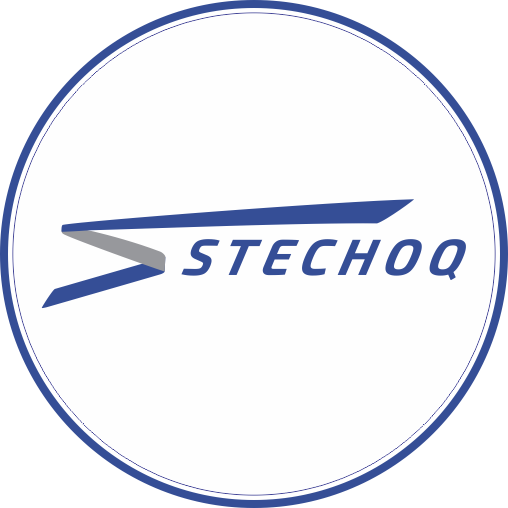
DAY 5
DESIGN FOR ADDITIVE MANUFACTURING 1
Seperti halnya permesinan CNC yang mempertimbangkan undercut dan jalur alat, atau bagian mold injeksi yang memperhitungkan sudut dan titik ejektor, terdapat beberapa elemen dasar yang terkait dengan pencetakan 3D. Bab ini memperkenalkan elemen-elemen tersebut, yang paling penting antara lain tinggi lapisan, penyusutan dan warping, support, dan fillet.
Setiap metode pencetakan 3D bergantung pada proses aditif yang mencetak bagian dalam lapisan-lapisan berturut-turut. Ketinggian setiap lapisan, juga dikenal sebagai resolusi sumbu-z, merupakan faktor yang mempengaruhi kualitas dan tampilan akhir suatu bagian. Umumnya, ketika ketinggian lapisan yang lebih kecil digunakan, bagian yang dicetak akan memiliki permukaan yang lebih halus dan detail yang lebih halus dengan tingkat ketepatan yang lebih tinggi. Namun, ini akan mengakibatkan waktu pencetakan yang lebih lama. Sebaliknya, ketinggian lapisan yang lebih tebal memungkinkan pencetakan yang lebih cepat, tetapi dapat menghasilkan lapisan-lapisan yang terlihat jelas pada permukaan bagian dan mengurangi tingkat ketepatan yang diinginkan. Hubungan antara waktu pencetakan dan ketinggian lapisan bersifat linier, yang berarti bahwa waktu yang dibutuhkan untuk mencetak bagian dengan ketinggian lapisan 50 mikron akan dua kali lebih lama daripada bagian dengan ketinggian lapisan 100 mikron.
Untuk kebanyakan aplikasi, ketinggian lapisan yang tercantum dalam Tabel 9.1 umumnya sudah memadai untuk setiap teknologi pencetakan 3D. Namun, dalam beberapa kasus di mana estetika atau kesesuaian menjadi faktor penting, seperti dalam desain bagian snap-fit atau bagian yang saling terkait, ketinggian lapisan dapat dikurangi untuk mencapai permukaan yang lebih halus. Namun, perlu diingat bahwa ini akan meningkatkan waktu pencetakan dan biaya produksi. Di sisi lain, untuk prototipe cepat di mana penampilan tidak terlalu penting, ketinggian lapisan yang lebih tebal dapat digunakan untuk mempercepat produksi bagian atau mengurangi biaya produksi. Namun, dalam kasus ini, garis-garis lapisan mungkin akan terlihat jelas kecuali jika ada proses pasca-pencetakan yang dilakukan.
Masalah umum yang sering terjadi dalam pencetakan 3D adalah warping dan penyusutan cetakan. Warping dan penyusutan biasanya disebabkan oleh dua mekanisme utama, yaitu suhu dan proses pengerasan (curing).
Penyusutan terjadi saat bagian yang dicetak mendingin setelah proses pencetakan. Ketika bahan cair mengalami pendinginan, cenderung mengalami kontraksi dan menyebabkan penyusutan pada bagian yang dicetak. Biasanya terjadi pada bahan termoplastik yang banyak digunakan dalam pencetakan 3D.
Warping, di sisi lain, terjadi ketika bagian yang dicetak mengalami deformasi atau distorsi bentuk. Biasanya terjadi ketika suhu pada bagian yang dicetak tidak merata selama proses pencetakan, atau ketika bagian tersebut mengalami perubahan suhu yang drastis setelah pencetakan. Deformasi ini dapat menyebabkan bagian yang dicetak melengkung, bergelombang, atau tidak rata.
Faktor suhu dan proses pengerasan memainkan peran penting dalam penyebab warping dan penyusutan. Perubahan suhu yang tidak merata selama pencetakan atau perubahan suhu yang tiba-tiba setelah pencetakan dapat menyebabkan stres dalam bahan dan mengakibatkan deformasi pada bagian yang dicetak.
Untuk mengatasi masalah warping dan penyusutan, beberapa tindakan pencegahan dapat diambil. Pengaturan suhu yang tepat selama pencetakan, penggunaan papan penyangga (heated build plate) untuk menjaga suhu bagian yang dicetak tetap stabil, penggunaan bahan cetak dengan sifat penyusutan rendah, dan penggunaan struktur pendukung (support structures) yang tepat adalah beberapa strategi yang dapat digunakan.
Dengan memahami mekanisme penyebab warping dan penyusutan ini, pengguna printer 3D dapat mengambil langkah-langkah yang diperlukan untuk mengurangi masalah tersebut dan mencapai hasil cetakan yang lebih baik.
1) Suhu
Tekanan residual adalah faktor utama yang menyebabkan penyusutan dan warping pada bagian yang dicetak. Tegangan residual terbentuk di dalam bagian tersebut sebagai akibat dari pendinginan yang tidak merata. Teknologi Material Extrusion (FFF) dan Powder Bed Fusion (SLS dan DMLS/SLM) menggunakan suhu tinggi dalam proses produksi komponen, yang membuat mereka rentan terhadap warping atau penyusutan yang disebabkan oleh perubahan suhu.
Ketika suatu area cetakan mengalami pendinginan, terjadi kontraksi. Kontraksi ini menyebabkan penyusutan pada bahan cetakan. Selain itu, kontraksi ini juga menarik daerah sekitarnya, menciptakan tekanan internal. Jika tekanan tersebut tinggi, bagian yang dicetak dapat melengkung atau bahkan, dalam kasus yang ekstrem, retak.
2) Curring
Proses fotopolimer seperti SLA/DLP dan Material Jetting tidak memerlukan suhu tinggi selama pencetakan, kecuali untuk pemanasan awal resin hingga suhu kerja yang optimal. Sebaliknya, warping dan penyusutan pada bagian terjadi saat lapisan-lapisan tersebut mengeras.
Setelah terpapar oleh sumber cahaya pengeras, setiap lapisan mengalami penyusutan saat proses pengentalan berlangsung. Ketika lapisan yang baru saja mengeras menyusut di atas lapisan sebelumnya yang telah mengeras sebelumnya (yang telah mengalami penyusutan), terjadi tekanan antara kedua lapisan tersebut. Akibatnya, tekanan tersebut menarik lapisan yang telah mengeras di sekitarnya, yang memicu terjadinya pengeritingan.
3) Mengurangi penyusutan dan warping
Terdapat beberapa metode yang dapat digunakan untuk mengurangi kemungkinan terjadinya warping atau penyusutan yang dapat merugikan sebuah bagian. Masalah pendinginan diferensial umumnya terkait dengan area besar dan tebal dari suatu bagian yang terhubung dengan fitur-fitur yang tipis.
● Menghindari fitur-fitur tipis karena cenderung mendingin lebih cepat, yang dapat menyebabkan mereka melengkung. Sebagai seorang desainer, penting untuk memastikan bahwa ketebalan dinding tetap konsisten di seluruh desain, hal ini akan membantu mengurangi kemungkinan terjadinya melengkung.
● Mencetak komponen dalam lingkungan dengan suhu yang terkontrol, seperti yang biasanya disediakan oleh printer industri, juga dapat membantu mengurangi kemungkinan terjadinya warping atau penyusutan.
● Perlu dihindari menggunakan permukaan yang besar dan datar, karena permukaan semacam itu rentan terhadap warping. Jika memungkinkan, pertimbangkan untuk merakit beberapa komponen sebagai alternatif jika permukaan yang besar dan datar sangat penting dalam desain.
● Terakhir, penggunaan dukungan (support) sangat penting untuk menjaga bagian cetakan yang berisiko warping agar tetap terikat pada pelat cetak. Memahami di mana dan seberapa banyak dukungan yang diperlukan akan membantu meningkatkan hasil cetakan. Hal ini sangat penting dalam teknologi seperti SLA/DLP dan DMLS/SLM.
Bagian yang dicetak dalam proses pencetakan 3D dibangun secara bertahap, lapis demi lapis. Tergantung pada teknologi pencetakan 3D yang digunakan dan kompleksitas model 3D, hal ini sering memerlukan struktur pendukung untuk mendukung setiap lapisan yang dibangun. Dalam sebagian besar teknologi, penggunaan struktur pendukung menjadi sangat penting untuk memastikan keberhasilan dan keakuratan cetakan model.
Ketika memilih teknologi pencetakan yang akan digunakan, penting untuk mempertimbangkan struktur pendukung dan bagaimana hal itu dapat mempengaruhi hasil akhir. Sebagian besar struktur pendukung dapat memberikan dampak negatif pada permukaan akhir, karena struktur tersebut perlu dihapus melalui tahap pasca-pemrosesan. Proses penghapusan struktur pendukung ini dapat meninggalkan noda atau membuat permukaan menjadi kasar. Seperti yang telah dibahas dalam Bagian 1, beberapa teknologi seperti FFF dan Material Jetting menawarkan struktur pendukung yang dapat larut, yang membuat penghapusan struktur pendukung menjadi lebih mudah. Pada teknologi berbasis bubuk atau pasir, struktur pendukung umumnya tidak diperlukan kecuali pada pencetakan logam.
Secara umum, struktur pendukung ditempatkan di bawah model sehingga permukaan yang terlihat menghadap ke atas memiliki kualitas akhir yang lebih baik. Jika estetika atau kesesuaian model menjadi faktor penting, maka yang terbaik adalah mengorientasikan model sedemikian rupa sehingga permukaan yang paling kritis menghadap ke atas (dengan pengecualian untuk pencetakan SLS).
Fillet, juga dikenal sebagai lengkungan atau jari-jari, merupakan fitur yang umum digunakan dalam desain bagian yang akan dicetak menggunakan teknologi pencetakan 3D. Fillet memiliki beberapa fungsi, antara lain mengurangi konsentrasi stres pada sudut dan tepi, memfasilitasi proses pencetakan 3D, dan memudahkan pemisahan komponen dari pelat cetak, terutama dalam metode pencetakan FFF.
Sebagian besar teknologi pencetakan 3D menghasilkan "fillet alami" pada semua tepi dan sudut bagian. Misalnya, dalam metode FFF, fillet luar akan memiliki jari-jari yang sama dengan jari-jari nosel, sementara dalam metode SLS, biasanya terdapat fillet dengan jari-jari sekitar 0,4 mm (ukuran titik laser) pada semua tepi yang tajam.
Dalam merancang bagian yang akan dicetak 3D, disarankan untuk memasukkan fillet sebanyak mungkin. Radius minimal 2 mm dapat menjadi titik awal yang baik. Untuk tepi luar yang terhubung dengan pelat cetak, seringkali lebih baik menggunakan chamfer (peruncingan) dengan sudut 45 daripada fillet, karena chamfer tidak memerlukan struktur pendukung tambahan, seperti yang dijelaskan dalam.
Tabel berikut ini memberikan penjelasan tentang berbagai fitur yang umum digunakan dalam pencetakan 3D. Perlu diperhatikan bahwa tidak semua fitur yang tercantum dalam Tabel berlaku untuk semua teknologi pencetakan 3D. Sebagai contoh, dalam metode pencetakan FFF (Fused Filament Fabrication), lubang keluar seperti yang disebutkan dalam tabel tidak diperlukan.
Aturan ini penting untuk dipahami dan diterapkan agar proses pencetakan 3D dapat menghasilkan bagian yang berkualitas dan berfungsi dengan baik.
Penerapan aturan desain teknik yang terkait dengan toleransi dalam Manufaktur Additive melibatkan pemahaman terhadap kemampuan printer 3D, kompensasi toleransi pemrosesan dan pemodelan, mempertimbangkan faktor-faktor eksternal, serta menggunakan alat pengukuran yang sesuai. Dengan mematuhi aturan ini, desainer dapat menciptakan bagian yang akurat dan berkualitas tinggi dalam proses pencetakan 3D.
Sebagai contoh, jika terdapat lubang dengan diameter 20 mm dan toleransi keseluruhan sebesar 0,30 mm, maka bagian tersebut harus dirancang dengan dimensi ∅ 20 0,15 mm. Jika bagian tersebut dirancang dengan dimensi ∅ 20 + 0,20 / -0,10 mm, yang mungkin terlihat dapat diterima dari perspektif perancang, kontur luar bagian tersebut tidak akan terbentuk dengan benar menggunakan metode Manufaktur Additive. Untuk mengatasi masalah ini, konsep "digital-to-object" baru-baru ini diperkenalkan.
Konsep "digital-to-object" mengacu pada pemahaman bahwa desain digital yang tepat akan menghasilkan objek fisik yang diinginkan dalam Manufaktur Additive. Oleh karena itu, penting bagi desainer untuk memahami batasan teknis dan kemampuan printer 3D yang digunakan. Dengan mempertimbangkan toleransi yang sesuai dalam desain, desainer dapat mencapai hasil akhir yang sesuai dengan harapan dan meminimalkan kesalahan atau cacat dalam bagian yang dicetak.
Aturan desain teknik yang terkait dengan kebebasan desain dalam Manufaktur Additive memberikan peluang bagi desainer untuk menciptakan bentuk dan struktur yang kompleks, geometri internal yang rumit, dan bentuk yang tidak terbatas. Hal ini membuka pintu bagi inovasi desain yang lebih besar, pengurangan berat komponen, penggunaan material yang efisien, serta produksi partai kecil atau kustom dengan biaya yang lebih rendah. Dengan pemahaman dan pertimbangan yang tepat terhadap faktor teknis yang terkait, desainer dapat sepenuhnya memanfaatkan potensi kebebasan desain yang ditawarkan oleh Manufaktur Additive.
Aturan desain teknik dalam Manufaktur Additive yang berkaitan dengan relative fit bertujuan untuk memastikan bahwa bagian-bagian yang dicetak dalam AM dapat dipasang dengan presisi dan memiliki kecocokan yang baik dengan bagian lainnya. Dengan memperhatikan dimensi, toleransi, kekuatan, orientasi pencetakan, dan desain antarmuka yang sesuai, dapat diciptakan komponen yang terintegrasi dengan baik dan berfungsi optimal dalam aplikasi akhir.
Dalam hal ini, kecocokan relatif yang akurat menjadi prioritas. Untuk memastikannya, bagian-bagian ditempatkan secara dekat di ruang pencetakan dan sejajar satu sama lain sebisa mungkin, dengan meninggalkan celah sekitar 0,10 hingga 0,20 mm. Hal ini memastikan bahwa bagian-bagian yang berdekatan akan pas dengan baik, tanpa memperhatikan apakah mereka memiliki kontur yang sederhana atau kompleks. Bahkan jika terjadi distorsi selama proses pencetakan, kecocokan bagian-bagian tersebut tidak akan terpengaruh.
Beberapa aturan desain teknik yang berkaitan dengan relative fit dalam AM antara lain:
1) Dimensi dan toleransi, untuk memastikan bahwa bagian-bagian yang akan digabungkan memiliki kecocokan yang baik.
2) Kekuatan dan fungsionalitas, bagian-bagian yang akan digabungkan harus dirancang sedemikian rupa sehingga kekuatan dan fungsionalitasnya tetap terjaga setelah penggabungan.
3) Orientasi pencetakan, orientasi bagian saat dicetak dalam AM dapat mempengaruhi relative fit. Perlu mempertimbangkan orientasi cetak yang optimal untuk memastikan kecocokan yang baik antara bagian-bagian yang akan digabungkan. Orientasi cetak yang salah dapat menyebabkan deformasi atau penyusutan yang dapat mempengaruhi relative fit.
4) Desain antarmuka, desain antarmuka atau interface antara bagian-bagian yang akan digabungkan harus diperhatikan dengan baik. Ini melibatkan pemikiran tentang bentuk, kehalusan permukaan, dan fitur-fitur khusus yang diperlukan untuk memastikan kecocokan yang baik dan koneksi yang kuat antara bagian-bagian tersebut.
Dalam Manufaktur Additive, terdapat aturan desain teknik yang berkaitan dengan fleksibilitas, engsel, dan snap fit untuk menciptakan bagian-bagian yang berfungsi dengan baik dan sesuai dengan kebutuhan aplikasi. Dalam merancang bagian-bagian tersebut, perlu dipertimbangkan bentuk, orientasi, ketebalan, lebar, toleransi, desain geometri, dan pemilihan bahan yang sesuai. Dengan mematuhi aturan-aturan ini, dapat menciptakan fleksibilitas, engsel, dan snap fit yang optimal dalam bagian-bagian yang dicetak dalam Manufaktur Additive.
Berikut ini beberapa aturan desain teknik yang terkait dengan fleksibilitas, engsel, dan snap fit dalam Manufaktur Additive:
1) Fleksibilitas (Flexures)
1. Bentuk dan orientasi
Desain fleksibilitas harus mempertimbangkan pemilihan bentuk dan struktur geometris yang tepat untuk memungkinkan deformasi elastis yang diinginkan.
2. Ketebalan dan lebar
Ketebalan dan lebar fleksibilitas harus dipilih dengan hati-hati untuk memastikan bahwa bagian tersebut memiliki kekuatan yang cukup untuk menahan beban yang dikenakan, sambil tetap memberikan tingkat fleksibilitas yang diinginkan.
3. Material
Bahan-bahan yang memiliki modulus elastisitas yang lebih rendah atau kemampuan deformasi yang lebih baik biasanya lebih cocok untuk menciptakan fleksibilitas yang diinginkan.
2) Engsel (Hinges)
1. Desain geometri
Engsel pada bagian-bagian yang dicetak harus dirancang sedemikian rupa sehingga dapat berfungsi sebagai titik putar atau sumbu rotasi yang stabil. Desain geometri harus memperhatikan radius lengkung dan sudut yang sesuai untuk memastikan engsel berfungsi dengan baik.
2. Toleransi
Toleransi harus diperhitungkan dengan cermat untuk memastikan bahwa engsel dapat bergerak dengan lancar dan tanpa hambatan. Toleransi yang terlalu ketat dapat menyebabkan gesekan berlebih dan menghambat gerakan engsel.
Dimensi celah antara bagian-bagian engsel bergantung pada orientasinya. Jika engsel berada di area x/y, nilai yang telah terbukti efektif adalah antara 0,3 hingga 0,5 mm, seperti yang ditunjukkan pada Gambar "A". Untuk engsel yang berada di area z, direkomendasikan antara 0,5 hingga 0,6 mm, sesuai yang ditampilkan pada Gambar "B".
Selain itu, dimensi absolut dan posisi engsel juga harus diperhatikan. Ini mencakup diameter pin dan sumbu engsel, panjang total engsel seperti yang ditampilkan pada Gambar "C", serta ketebalan dinding atau volume bagian. Bagian dengan volume yang lebih besar yang menyimpan panas dan mendukung partikel yang menempel memerlukan pembersihan yang lebih intensif. Hal yang sama berlaku jika engsel secara keseluruhan cenderung miring.
3) Snap Fit
1. Desain fitur
Desain fitur-fitur ini harus mempertimbangkan geometri, ukuran, dan toleransi yang sesuai untuk menciptakan koneksi snap yang kuat. Ketebalan dinding snap-fit tidak boleh kurang dari 0,5 mm, dan ruang gerak bebas harus sebesar mungkin agar tidak memberikan beban yang berlebihan pada bagian tersebut. Sementara itu, sambungan film harus memiliki ketebalan dinding 0,5 mm. Variasi dalam nilai-nilai ini tergantung pada pengalaman yang didapat.
2. Material
Pemilihan bahan yang tepat juga penting dalam snap fit. Bahan yang memiliki ketangguhan yang baik dan daya rekat yang cukup dapat memberikan koneksi snap yang kuat dan tahan lama.
Berikut ini adalah beberapa aturan desain teknik terkait dengan orientasi dan pengencangan dalam Manufaktur Additive yang dapat berperan penting dalam mencapai hasil pencetakan yang optimal:
1) Orientasi pencetakan
Memilih orientasi yang tepat untuk bagian yang akan dicetak dapat mempengaruhi kekuatan dan sifat mekanik yang diinginkan. Orientasi yang optimal dapat membantu menghindari kelemahan struktural dan meningkatkan kualitas cetakan.
2) Pengencangan
Pengencangan yang baik pada bagian yang dicetak sangat penting untuk menjaga stabilitas dan mencegah deformasi selama proses pencetakan. Pengencangan yang tidak memadai dapat mengakibatkan bagian yang tidak rata, melengkung, atau cacat.
3) Pertimbangkan sifat material
Memahami sifat material yang digunakan dalam pencetakan 3D sangat penting dalam menentukan orientasi dan pengencangan yang tepat. Beberapa material mungkin lebih rentan terhadap deformasi atau perubahan dimensi selama proses pencetakan.
4) Dukungan yang diperlukan
Memperhitungkan dukungan atau struktur pendukung yang diperlukan untuk bagian yang kompleks atau memiliki overhang yang signifikan adalah langkah penting. Dukungan yang tepat dapat membantu menjaga integritas bagian selama proses pencetakan dan kemudian dapat dihapus setelah selesai.
5) Pengujian dan optimalisasi
Melakukan uji coba dan iterasi pada desain sebelum pencetakan massal dapat membantu mengidentifikasi masalah potensial terkait orientasi dan pengencangan. Dengan mengoptimalkan desain berdasarkan hasil pengujian, dapat mencapai hasil pencetakan yang lebih baik.
Perlu diperhatikan bahwa aturan desain teknik untuk drilling, gaps, pins, dan walls dalam Manufaktur Additive dapat berbeda-beda tergantung pada teknologi pencetakan yang digunakan, bahan yang digunakan, dan kebutuhan aplikasi spesifik.
Berikut adalah beberapa aturan desain teknik terkait drilling, gaps, pins, dan walls dalam Manufaktur Additive:
1) Drilling (bor)
1. Ukuran dan geometri
Pastikan bahwa diameter, kedalaman, dan kemiringan lubang sesuai dengan kebutuhan fungsional dan kekuatan struktural bagian tersebut. Sebagai pedoman umum, saat menggunakan proses sintering laser untuk poliamida, diameter lubang sebaiknya tidak kurang dari 0,5 mm agar dapat terdeteksi dengan cukup baik (meskipun kualitasnya mungkin tidak optimal) jika ketebalan dinding kurang dari atau sama dengan 0,30 mm. Namun, jika ketebalan dinding lebih besar dari 0,6 mm, diameter minimal yang dapat terdeteksi secara akurat meningkat menjadi 0,70 mm.
2. Dukungan dan orientasi
Lubang bor mungkin memerlukan dukungan selama pencetakan untuk mencegah kemiringan atau deformasi. Oleh karena itu, orientasi dan penempatan yang tepat harus dipertimbangkan agar dukungan dapat diberikan secara efektif.
2) Gaps
1. Ukuran dan toleransi
Ketika merancang celah (gaps) dalam bagian, pastikan untuk memperhatikan ukuran dan toleransi yang diperlukan. Jarak antara dua permukaan yang berdekatan harus direncanakan dengan cermat untuk memenuhi kebutuhan fungsional dan perakitan akurat bagian tersebut.
2. Kebersihan permukaan
Pastikan bahwa permukaan celah bersih dan bebas dari sisa material atau cacat cetakan. Hal ini dapat memastikan kualitas dan keakuratan perakitan bagian yang melibatkan celah tersebut.
3) Pins
1. Dimensi dan kekuatan
Saat merancang pin (pen), perhatikan dimensi yang tepat dan kekuatan yang diperlukan. Pastikan bahwa diameter dan panjang pin cukup untuk menyediakan sambungan yang kuat dan stabil antara bagian yang berbeda.
2. Posisi dan orientasi
Penempatan dan orientasi pin harus direncanakan dengan hati-hati agar dapat memastikan kesesuaian dan kekuatan perakitan yang diinginkan. Pertimbangkan faktor seperti beban yang diterima dan kebutuhan aksesibilitas saat menentukan posisi dan orientasi pin.
4) Walls (dinding)
1. Ketebalan dan kekuatan
Ketika merancang dinding dalam bagian yang akan dicetak, pertimbangkan ketebalan yang tepat untuk memenuhi kekuatan struktural yang diperlukan.
2. Struktur internal
Dalam beberapa kasus, dinding dapat memiliki struktur internal untuk meningkatkan kekuatan dan efisiensi material. Pertimbangkan penggunaan pengisi (infill) atau struktur bantu lainnya untuk mengoptimalkan kinerja dinding.
Kubus ini memiliki dinding luar dengan ketebalan 2 mm dan tapak dengan luas 3 cm2. Tinggi kubus sama dengan luas tapaknya. Di bagian dasar kubus, terdapat dinding dan pin yang berdiri bebas dengan ketebalan dinding masing-masing 5, 2, 1, 0,5, dan 0,2 mm. Penutup kubus dilengkapi dengan celah dan lubang yang sesuai ketika diletakkan terbalik di pangkalan. Terdapat jarak bebas sebesar 0,1 mm yang memungkinkan kecocokan jika semua bagian diproduksi dengan benar. Diameter lubang sebesar 0,2 mm dan ketebalan dinding yang dimaksud tidak dapat diproduksi secara keseluruhan, sementara lubang dengan diameter 0,5 mm harus mengalami kalibrasi sebelumnya untuk memastikan hasil yang dapat diandalkan.
Dinding yang berdiri bebas memiliki tingkat reproduksi yang sedikit lebih baik daripada pin. Dalam hal ini, dinding dengan ketebalan 0,5 mm dan bahkan pin dengan ketebalan 0,2 mm dapat diproduksi jika prosesnya dikalibrasi dengan benar dan penyelesaiannya dilakukan secara hati-hati.
Semua data ini tergantung pada kalibrasi dan penanganan yang profesional dari mesin. Mesin stereolitografi laser yang telah dikalibrasi dengan baik dapat menghasilkan komponen dengan jarak dinding antara saluran tembus sebesar 0,05 mm, terutama jika ditempatkan di tengah platform build untuk mengurangi masalah pemindaian. Sebagai contoh, gambar 5.10 menunjukkan contoh perangkat mikrofluida yang akurat.