dihasilkan membutuhkan lebih banyak usaha jika bahan yang diproses keras, misalnya logam dan keramik.
Pembentukan kontur setiap lapisan membutuhkan sumber energi yang menghasilkan efek fisik yang dipilih dan perangkat penanganan yang mengontrol koordinat x-y. Umumnya digunakan:
1. Laser dengan perangkat pemindaian tipe galvo, sakelar optik, atau sistem penanganan tipe gantry
2. Balok elektron
3. Kepala cetak dengan satu atau beberapa nozzle
4. Pisau, ekstruder, atau pemanas inframerah dengan plotter atau proyektor DLP.
Semua proses yang mungkin ada dapat diklasifikasikan ke dalam lima keluarga dasar proses manufaktur aditif (AM). Nama-nama yang tercantum dalam tabel adalah nama generik yang berfungsi sebagai deskripsi umum untuk semua variasi yang termasuk dalam kelompok tersebut. Nama generik harus dibedakan dari merek dagang yang diberikan oleh produsen untuk proses atau mesin tertentu.
Tabel Prinsip Fisik Generasi Lapisan dan Kontur serta Lima Keluarga Dasar Proses AM (Nama Generik)
Tabel Proses AM: Nama Generik, Nama Merek, dan Singkatannya
A. Polymerization
Proses polimerisasi (foto) adalah proses pemadatan resin monomer cair (seperti epoksi, akrilat, atau vinil eter) menggunakan radiasi ultraviolet. Ada berbagai variasi proses yang berbeda dalam cara radiasi UV dihasilkan dan bagaimana kontur dibentuk. Beberapa proses polimerisasi hanya menghasilkan pemadatan sebagian, sehingga menghasilkan "bagian hijau" yang memerlukan pengawetan tambahan untuk sepenuhnya sembuh. Proses pengerasan tambahan dilakukan setelah proses pembuatan menggunakan alat khusus yang disebut oven pengerasan. Oven ini dilengkapi dengan lampu pemancar UV untuk memastikan pemadatan yang lengkap dan merata pada seluruh bagian.
Selama proses pembuatan, proses polimerisasi membutuhkan support. Support ini digunakan untuk menjaga stabilitas seluruh bagian termasuk overhang, menyambungkan elemen yang tidak terhubung sementara, menyangga bagian di atas platform, dan mencegah distorsi dan perubahan bentuk. Support ini ditambahkan ke model CAD 3D menggunakan perangkat lunak otomatis dan harus dihapus secara manual setelah proses pembuatan selesai. Beberapa jenis support dapat dicuci secara otomatis menggunakan perangkat pembersih khusus.
1) Laser-Stereolithography (SL)
Stereolitografi bukan hanya proses AM tertua, tetapi juga masih menjadi proses yang paling detail. Proses ini ditemukan dan pertama kali dikomersialkan oleh 3D Systems, Rock Hill, SC, Amerika Serikat. Stereolitografi laser menghasilkan komponen dengan permukaan yang sangat halus dan detail yang fein. Bagian-bagian tersebut dibuat melalui polimerisasi lokal dari monomer yang semula dalam keadaan cair. Dengan bantuan sinar laser UV, polimerisasi mengubah cairan tersebut menjadi padat, membentuk lapisan-lapisan padat yang saling terkait. Sinar laser diarahkan oleh perangkat pemindai tipe galvo yang dikendalikan sesuai dengan kontur setiap lapisan. Contoh mesin yang umum digunakan adalah sebagai berikut.
Mesin stereolitografi laser terdiri dari ruang pembuatan yang diisi dengan bahan cair dan unit pemindai laser yang terletak di atasnya, yang menghasilkan kontur dalam sumbu x-y. Ruang pembuatan dilengkapi dengan platform pembuatan yang terpasang pada perangkat seperti elevator yang dapat bergerak ke arah pembuatan (sumbu z-). Bagian dibangun pada platform ini. Sinar laser secara simultan membentuk kontur dan memadatkan setiap lapisan, serta mengikatnya ke lapisan sebelumnya. Gerakan sinar laser dikontrol oleh data irisan untuk setiap lapisan dan diarahkan oleh pemindai.
Ketika sinar laser menembus permukaan resin, pemadatan segera terjadi. Ketebalan lapisan dapat disesuaikan tergantung pada reaktivitas dan transparansi resin, dengan menggunakan daya laser dan kecepatan pergerakan yang tepat.
Setelah proses pembangunan selesai, bagian tersebut dapat diampelas, dipoles, atau diberi lapisan pernis jika diperlukan. Tahap-tahap ini dikenal sebagai "finishing". Proses finishing merupakan tahapan yang independen dari proses AM dan tidak termasuk dalam bagian inti dari proses tersebut. Finishing hanya bergantung pada persyaratan pengguna untuk suku cadang dan mungkin terbatas oleh beberapa pembatasan yang terkait dengan penggunaannya.
Bahan yang digunakan dapat berupa resin epoksi dan akrilik, baik yang tidak terisi maupun yang terisi. Bahan yang tidak terisi cenderung memiliki stabilitas dan tahanan terhadap suhu tinggi yang lebih rendah. Namun, hal ini dapat ditingkatkan dengan menambahkan mikrosfer atau benda butiran seperti bola kaca, serat karbon, atau serbuk aluminium. Saat ini, bahan yang terisi seringkali mengandung partikel nano yang terbuat dari karbon atau keramik.
2) Polymer Printing and Jetting
Jika bahan yang dapat dipulihkan diterapkan melalui print head, proses ini disebut sebagai pencetakan polimer atau aliran polimer. Proses ini dikomersialkan oleh Objet, Rehovot, Israel. Meskipun dapat dianggap sebagai proses pencetakan 3D, namun karena bagian dibangun melalui polimerisasi monomer cair dengan pengerasan UV, ini sebenarnya adalah proses polimerisasi atau stereolitografi.
Desain mesin ini mirip dengan printer kantor 2D (lihat Gambar 2.6, sebelah kiri). Material langsung diaplikasikan ke platform pembangun melalui print head multi-nozel piezo-elektrik. Pemadatan bahan dilakukan secara bersamaan dengan menggunakan dua lampu UV berkinerja tinggi yang berjalan secara simultan, membentuk tirai cahaya ganda. Ketebalan lapisan yang dihasilkan hingga 0,016 mm, sehingga menghasilkan permukaan yang sangat halus. Platform bergerak ke arah-z untuk memproses lapisan-lapisan yang berdekatan. Proses ini berlanjut lapis demi lapis hingga bagian selesai terbentuk.
Bagian-bagian membutuhkan support selama proses pembangunan. support tersebut dihasilkan secara otomatis dan dibangun secara bersamaan oleh satu set nozzle kedua sehingga setiap lapisan terdiri dari bahan bangunan atau bahan support Akibatnya, support tersebut berupa bahan padat dan menghabiskan jumlah bahan yang cukup besar. Bahan support dapat dicuci tanpa meninggalkan bekas dalam proses pasca-proses yang sebagian besar otomatis.
Proses ini memanfaatkan monomer yang peka terhadap cahaya untuk membuat bagian plastik. Bahan ini tersedia dalam berbagai pilihan warna dan kekerasan. Dengan menggunakan teknologi eksklusif yang disebut "Poly-Jet Matrix" dan keluarga perangkat yang disebut "Connex", bagian-bagian dapat dibuat dari dua bahan yang berbeda yang menyerupai dua komponen dalam cetakan injeksi. Hal ini membuka kemungkinan untuk menghasilkan bagian multi-material di masa depan. Bagian-bagian ini umumnya berdinding tipis, terperinci, dan menunjukkan struktur berongga di dalamnya.
3) Digital Light Processing
Berbagai variasi proses polimerisasi foto ini menggunakan proyektor DLP komersial sebagai sumber cahaya UV. Proyektor tersebut memproyeksikan kontur lengkap dari penampang lapisan aktual dan memulai pemadatan secara bersamaan. Proses ini telah dikomersialkan dengan nama "Perfectory" oleh Envisiontec, Gladbeck, Jerman.
Proyektor dipasang di bagian bawah mesin. Resin disimpan dalam sebuah tangki yang terbuat dari kaca dan ditempatkan di bagian atas unit proyeksi. Penampang lapisan aktual diproyeksikan dari bawah dan ditampilkan pada permukaan bawah resin. Platform pembangunan yang terletak di bagian atas, yang diatur secara terbalik, menurunkan dirinya ke dalam resin dari atas, membentuk ruang dengan ketebalan satu lapisan antara permukaan transparan di bagian bawah dan permukaan resin itu sendiri. Setelah pemadatan lapisan, platform dinaikkan dengan ketebalan satu lapisan, menciptakan ruang untuk lapisan berikutnya. Karena tangki resin yang kecil, proses ini cocok untuk pembuatan part kecil. Hal ini memungkinkan perubahan material yang cepat dan kebutuhan pembuatan support. Berbagai jenis bahan plastik fotosensitif tersedia, termasuk bahan yang biokompatibel yang dapat digunakan untuk membuat alat bantu dengar atau master untuk prostesis gigi.
4) Micro Stereolithography
Micro stereolithography adalah sebuah teknologi yang digunakan dalam proses manufaktur aditif (AM) untuk mencetak objek dengan skala yang sangat kecil dan tingkat detail yang tinggi. Metode ini mirip dengan stereolitografi konvensional, tetapi dengan pemrosesan yang lebih halus dan presisi yang lebih tinggi.
Dalam micro stereolithography, objek dicetak dengan cara memadatkan lapisan demi lapisan dari material polimer cair yang fotosensitif menggunakan sinar laser ultraviolet (UV). Sinar laser diarahkan ke resin cair untuk mengeras dan membentuk polimer padat yang sesuai dengan desain yang diinginkan. Pergerakan sinar laser dikendalikan oleh sistem pemindai yang sangat akurat, memungkinkan pembentukan detail mikroskopis.
Kelebihan dari micro stereolithography adalah kemampuannya untuk mencetak struktur kompleks dengan resolusi yang sangat tinggi, bahkan mencapai skala mikro atau nano. Teknologi ini sering digunakan dalam bidang-bidang seperti mikroelektronika, biomedis, optik mikro, dan mikrofluidika. Contoh penggunaannya termasuk pembuatan komponen mikro, prototipe presisi tinggi, perangkat laboratorium mikro, dan implant medis yang disesuaikan.
Meskipun micro stereolithography memiliki kelebihan dalam resolusi dan detail, perlu dicatat bahwa proses ini mungkin memerlukan peralatan dan keterampilan khusus, serta bahan yang sesuai untuk mencapai hasil yang diinginkan.
B. Sintering and Melting
Sintering dan melting adalah dua proses dalam manufaktur aditif (AM) yang melibatkan pemadatan atau pencairan material untuk membentuk objek tiga dimensi. Sintering adalah proses di mana serbuk-serbuk material dikompres dan dipanaskan hingga suhu di bawah titik lelehnya. Selama proses sintering, serbuk-serbuk tersebut terikat satu sama lain secara termal dan mekanis, membentuk objek padat dengan kekuatan yang cukup. Sintering sering digunakan dalam teknik seperti Sintering Laser Selective (SLS) dan Metal Injection Molding (MIM) untuk mencetak objek dari logam atau keramik.
Melting, di sisi lain, melibatkan pencairan bahan mentah seperti logam atau polimer hingga menjadi bentuk cair. Material yang cair kemudian dicetak dan didinginkan kembali untuk membentuk objek yang solid. Metode yang menggunakan proses peleburan ini antara lain adalah Direct Metal Laser Sintering (DMLS) untuk logam dan Fused Deposition Modeling (FDM) untuk polimer.
Keduanya, sintering dan melting, merupakan proses penting dalam AM yang memungkinkan pembentukan objek dengan kekakuan dan kompleksitas geometri yang berbeda. Pemilihan metode yang tepat tergantung pada jenis material yang digunakan, kebutuhan desain, dan sifat akhir yang diinginkan untuk objek yang dicetak.
1) Laser Sintering Selective Laser Sintering (LS SLS)
Laser Sintering (LS) atau Selective Laser Sintering (SLS) adalah metode dalam manufaktur aditif (AM) yang menggunakan laser untuk memadatkan serbuk material menjadi objek tiga dimensi. Proses ini umumnya digunakan untuk mencetak objek dari serbuk logam, plastik, atau keramik.
Dalam Laser Sintering, serbuk material disebar secara merata di atas platform pembangunan. Kemudian, laser yang terfokus dipindai melintasi lapisan serbuk sesuai dengan pola yang ditentukan oleh data desain. Saat laser mengenai serbuk, panas yang dihasilkan menyebabkan serbuk meleleh dan menempel bersama untuk membentuk lapisan objek yang solid. Setelah lapisan selesai, platform turun sejauh ketebalan lapisan dan lapisan berikutnya dari serbuk ditambahkan. Proses ini berlanjut hingga objek selesai tercetak.
Metode Selective Laser Sintering (SLS) melibatkan penggunaan laser untuk secara selektif memadatkan serbuk hanya pada area yang diinginkan, sesuai dengan data desain. Hal ini memungkinkan pembentukan objek yang kompleks dan struktur internal yang rumit. Metode LS dan SLS ini digunakan dalam berbagai aplikasi, termasuk pembuatan prototipe, produksi batch, dan manufaktur massal dalam industri seperti otomotif, kedirgantaraan, dan kedokteran.
2) Laser Melting Selective Laser Melting (SLM)
Laser Melting (LM) atau Selective Laser Melting (SLM) adalah metode dalam manufaktur aditif (AM) yang menggunakan laser untuk melelehkan dan memadatkan serbuk logam secara selektif hingga membentuk objek tiga dimensi. Proses ini sering digunakan dalam pencetakan logam kompleks dengan tingkat akurasi yang tinggi.
Dalam Laser Melting, serbuk logam disebar secara merata di atas platform pembangunan. Laser yang sangat terfokus kemudian dipindai melintasi lapisan serbuk sesuai dengan pola yang ditentukan oleh data desain. Saat laser mengenai serbuk logam, panas yang dihasilkan sangat intens sehingga menyebabkan serbuk meleleh dan mencair. Setelah pendinginan, serbuk logam yang telah dilelehkan akan membentuk lapisan objek padat yang terikat dengan erat. Platform kemudian turun sejauh ketebalan lapisan dan lapisan berikutnya dari serbuk ditambahkan. Proses ini berulang hingga objek tiga dimensi selesai tercetak.
Metode Selective Laser Melting (SLM) memungkinkan pembentukan objek logam dengan struktur internal yang kompleks, termasuk aliran saluran dan struktur yang terintegrasi. Ini adalah teknologi yang populer dalam industri manufaktur, seperti kedirgantaraan, kedokteran gigi, dan industri otomotif, untuk pembuatan suku cadang yang presisi dan fungsional. Metode SLM juga memungkinkan penggunaan berbagai jenis logam, termasuk paduan logam yang sulit untuk diproses secara tradisional.
3) Electron Beam Melting
Electron Beam Melting (EBM) adalah sebuah proses manufaktur aditif (AM) yang menggunakan sinar elektron yang sangat terfokus untuk melelehkan dan memadatkan logam secara selektif, sehingga membentuk objek tiga dimensi. Dalam proses ini, sebuah aliran sinar elektron yang berasal dari kanon elektron yang terfokus dengan energi yang tinggi digunakan untuk memanaskan dan melelehkan serbuk logam.
Proses EBM mirip dengan Selective Laser Melting (SLM), tetapi menggunakan sinar elektron sebagai sumber panasnya. Serbuk logam ditempatkan di atas platform pembangunan, dan sinar elektron yang sangat terfokus kemudian dipindai secara selektif pada serbuk logam sesuai dengan pola yang ditentukan oleh data desain. Sinar elektron yang kuat ini dapat memberikan energi yang cukup untuk melelehkan serbuk logam dan membentuk lapisan objek yang padat.
EBM umumnya dilakukan dalam lingkungan vakum untuk menghindari interaksi dengan atmosfer dan mengurangi kontaminasi. Platform pembangunan secara bertahap diturunkan sejauh ketebalan lapisan yang diinginkan, dan serbuk logam baru ditambahkan untuk membentuk lapisan berikutnya. Proses ini berlanjut hingga seluruh objek selesai terbentuk.
Keunggulan dari Electron Beam Melting termasuk kemampuannya untuk mencetak objek dengan struktur internal yang kompleks dan geometri yang sulit dicapai dengan metode tradisional. EBM juga mampu menghasilkan objek logam dengan tingkat ketelitian dan kekuatan yang tinggi. Proses ini banyak digunakan dalam industri kedirgantaraan, kedokteran gigi, manufaktur komponen mesin, dan sektor-sektor lain di mana komponen logam berkualitas tinggi diperlukan.
C. Extrusion Fused Layer Modeling
Extrusion - Fused Layer Modeling (FDM) adalah sebuah proses manufaktur aditif (AM) yang menggunakan prinsip ekstrusi untuk membuat objek tiga dimensi. Dalam proses ini, seutas filamen termoplastik dipanaskan hingga meleleh dan ditekan melalui sebuah nozzle yang terkontrol secara komputer.
Pada awal proses, model objek yang akan dicetak disiapkan dalam format digital menggunakan perangkat lunak desain komputer-aided (CAD). Filament termoplastik, yang biasanya terbuat dari bahan seperti polimer atau PLA (Poly Lactic Acid), dimasukkan ke dalam mesin printer 3D melalui sebuah spool.
Selanjutnya, filamen dipanaskan hingga mencapai titik lelehnya dan ditekan keluar melalui nozzle yang bergerak secara presisi. Dalam perjalanan keluar, filamen yang meleleh ini ditempatkan secara lapisan oleh lapisan pada permukaan kerja yang ditentukan. Setiap lapisan yang ditempatkan cepat mendingin dan membentuk ikatan yang kuat dengan lapisan di bawahnya.
Secara umum, ukuran diameter filament yang digunakan dalam proses Fused Deposition Modeling (FDM) berkisar antara 0,1 mm hingga 0,25 mm. Platform kerja bergerak dalam arah sumbu-z, yang menentukan ketebalan setiap lapisan saat bahan dicetak di atas bagian yang sebagian sudah jadi. Dalam proses ini, support diperlukan untuk mendukung bagian yang menjorok. Support ini dibuat oleh nozzle kedua yang secara bersamaan mengekstrusi bahan pendukung plastik bersamaan dengan bahan bangunan.
Proses ini berlanjut secara bertahap, dengan platform pembangunan turun sedikit setiap kali lapisan selesai dicetak, memberikan ruang untuk lapisan berikutnya. Support sementara juga dapat dicetak untuk mendukung bagian yang menjorok atau berongga. Setelah objek selesai dicetak, support tersebut dapat dihapus dengan cara melepuhkannya atau menggunakan alat pemotong.
FDM memiliki beberapa keuntungan, antara lain kemampuannya untuk mencetak dengan cepat, biaya yang relatif rendah, dan ketersediaan berbagai jenis bahan termoplastik. Namun, hasil cetakan FDM mungkin memiliki tekstur permukaan yang kasar dan toleransi dimensional yang lebih rendah dibandingkan dengan metode AM lainnya.
Fused Deposition Modeling (FDM) telah banyak digunakan dalam berbagai industri, termasuk manufaktur, prototyping, pendidikan, dan hobi pencetakan 3D. Meskipun ada keterbatasan tertentu, FDM tetap menjadi salah satu metode pencetakan 3D yang paling populer dan terjangkau.
D. Powder-Blinder Bonding Three Dimensional Printing
Powder-Binder Bonding - Three Dimensional Printing (Drop on Powder Processes) adalah sebuah metode dalam proses manufaktur aditif di mana bahan serbuk digunakan sebagai bahan dasar untuk pembentukan objek. Dalam metode ini, lapisan tipis dari bahan serbuk diletakkan di atas platform kerja, dan kemudian sebuah cairan perekat (binder) diaplikasikan secara selektif di atas serbuk untuk membentuk lapisan yang solid. Proses ini berulang untuk setiap lapisan, dengan penambahan serbuk baru dan aplikasi binder yang akurat sesuai dengan desain objek yang diinginkan.
Setelah selesai proses pencetakan, objek yang terbentuk memiliki struktur pori-pori karena keberadaan serbuk yang belum terikat sepenuhnya. Untuk memperkuat objek, proses pengikatan dan pemadatan lanjutan mungkin diperlukan, seperti pemanasan atau perlakuan lainnya, tergantung pada bahan dan aplikasi yang digunakan.
Metode Powder-Binder Bonding - Three Dimensional Printing ini memungkinkan pembuatan objek yang kompleks dengan tingkat detail yang tinggi. Keuntungan dari metode ini termasuk kemampuan untuk menggunakan berbagai jenis serbuk dan binder yang sesuai dengan kebutuhan aplikasi tertentu.
1) Three Dimensional Printing Z-Corporation
Three Dimensional Printing - Z-Corporation adalah sebuah teknologi dalam proses manufaktur aditif yang dikembangkan oleh perusahaan Z-Corporation. Teknologi ini menggunakan metode powder-based untuk mencetak objek tiga dimensi.
Dalam Three Dimensional Printing - Z-Corporation, objek dicetak dengan mengaplikasikan lapisan tipis dari bahan serbuk menggunakan printer khusus. Setiap lapisan serbuk kemudian diikat bersama menggunakan sebuah cairan perekat yang disemprotkan secara selektif. Proses ini berulang untuk setiap lapisan, dengan lapisan-lapisan serbuk dan cairan perekat yang terus ditumpuk hingga objek selesai terbentuk.
Setelah selesai pencetakan, objek yang dihasilkan memiliki struktur pori-pori karena adanya bahan serbuk yang belum terikat sepenuhnya. Untuk memperkuat objek dan menghilangkan porositas, objek tersebut kemudian dapat diproses melalui tahap pengikatan dan pemadatan lanjutan seperti perlakuan panas atau penggunaan bahan tambahan.
Teknologi Three Dimensional Printing - Z-Corporation telah digunakan dalam berbagai industri seperti desain produk, arsitektur, dan rekayasa. Keuntungan dari metode ini adalah kemampuannya untuk mencetak objek dengan detail yang tinggi dan kecepatan produksi yang relatif cepat.
2) Three Dimensional Printing Prometal
Three Dimensional Printing - Prometal adalah sebuah teknologi dalam proses manufaktur aditif yang dikembangkan oleh perusahaan prometal. Teknologi ini juga dikenal sebagai Rapid Production Technology (RPT) atau Three Dimensional Printing with Metals.
Dalam Three Dimensional Printing - Prometal, objek tiga dimensi dicetak menggunakan bahan logam yang diproses dalam bentuk serbuk. Proses dimulai dengan penyebaran lapisan tipis serbuk logam pada platform kerja. Setelah itu, sebuah printer khusus mengaplikasikan cairan pengikat atau bahan perekat secara selektif pada serbuk logam sesuai dengan pola desain yang diinginkan.
Lapisan serbuk logam yang telah diberi cairan pengikat kemudian dikeringkan atau dikatalisasi untuk membentuk ikatan antarpartikel dan menghasilkan kekuatan struktural. Proses ini berulang untuk setiap lapisan, dengan serbuk logam dan cairan pengikat yang terus ditumpuk hingga objek selesai terbentuk.
Setelah pencetakan selesai, objek tiga dimensi yang dihasilkan kemudian menjalani tahap pascaproses seperti pemanasan, penyelesaian permukaan, dan penghilangan material pendukung jika diperlukan. Ini bertujuan untuk meningkatkan kekuatan, kualitas permukaan, dan akurasi geometri objek.
Teknologi Three Dimensional Printing - Prometal memungkinkan pencetakan objek logam dengan kompleksitas geometri tinggi dan keakuratan yang tinggi. Ini memungkinkan pembuatan prototipe cepat, produksi on-demand, dan manufaktur massal dari komponen logam yang rumit dan disesuaikan dengan kebutuhan spesifik pengguna.
3) Three Dimensional Printing Voxeljet
Three Dimensional Printing - Voxeljet adalah sebuah teknologi dalam proses manufaktur aditif yang dikembangkan oleh perusahaan Voxeljet. Teknologi ini juga dikenal sebagai Voxeljet Printing atau Voxel Printing.
Dalam Three Dimensional Printing - Voxeljet, objek tiga dimensi dicetak menggunakan bahan serbuk yang disebut material pengikat (binder material) dan serbuk pendukung (support material). Proses dimulai dengan menyebar lapisan tipis serbuk pada platform kerja menggunakan jet printer khusus.
Selanjutnya, printer mengaplikasikan material pengikat secara selektif pada serbuk, mengikat partikel-partikel serbuk bersama untuk membentuk lapisan objek yang diinginkan. Proses ini berulang untuk setiap lapisan hingga objek selesai terbentuk.
Setelah pencetakan selesai, objek tiga dimensi yang dihasilkan masih terikat dengan serbuk pendukung. Tahap pascaproses meliputi penghilangan serbuk pendukung dengan membersihkan atau mencuci objek, dan kemudian melakukan pemanasan atau pengeringan untuk memperkuat struktur objek.
Teknologi Three Dimensional Printing - Voxeljet memiliki keunggulan dalam mencetak objek dengan skala yang lebih besar dan kemampuan mencetak dengan cepat. Hal ini memungkinkan aplikasi dalam pembuatan prototipe industri, produksi cetakan pasir untuk pengecoran logam, dan pembuatan arsitektur skala besar. Dalam industri manufaktur, teknologi ini dapat digunakan untuk mencetak komponen yang kompleks dan berukuran besar dengan cepat dan efisien.
E. Layer Laminate Manufacturing (LLM)
Layer Laminate Manufacturing (LLM) adalah sebuah teknologi dalam proses manufaktur aditif yang digunakan untuk mencetak objek tiga dimensi dengan menggunakan lapisan-lapisan bahan lembaran. Teknologi ini juga dikenal sebagai Sheet Lamination atau Sheet Layering.
Dalam Layer Laminate Manufacturing, objek dicetak dengan cara menggabungkan dan merekatkan lapisan-lapisan bahan lembaran yang sesuai. Setiap lembaran biasanya terbuat dari bahan seperti kertas, plastik, logam, atau serat komposit. Proses dimulai dengan memotong atau memotong lembaran bahan sesuai dengan pola yang diinginkan.
Selanjutnya, lembaran bahan ditempatkan secara berurutan dan direkatkan satu sama lain menggunakan metode perekat atau pemanasan. Proses ini berulang untuk setiap lapisan hingga objek selesai terbentuk. Setelah pencetakan selesai, objek yang dihasilkan dapat dihaluskan, diperkuat, atau diproses lebih lanjut sesuai kebutuhan.
Layer Laminate Manufacturing memiliki keunggulan dalam kemampuan mencetak objek dengan biaya rendah dan menggunakan berbagai jenis bahan lembaran. Prosesnya juga relatif cepat dan dapat menghasilkan objek dengan kekuatan dan ketahanan yang baik. Namun, karena menggunakan bahan lembaran yang sudah ada, teknologi ini mungkin memiliki batasan dalam kompleksitas geometri objek yang dapat dicetak.
1) Laminated Object Manufacturing (LOM)
Laminated Object Manufacturing (LOM), adalah metode manufaktur aditif yang digunakan untuk membuat objek tiga dimensi dengan membangun lapisan-lapisan bahan lembaran yang direkatkan bersama.
Proses LLM dimulai dengan memotong lembaran bahan seperti kertas, plastik, atau logam sesuai dengan pola yang diinginkan. Lembaran tersebut kemudian ditempatkan secara berurutan dan direkatkan bersama menggunakan perekat atau pemanasan. Setelah satu lapisan selesai, lapisan berikutnya ditempatkan di atasnya dan direkatkan lagi. Proses ini diulang hingga seluruh objek selesai terbentuk.
Setelah objek selesai dicetak, surplus bahan lembaran yang tidak diperlukan dapat dihapus atau dipotong untuk menghasilkan bentuk yang diinginkan. Objek yang dihasilkan mungkin memerlukan tahap pembersihan dan penghalusan tambahan.
Keuntungan dari Layer Laminate Manufacturing (LLM) adalah kemampuannya untuk mencetak objek dengan biaya rendah, cepat, dan menggunakan berbagai jenis bahan lembaran. Metode ini juga dapat menghasilkan objek dengan ketahanan dan kekuatan yang baik. Namun, kompleksitas geometri objek yang dapat dicetak mungkin terbatas dibandingkan dengan teknologi manufaktur aditif lainnya.
2) Paper Lamination, MCOR Matrix
MCOR Matrix adalah salah satu merek yang menggunakan teknologi Layer Laminate Manufacturing (LLM) dengan fokus pada penggunaan kertas sebagai bahan dasar. MCOR Matrix menggunakan bahan kertas yang terjangkau dan ramah lingkungan untuk mencetak objek dengan kualitas yang baik.
Keuntungan dari Layer Laminate Manufacturing (LLM) atau Paper Lamination adalah biaya produksi yang rendah karena bahan dasarnya yang murah dan mudah didapat. Selain itu, bahan kertas juga dapat didaur ulang, sehingga metode ini dianggap lebih ramah lingkungan dibandingkan dengan beberapa teknologi manufaktur aditif lainnya. Namun, objek yang dihasilkan mungkin memiliki kekuatan yang lebih rendah dibandingkan dengan metode manufaktur aditif lain yang menggunakan bahan yang lebih kuat seperti logam atau plastik.
3) Plastic Laminate Printers
Plastic laminate printers adalah printer khusus yang digunakan untuk mencetak objek tiga dimensi menggunakan bahan laminasi plastik. Proses ini melibatkan penggunaan lembaran plastik yang telah dilaminasi sebagai bahan baku. Lembaran plastik tersebut kemudian dimasukkan ke dalam printer yang secara bertahap mencairkan dan menempelkan lapisan-lapisan plastik tersebut untuk membentuk objek yang diinginkan.
Plastic laminate printers menggunakan prinsip dasar Laminated Object Manufacturing (LOM) di mana lapisan-lapisan bahan plastik dilapisi dengan perekat dan ditempatkan satu per satu untuk membentuk objek akhir. Proses ini dapat dikendalikan melalui perangkat lunak yang memetakan pola dan ketebalan setiap lapisan yang akan dicetak.
Keuntungan menggunakan plastic laminate printers adalah kemampuan untuk mencetak objek dengan biaya rendah dan relatif cepat. Bahan plastik laminasi yang digunakan umumnya tersedia dalam berbagai warna dan kekerasan yang berbeda, memungkinkan pengguna untuk mencetak objek dengan variasi estetika dan kekuatan yang diinginkan.
Plastic laminate printers sering digunakan dalam berbagai aplikasi, termasuk pembuatan prototipe produk, model arsitektur, mainan, aksesori, dan dekorasi. Meskipun tidak sekuat atau seketat seperti bahan cetakan lainnya seperti logam atau resin, plastic laminate printers masih dapat memberikan hasil yang memadai untuk berbagai keperluan dan kebutuhan cetakan plastik.
4) LLM Machines for Metal Parts
LLM (Layer Laminate Manufacturing) Machines for Metal Parts adalah jenis mesin cetak 3D yang digunakan khusus untuk mencetak bagian logam menggunakan metode Laminated Object Manufacturing (LOM). Proses LLM untuk logam melibatkan penggunaan lembaran logam tipis yang dilaminasi sebagai bahan baku.
Dalam LLM Machines for Metal Parts, lembaran logam tipis dipotong sesuai dengan pola yang diinginkan dan dilapisi dengan lapisan perekat. Lembaran logam yang telah dilaminasi kemudian ditempatkan dan ditekan bersama-sama untuk membentuk lapisan-lapisan yang saling terikat. Proses ini diulangi untuk setiap lapisan hingga objek logam yang lengkap terbentuk.
Mesin LLM untuk bagian logam menawarkan beberapa keuntungan, termasuk kemampuan mencetak bagian dengan biaya rendah, kemampuan menghasilkan objek dengan kompleksitas geometri yang tinggi, dan kemampuan menggunakan berbagai jenis logam yang dapat dilaminasi, seperti aluminium, baja, atau titanium. Namun, perlu diperhatikan bahwa objek logam yang dicetak menggunakan LLM mungkin memiliki kekuatan dan ketahanan yang lebih rendah dibandingkan dengan bagian logam yang dibuat dengan metode manufaktur tradisional seperti pengecoran logam atau penempaan.
a. Ultrasonic Consolidation Solidica
Ultrasonic Consolidation (UC) adalah metode manufaktur aditif yang digunakan untuk mencetak bagian logam dengan menggunakan gelombang ultrasonik. Solidica adalah salah satu perusahaan yang mengkhususkan diri dalam teknologi Ultrasonic Consolidation.
Proses Ultrasonic Consolidation melibatkan penggabungan lapisan-lapisan logam dengan cara menghasilkan getaran ultrasonik pada permukaan logam yang telah dilapisi dengan lapisan perekat. Getaran ultrasonik ini menyebabkan gesekan dan tekanan yang cukup untuk menyatukan logam-logam tersebut. Pada saat yang sama, energi panas yang dihasilkan oleh gesekan ini menyebabkan logam-logam tersebut meleleh sedikit, menciptakan ikatan yang kuat antara lapisan-lapisan tersebut.
Solidica adalah salah satu perusahaan yang mengembangkan dan memasarkan sistem Ultrasonic Consolidation. Mereka menawarkan solusi dan layanan untuk aplikasi Ultrasonic Consolidation dalam berbagai industri, termasuk aerospace, otomotif, dan manufaktur umum. Solidica berfokus pada pengembangan teknologi Ultrasonic Consolidation yang canggih dan inovatif untuk memenuhi kebutuhan pelanggan dan memperluas aplikasi teknologi ini dalam dunia manufaktur.
F. Proses Lainnya
Selain proses additive manufacturing yang sudah dijelaskan, terdapat proses lainnya seperti aerosolprinting dan bioplotter.
1) Aerosolprinting
Ada sebuah proses menarik dengan potensi yang tinggi yang dikenal sebagai aerosolprinting. Proses ini dikembangkan dan diperkenalkan oleh Optomec, NM, AS dengan nama Maskless Mesoscale Materials Deposition (M3D).
Proses ini melibatkan aliran tetesan yang sangat halus, yang disebut aerosol, yang mengandung partikel ultra halus dengan diameter dalam kisaran nanometer. Aerosol ini kemudian diarahkan ke permukaan substrat sesuai dengan pola desain yang dibuat menggunakan perangkat CAD. Ketika aerosol dideposisikan di permukaan, fase cairnya menguap, meninggalkan partikel-partikel tersebut di tempatnya. Partikel yang digunakan dapat bervariasi, termasuk tinta fungsional, logam, keramik, plastik, dan bahkan sel hidup. Tergantung pada jenis material yang digunakan, proses ini mungkin memerlukan perlakuan lanjutan menggunakan laser.
Aerosolprinting menawarkan potensi yang sangat menjanjikan untuk aplikasi dalam bidang perangkat elektronik dan rekayasa jaringan. Namun, karena saat ini proses ini hanya cocok untuk mencetak tekstur permukaan 2 1/2 dimensi dan objek, dan bukan untuk mencetak objek 3 dimensi yang sebenarnya, beberapa orang mungkin tidak menganggapnya sebagai proses manufaktur aditif yang sesungguhnya.
2) Bioplotter
Seperti yang telah ditunjukkan dalam pengenalan mesin pengaliran polimer Objet dan mesin Optomec M3D, salah satu fitur unik yang ditawarkan oleh manufaktur aditif (AM) adalah kemampuan untuk memproses berbagai jenis material. Salah satu contoh mesin yang memungkinkan pemrosesan multi-material adalah Bioplotter 3D, yang merupakan merek dagang dari Envisiontec, Marl, Jerman.
Bioplotter 3D memungkinkan pemrosesan berbagai jenis bahan, mulai dari plastik seperti poliuretan dan silikon, hingga bahan tulang seperti hidroksiapatit, serta bahan obat-obatan seperti PCL (polycaprolactone), kolagen, atau fibrin yang digunakan untuk pencetakan organ atau fabrikasi jaringan lunak. Mesin ini dilengkapi dengan unit dispenser yang dapat dipanaskan atau didinginkan, dan dioperasikan oleh plotter 3-sumbu. Hingga lima jenis bahan dapat diproses secara simultan.
Proses pengerasan yang digunakan oleh Bioplotter 3D bervariasi tergantung pada jenis bahan yang digunakan, termasuk proses presipitasi, transisi fase dari cair ke padat, atau reaksi dua komponen. Beberapa bahan mungkin juga membutuhkan proses pasca pengolahan seperti sintering untuk mencapai kekuatan dan sifat yang diinginkan.
Memilih teknologi manufaktur aditif yang tepat tergantung pada sejumlah faktor yang perlu dipertimbangkan. Berikut adalah beberapa pertimbangan yang dapat membantu dalam memilih teknologi yang sesuai:
a. Tujuan aplikasi
Pertimbangkan jenis produk yang ingin diproduksi menggunakan teknologi manufaktur aditif. Apakah Anda membutuhkan prototipe cepat, alat produksi, bagian akhir jadi, atau aplikasi khusus seperti pencetakan medis atau industri.
b. Material yang digunakan
Periksa jenis material yang dapat diproses oleh setiap teknologi. Beberapa teknologi dapat bekerja dengan berbagai macam material seperti plastik, logam, keramik, atau bahan organik, sementara yang lain terbatas pada jenis material tertentu.
c. Skala dan ukuran
Pertimbangkan ukuran dan skala produk yang ingin Anda produksi. Beberapa teknologi cocok untuk mencetak bagian kecil dan kompleks, sedangkan yang lain dapat menangani objek besar.
d. Resolusi dan kecepatan
Evaluasi tingkat resolusi dan kecepatan yang diinginkan untuk aplikasi Anda. Beberapa teknologi mampu mencetak dengan resolusi tinggi tetapi mungkin membutuhkan waktu lebih lama, sementara yang lain dapat mencetak dengan cepat tetapi dengan resolusi yang lebih rendah.
e. Biaya
Pertimbangkan biaya peralatan, bahan, dan pemeliharaan yang terkait dengan setiap teknologi. Pastikan untuk menyesuaikan anggaran dengan kemampuan finansial Anda.
f. Keahlian dan sumber daya
Periksa apakah Anda memiliki keahlian dan sumber daya yang diperlukan untuk mengoperasikan teknologi tertentu. Beberapa teknologi lebih kompleks dan membutuhkan pelatihan khusus, sementara yang lain lebih mudah dioperasikan.
g. Fleksibilitas dan ketersediaan
Pertimbangkan fleksibilitas dan ketersediaan teknologi di pasar. Pastikan teknologi yang dipilih dapat memenuhi kebutuhan jangka panjang dan memiliki support yang memadai.
Dengan mempertimbangkan faktor-faktor di atas, Anda dapat membuat keputusan yang lebih terinformasi tentang teknologi manufaktur aditif yang paling cocok untuk kebutuhan Anda. Selalu disarankan untuk berkonsultasi dengan para ahli dan melakukan penelitian yang mendalam sebelum membuat keputusan akhir.