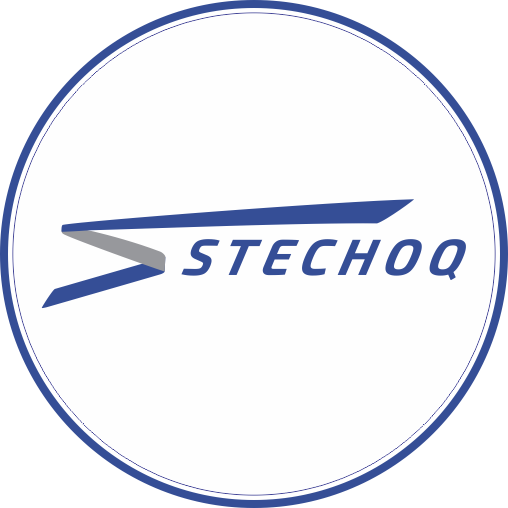
DAY 9
PASCA PEMROSESAN
Pasca-pemrosesan pada proses manufaktur aditif (AM) umumnya melibatkan serangkaian langkah yang dilakukan setelah pembuatan komponen untuk meningkatkan bentuk, kecocokan, dan/atau fungsi yang diinginkan. Teknik pasca-pemrosesan yang digunakan dapat berbeda-beda tergantung pada metode AM yang digunakan. Dalam kesempatan ini, akan dibahas beberapa teknik pasca-pemrosesan yang dapat digunakan untuk meningkatkan komponen atau mengatasi keterbatasan AM. Beberapa teknik tersebut antara lain:
Langkah penting dalam AM karena dalam proses cetak, support sering kali diperlukan untuk menjaga stabilitas komponen saat dicetak. Setelah pencetakan selesai, support tersebut perlu dihapus agar komponen akhir memiliki bentuk dan permukaan yang diinginkan. Support dalam AM dapat dibedakan menjadi dua kategori utama: (a) dukungan alami, yang terbentuk secara alami sebagai produk sampingan selama proses pencetakan, dan (b) dukungan sintetis, yaitu struktur kaku yang dirancang dan dibuat khusus untuk mendukung, menahan, atau memasang bagian yang sedang dicetak pada platform pembangunan.
Belakangan ini, telah terjadi perkembangan dalam teknik penghilangan bubuk otomatis. Teknik ini dapat berupa peralatan mandiri atau terintegrasi di dalam ruang cetak. Beberapa mesin pencetak dengan pemrosesan berikat, seperti ZCorp (sekarang Sistem 3D), telah dilengkapi dengan kemampuan penghilangan bubuk otomatis. Selain itu, beberapa produsen mesin pencetak PBF logam juga mulai mengintegrasikan teknik penghilangan bubuk semi-otomatis dalam mesin mereka. Tren saat ini menunjukkan bahwa di masa depan, banyak mesin PBF dan mesin pencetak jetting akan mengadopsi berbagai bentuk penghilangan bubuk otomatis.
Dalam proses laminasi lembaran bond-then-form, yang digunakan oleh mesin Mcor, penghilangan bahan pendukung alami diperlukan sebelum bagian dapat digunakan. Namun, jika geometri bagian tersebut kompleks dengan fitur menonjol, rongga internal, saluran, atau fitur halus, proses penghilangan bahan pendukung dapat menjadi tugas yang memakan waktu dan membosankan. Untuk bagian yang memiliki rongga atau saluran tertutup, seringkali perlu dilakukan pemisahan lapisan model pada tingkat tertentu agar dapat mengakses fitur internal dan menghilangkan bahan pendukung yang berlebihan. Setelah proses penghilangan bahan pendukung selesai, bagian tersebut kemudian direkatkan kembali.
Proses manufaktur yang tidak menghasilkan support alami pada komponen memerlukan penggunaan support sintetis untuk fitur-fitur yang menggantung. Dalam beberapa kasus, seperti ketika menggunakan teknik PBF untuk logam, support sintetis juga diperlukan untuk mencegah distorsi. Support sintetis dapat dibuat menggunakan bahan konstruksi atau bahan sekunder. Pengembangan bahan support sekunder adalah langkah penting dalam upaya untuk menyederhanakan penghilangan dukungan sintetis, karena bahan-bahan ini dirancang agar lebih lemah, larut dalam cairan, atau meleleh pada suhu yang lebih rendah daripada bahan konstruksi.
i. Support yang Terbuat dari Bahan Cetakan
Dalam semua proses ekstrusi material, aliran material, dan fotopolimerisasi, diperlukan penggunaan dukungan untuk struktur yang tergantung dan untuk menghubungkan bagian ke platform cetakan. Karena proses ini umumnya digunakan untuk bahan polimer, dukungan dengan kekuatan rendah dapat dengan mudah dihapus secara manual. Jenis dukungan ini juga sering disebut sebagai dukungan yang dapat dipecahkan. Menghilangkan dukungan dari fitur yang menghadap ke bawah akan meninggalkan bekas di tempat dukungan sebelumnya terpasang. Oleh karena itu, permukaan ini mungkin perlu diamplas dan dipoles setelahnya. Gambar di atas mengilustrasikan teknik pelepasan dukungan yang dapat dipecahkan untuk bagian yang dibuat menggunakan proses ekstrusi material dan fotopolimerisasi.
ii. Support yang Terbuat dari Bahan Sekunder
Selama beberapa tahun terakhir, telah ada perkembangan dalam pengembangan berbagai bahan pendukung sekunder untuk mengurangi penghapusan manual dukungan padat dalam proses manufaktur. Dua teknologi awal yang menggunakan bahan pendukung sekunder adalah proses fotopolimerisasi lapisan cubital dan proses aliran bahan solidscape. Penggunaan bahan pendukung lilin memungkinkan struktur pendukung yang terbuat dari bahan tersebut ditempatkan dalam bak air hangat, sehingga melelehkan atau melarutkan lilin akan menghasilkan bagian akhir yang diinginkan. Sejak itu, penggunaan dukungan sekunder telah menjadi umum dalam proses ekstrusi material dan aliran material secara komersial. Dukungan sekunder juga telah diteliti dan digunakan dalam proses laminasi lembaran logam bentuk-kemudian-ikatan dan proses DED (Directed Energy Deposition).
Untuk bahan polimer, bahan pendukung sekunder yang umum digunakan adalah bahan polimer yang dapat dilelehkan dan/atau dilarutkan dalam pelarut berbasis air. Penggunaan aliran air atau getaran ultrasonik dapat mempercepat proses penghilangan dukungan. Di sisi lain, untuk bahan logam, bahan pendukung sekunder yang umum digunakan adalah paduan dengan suhu leleh yang lebih rendah atau paduan yang dapat dilarutkan secara kimia dalam pelarut, dengan catatan bahwa pelarut yang digunakan tidak boleh mempengaruhi bahan utama.
Terdapat beberapa peralatan yang dapat digunakan untuk mempermudah pasca-pemrosesan:
● Flush Cutters
Flush Cutters untuk memotong filament dan bahan tipis lain yang terkait dengan pencetakan 3D.
● Needle Nose Pliers
Needle Nose Pliers untuk membantu menghilangkan sisa filament dari nosel ekstruder panas, atau untuk mencapai tempat-tempat yang sulit dijangkau di dalam printer 3D.
● Scrapper
Scrapper ini dirancang dengan bilah yang sangat tipis, sehingga memungkinkan untuk dengan mudah meluncurkannya di bawah cetakan 3D.
● Alat Deburring
Digunakan untuk menghilangkan burrs atau taju-taju tajam pada permukaan atau tepi benda yang telah diproses.
● Cutting Mat
Untuk melindungi area kerja atau meja sehingga dapat melakukan pasca-pemrosesan cetakan dengan aman.
● Filing Tool (kikir)
Digunakan untuk merapikan atau menghaluskan permukaan benda kerja dengan cara mengikis material secara perlahan. Filing Tool sering digunakan dalam berbagai aplikasi, termasuk proses manufaktur aditif (AM), untuk menghilangkan ketidaksempurnaan, menghaluskan tepi, atau mengoreksi bentuk dari komponen yang dicetak.
● Sikat Kawat
Gunakan sikat kawat untuk membersihkan sisa filament dari nosel ekstruder atau tempat tidur cetak.
Ada beberapa metode umum yang digunakan untuk meningkatkan tekstur permukaan bagian yang dicetak, antara lain:
Metode ini melibatkan penggunaan media peledak, seperti butiran abrasif kecil atau kerikil, yang ditembakkan ke permukaan bagian. Peledakan permukaan membantu meratakan tekstur permukaan, menghilangkan sudut tajam, dan memberikan tampilan matte keseluruhan.
Pengamplasan basah melibatkan pencelupan bagian ke dalam larutan abrasif atau penggosokan dengan kertas pasir basah. Sedangkan pengamplasan kering menggunakan bahan abrasif seperti kertas pasir atau spons pengamplas. Pengamplasan membantu menghilangkan ketidakrataan dan meningkatkan kehalusan permukaan.
Metode ini melibatkan penggunaan bahan pemoles, seperti kain mikrofiber atau kain lembut lainnya, yang digosokkan secara manual ke permukaan bagian untuk meningkatkan kilau dan kehalusan.
Pengecatan permukaan dengan bahan seperti cyanoacrylate atau sealant dapat memberikan manfaat ganda. Selain menyegel porositas, lapisan cat dapat meratakan efek tangga dan memudahkan proses pengamplasan dan pemolesan.
Penggunaan bahan tambahan seperti polisher dan finishing compound dapat membantu meningkatkan kilau dan kehalusan permukaan.
Terdapat juga berbagai teknik lain yang dapat digunakan, seperti penggunaan mesin pengamplas otomatis, proses kimia, atau bahkan teknologi pemindaian permukaan untuk memperbaiki tekstur permukaan.
Meningkatkan akurasi dalam manufaktur aditif (additive manufacturing) melibatkan beberapa strategi dan tindakan yang dapat dilakukan, antara lain:
Setiap teknologi manufaktur aditif memiliki tingkat akurasi yang berbeda. Memilih teknologi yang sesuai dengan kebutuhan dan toleransi yang diinginkan dapat membantu meningkatkan akurasi hasil cetakan.
Mengoptimalkan parameter pencetakan seperti kecepatan cetak, suhu cetak, ketebalan lapisan, dan kepadatan infill dapat mempengaruhi akurasi cetakan. Eksperimen dan penyesuaian parameter dapat dilakukan untuk mencapai hasil yang lebih akurat.
Mesin pencetak perlu dikalibrasi secara teratur untuk memastikan akurasi yang konsisten. Ini melibatkan penyesuaian sumbu dan sistem pengendalian mesin, serta pemeriksaan dan kalibrasi sensor dan pemindai yang digunakan.
Mesin pencetak perlu dirawat dan dipelihara dengan baik untuk menjaga akurasi. Membersihkan dan melumasi komponen yang tepat, mengganti suku cadang yang aus, dan melakukan perawatan yang direkomendasikan oleh produsen dapat membantu menjaga performa dan akurasi mesin.
Memilih bahan cetak berkualitas tinggi yang memiliki stabilitas dimensi yang baik dapat meningkatkan akurasi cetakan. Memastikan konsistensi bahan cetak dari batch ke batch juga penting untuk hasil yang akurat.
Memperhatikan aspek desain yang dapat mempengaruhi akurasi, seperti toleransi, dukungan yang diperlukan, dan orientasi cetak, dapat membantu menghasilkan cetakan yang lebih akurat. Menggunakan perangkat lunak pemodelan 3D yang canggih juga dapat membantu memprediksi dan mengoptimalkan akurasi cetakan.
Melakukan pemeriksaan dan pengujian berkala terhadap cetakan yang dihasilkan dapat membantu mengidentifikasi dan memperbaiki kesalahan dan penyimpangan yang mungkin terjadi. Penggunaan alat pengukur dan teknik inspeksi yang tepat juga penting untuk memastikan akurasi hasil cetakan.
Dalam beberapa kasus, penggunaan dukungan dan struktur pengunci yang tepat dapat membantu menjaga ketelitian dan kestabilan komponen yang sedang dicetak.
Peningkatan estetika dalam manufaktur aditif (additive manufacturing) melibatkan serangkaian langkah dan teknik untuk meningkatkan tampilan visual dan estetika dari produk cetakan. Beberapa langkah yang dapat dilakukan untuk mencapai peningkatan estetika adalah sebagai berikut:
Memilih bahan cetak dengan sifat estetika yang baik, seperti kecerahan, kejernihan, atau kemampuan untuk mencapai hasil permukaan yang halus, dapat memberikan tampilan yang lebih menarik pada produk cetakan.
Mengoptimalkan parameter pencetakan seperti suhu cetak, kecepatan cetak, dan ketebalan lapisan dapat mempengaruhi hasil estetika. Eksperimen dengan parameter pencetakan dapat dilakukan untuk mencapai hasil yang lebih baik secara visual.
Memperhatikan aspek desain yang mempertimbangkan keindahan dan estetika, seperti bentuk, pola, detail, dan permukaan, dapat memberikan hasil cetakan yang lebih menarik secara visual. Menggunakan perangkat lunak pemodelan 3D yang canggih dapat membantu merancang produk dengan tampilan yang estetis.
Proses finishing seperti pengamplasan, pemolesan, atau lapisan permukaan dapat meningkatkan tampilan estetika produk cetakan. Metode seperti pengamplasan basah atau kering, penggunaan bahan pemoles, atau penerapan lapisan permukaan yang dekoratif dapat digunakan untuk mencapai hasil yang lebih estetis.
Penggunaan pewarna atau cat pada produk cetakan dapat memberikan tampilan yang lebih menarik dan estetis. Pewarnaan dapat dilakukan dengan menggunakan cat atau pigmen yang cocok dengan bahan cetak, sementara pengecatan dapat melibatkan penggunaan teknik seperti pengecatan semprot atau pengecatan tangan untuk mencapai hasil yang diinginkan.
Lapisan pelindung seperti lapisan clear coat atau lapisan pelindung khusus dapat diterapkan pada permukaan bagian untuk memberikan perlindungan tambahan, mencegah korosi, dan meningkatkan tahan lama tampilan estetika bagian.
Jika bagian terdiri dari beberapa komponen yang terpisah, teknik penyatuan seperti perekatan atau pengerjaan khusus dapat digunakan untuk menyatukan komponen-komponen tersebut secara estetis dan kuat.
Metode tambahan seperti embossing, engraving, atau aplikasi label dan stiker dapat digunakan untuk memberikan elemen dekoratif tambahan pada bagian. Hal ini membantu meningkatkan nilai estetika dan memberikan identitas visual khusus.
Memanfaatkan teknologi post-processing seperti penggunaan mesin penghalus permukaan, teknik pewarnaan khusus, atau metode finishing yang canggih dapat membantu mencapai hasil estetika yang lebih baik pada produk cetakan.
Akurasi dan penyelesaian permukaan pola yang dihasilkan melalui manufaktur aditif (AM) memiliki dampak langsung terhadap akurasi dan penyelesaian permukaan pada bagian akhir yang dibuat. Oleh karena itu, sangat penting untuk memberikan perhatian yang cermat guna memastikan bahwa pola memiliki tingkat akurasi dan penyelesaian permukaan yang sesuai dengan yang diinginkan pada bagian akhirnya. Selain itu, pola juga harus diubah skala untuk mengkompensasi penyusutan yang terjadi selama proses replikasi pola.
Bagian-bagian yang diproduksi melalui manufaktur aditif (AM) dapat langsung dicetak pada pohon cor atau ditambahkan secara manual ke pohon cor setelah proses AM. Gambar di atas menggambarkan pembuatan cincin menggunakan sistem aliran material. Pada gambar pertama, terlihat beberapa cincin yang ditempatkan pada platform produksi, dan setiap cincin didukung oleh struktur pendukung berwarna putih. Pada gambar kedua, terlihat gambar close-up dari pola cincin tersebut. Pada gambar ketiga, terlihat cincin logam yang masih terhubung dengan pohon cor. Dalam kasus ini, cincin tersebut ditambahkan ke pohon cor setelah proses AM, tetapi sebelum proses pengecoran dilakukan.
Metode pengikat termoseting dan (PBF) dapat digunakan untuk secara langsung membuat inti dan rongga cetakan pasir dengan mengikat pasir dalam bentuk yang diinginkan. Pendekatan langsung ini memiliki keuntungan, di antaranya adalah kemampuan untuk membuat inti dengan geometri kompleks yang sulit dicapai melalui metode lain, seperti yang ditampilkan dalam gambar di atas.
Sejak akhir tahun 1980-an, berbagai metode replikasi pola telah digunakan untuk mengubah prototipe cepat yang memiliki kelemahan pada saat itu menjadi bagian-bagian dengan sifat material yang berguna. Namun, dengan meningkatnya jumlah teknologi manufaktur aditif (AM) dan peningkatan daya tahan bahan yang dihasilkan, penggunaan proses replikasi pola semakin berkurang. Banyak orang lebih memilih untuk mencetak langsung bagian yang dapat digunakan jika memungkinkan. Meskipun teknologi AM dan bahan yang tersedia semakin maju, proses replikasi pola masih digunakan oleh lembaga jasa dan perusahaan yang membutuhkan suku cadang dari bahan tertentu yang tidak dapat diproses secara langsung melalui AM.
Salah satu metode replikasi pola yang umum digunakan adalah cetakan RTV (Room Temperature Vulcanization) atau cetakan karet silikon. Dalam cetakan RTV, pola AM diberi penanda visual, seperti pita berwarna, untuk menandai lokasi garis pemisahan saat membongkar cetakan. Kemudian, pelari, anak tangga, dan gerbang ditambahkan ke pola tersebut. Pola ditempatkan dalam kotak cetakan, dan bahan seperti karet dituangkan di sekitar pola untuk membentuk cetakan. Setelah pengerasan, cetakan karet tembus pandang padat dikeluarkan dari kotak cetakan. Cetakan karet kemudian dipotong menggunakan pisau sesuai dengan penanda garis pemisahan, dan pola asli dikeluarkan dari cetakan. Proses replikasi ini dapat diulang beberapa kali untuk membuat jumlah bagian yang diperlukan.
Dengan adanya proses replikasi pola ini, memungkinkan pembuatan bagian dengan geometri kompleks yang sulit dicapai menggunakan metode lain. Meskipun tidak lagi menjadi pilihan utama dalam industri AM, metode replikasi pola tetap menjadi opsi yang berguna dalam situasi khusus di mana diperlukan suku cadang dengan bahan tertentu yang tidak dapat diproses langsung melalui AM.
Teknik non-termal dapat digunakan dalam proses pemrosesan pasca-manufaktur tambahan untuk meningkatkan berbagai sifat dari bagian tersebut. Salah satu teknik yang digunakan adalah penyelesaian permukaan, yang melibatkan proses seperti penggosokan, pengamplasan, atau pengeblasan pasir untuk meningkatkan kualitas dan estetika permukaan bagian tersebut. Penyelesaian permukaan juga membantu mengurangi kekasaran permukaan dan menghilangkan tekstur yang tidak diinginkan.
Teknik non-termal lainnya adalah perlakuan kimia atau modifikasi permukaan. Ini melibatkan penggunaan agen kimia atau lapisan untuk mengubah sifat permukaan bagian tersebut. Misalnya, pengikisan kimia dapat digunakan untuk menghilangkan material secara selektif dan menciptakan pola atau tekstur permukaan khusus. Lapisan permukaan dapat diterapkan untuk meningkatkan ketahanan terhadap korosi, ketahanan aus, atau memberikan fungsionalitas lain yang diinginkan pada bagian tersebut.
Teknik pemrosesan pasca seperti shot peening atau laser peening juga digunakan untuk meningkatkan sifat mekanik dari bagian-bagian yang diproduksi tambahan. Teknik-teknik ini menciptakan tegangan tekan pada lapisan permukaan, meningkatkan kekuatan kelelahan dan ketahanan terhadap inisiasi dan penyebaran retakan.
Selain itu, teknik non-termal seperti getaran ultrasonik, perlakuan medan magnetik, atau agitasi mekanik dapat digunakan untuk meningkatkan kepadatan dan mengurangi porositas pada bagian yang diproduksi. Teknik-teknik ini membantu mencapai kepadatan material yang lebih tinggi, sifat mekanik yang lebih baik, dan mengurangi kerentanan terhadap cacat.
Dengan menggunakan teknik non-termal ini dalam pemrosesan pasca-manufaktur tambahan, sifat keseluruhan bagian dapat ditingkatkan, yang pada gilirannya meningkatkan kinerja, fungsionalitas, dan keandalan.
Setelah proses manufaktur aditif (AM), banyak bagian memerlukan pemrosesan termal untuk meningkatkan sifat-sifatnya. Pada teknik Directed Energy Deposition (DED) dan Powder Bed Fusion (PBF) untuk logam, pemrosesan termal biasanya dilakukan melalui perlakuan panas. Tujuan dari perlakuan panas ini adalah untuk membentuk struktur mikro yang diinginkan dan/atau menghilangkan tegangan sisa. Dalam kasus ini, seringkali digunakan resep perlakuan panas tradisional yang telah dikembangkan untuk paduan logam tertentu. Namun, dalam beberapa situasi, metode perlakuan panas khusus telah dikembangkan untuk mempertahankan struktur mikro dengan butiran halus di dalam bagian AM sambil tetap mengurangi tegangan sisa dan meningkatkan keuletan.
Sebelum teknik DED dan PBF yang mampu memproses logam dan keramik secara langsung muncul, banyak teknik dikembangkan untuk membuat bagian "hijau" logam dan keramik menggunakan AM. Bagian tersebut kemudian mengalami pemrosesan termal untuk mencapai kepadatan yang diperlukan agar dapat digunakan. Binder jetting adalah satu-satunya proses AM yang umum digunakan untuk tujuan ini. Beberapa langkah persiapan biasanya dilakukan untuk mempersiapkan bagian "hijau" sebelum pemrosesan termal. Gambar di bawah ini menunjukkan langkah-langkah yang dilakukan untuk mempersiapkan bagian "hijau" logam yang terbuat dari LaserForm ST-100 untuk proses infiltrasi termal dalam tungku.
Gambar di bawah ini menampilkan contoh cetakan injeksi yang dibuat menggunakan proses pengaliran pengikat ExOne setelah melalui tahap pengikatan, sintering, dan infiltrasi (serupa dengan Gambar 8.5). Dalam pengembangan cetakan injeksi, penggunaan saluran pendingin yang mengikuti kontur permukaan, dikenal sebagai saluran pendingin konformal, terbukti secara signifikan meningkatkan produktivitas cetakan injeksi dengan mengurangi waktu pendinginan dan distorsi pada bagian-bagian cetakan. Dengan menggunakan saluran pendingin konformal yang tepat, banyak perusahaan dapat memanfaatkan perkakas cetakan injeksi yang diproduksi melalui proses manufaktur aditif untuk secara signifikan meningkatkan produktivitas mereka.
Kontrol kualitas pada manufaktur aditif ( /AM) merupakan proses penting untuk memastikan bahwa bagian-bagian yang diproduksi memiliki kualitas yang sesuai dengan spesifikasi yang diinginkan. Berikut adalah beberapa alat yang umumnya digunakan dalam kontrol kualitas pada AM:
Untuk menginspeksi kualitas, tersedia berbagai pilihan alat pengukuran mulai dari alat manual tradisional hingga peralatan digital industri. Alat-alat manual seperti jangka sorong dan set alat ukur adalah pilihan yang lebih terjangkau, sederhana, dan umum digunakan dibandingkan dengan opsi lainnya. Namun, alat-alat ini hanya dapat mengukur fitur geometri tertentu seperti panjang, diameter, dan sudut. Dengan kata lain, mereka tidak begitu serbaguna.
Namun, kelemahan utama dari alat-alat ini adalah bahwa semua data kualitas harus dicatat secara manual. Hal ini dapat menyebabkan tugas inspeksi metrologi menjadi melelahkan dan tidak efisien. Sebaliknya, salah satu alasan utama mengapa industri mengadopsi manufaktur tambahan adalah untuk memungkinkan fleksibilitas geometri yang lebih besar dan untuk meningkatkan alur kerja produksi melalui digitalisasi.
Permintaan untuk mencapai standar yang lebih tinggi telah mendorong industri untuk mengadopsi Mesin Pengukur Koordinat (CMM). Mesin ini dapat mereproduksi titik-titik awan digital dengan menggunakan probe kontak yang sangat presisi, sehingga memungkinkan pengukuran yang akurat pada geometri yang rumit seperti profil sayap. Selain itu, CMM memungkinkan interaksi langsung dengan lingkungan CAD, membuka peluang baru untuk analisis data.
Alat-alat digital dapat menyederhanakan proses verifikasi toleransi dengan membandingkan deviasi dari bagian yang diproduksi dengan desain CAD nominal mereka. Semua data inspeksi juga dapat disimpan dan diproses langsung dalam sistem terpusat. Secara keseluruhan, CMM merupakan mesin yang luar biasa; namun, mesin ini juga memiliki beberapa batasan. Proses inspeksi dengan CMM cenderung lambat dibandingkan dengan metode lainnya, memiliki portabilitas yang terbatas, dan karena menggunakan probe kontak, sangat tergantung pada fixture atau perangkat penahanan. Kini, kita mulai menghargai pemindai 3D berbasis cahaya sebagai alternatif yang berharga untuk CMM.
Tidak peduli teknologi pemindai 3D yang kita bicarakan, seperti fotogrametri, cahaya terstruktur, atau triangulasi laser, pemindai ini memiliki kemampuan untuk menangkap titik koordinat dengan kecepatan yang sangat tinggi tanpa perlu menyentuh objek yang dipindai. Oleh karena itu, menggunakan prinsip optik memberikan keuntungan besar dalam pemindaian ini. Namun, paradoksnya, teknologi ini juga memiliki beberapa kelemahan dalam situasi tertentu. Salah satu batasannya adalah gangguan dari pengaturan cahaya eksternal, sementara permukaan dengan sifat reflektif, transparan, atau gelap dapat mempengaruhi kualitas pengumpulan data.
Secara keseluruhan, dengan kemajuan yang terus dilakukan oleh produsen pemindai 3D dalam menyelesaikan masalah-masalah ini, pemindai 3D optik memiliki masa depan yang menjanjikan dalam industri manufaktur.
Selain digunakan dalam bidang medis, CT scan juga sangat diinginkan dalam lingkungan manufaktur yang memiliki persyaratan kualitas yang ketat selama bertahun-tahun. Mengapa demikian? Nah, dengan memanfaatkan pencitraan sinar-X, CT scan memiliki kemampuan untuk menghasilkan gambaran internal yang detail dan komprehensif dengan cepat dan tingkat akurasi yang luar biasa. Selain itu, semua data yang dihasilkan dapat diekspor sebagai peta kepadatan 3D yang memberikan informasi yang komprehensif tentang kualitas produk. Namun, ada lebih banyak lagi; CT scan tidak hanya berguna dalam metrologi, tetapi juga ideal untuk mendeteksi cacat seperti retakan, delaminasi, ruang hampa, kontaminasi, dan porositas lokal tanpa harus menyentuh bagian yang diperiksa.
Pemindai CT memiliki kemampuan yang lebih luas dibandingkan dengan metode pengujian non-destruktif lainnya seperti cairan penetrasi, arus eddy, partikel magnetik, dan ultrasonik. Namun, peralatan CT mungkin terlalu mahal untuk sebagian besar aplikasi, dan ada juga risiko terkait dengan paparan sinar-X. Karena kesulitan memiliki peralatan CT di dalam perusahaan, banyak perusahaan konsultan pihak ketiga, seperti Visiconsult, yang menyediakan layanan inspeksi menggunakan CT scan.
Dengan tujuan mempelajari lebih lanjut tentang proses Manufaktur Aditif (AM) guna mengembangkan standar dan menerapkan produksi dalam jumlah besar dengan keyakinan penuh, penting untuk mempercepat pengumpulan data. Sejauh ini, praktik-praktik yang telah diamati menunjukkan perlunya melakukan tugas inspeksi yang terpisah dari proses produksi, yang dapat menjadi pekerjaan yang melelahkan. Namun, dengan kemajuan terus-menerus dalam sensor, otomasi loop tertutup, kecerdasan buatan, pembelajaran mesin, dan komputasi awan, tidaklah mengherankan bahwa para inovator utama dalam AM telah menerapkan prinsip-prinsip ini dalam proses inspeksi in-situ. Dengan kata lain, mereka telah menyematkan pemindai dan teknologi inspeksi ke dalam mesin pencetak 3D.
Secara umum, cara kerjanya adalah sebagai berikut: sensor mengumpulkan data saat setiap lapisan produk terbentuk. Kemudian, dengan menggunakan kecerdasan buatan, semua informasi tersebut dapat diolah secara real-time untuk melakukan perbandingan, memberikan analisis, menghentikan proses jika terdeteksi kesalahan, dan yang paling penting, mengoptimalkan parameter pencetakan berdasarkan pembelajaran dari data historis. Banyak perusahaan yang terlibat dalam tren ini fokus pada mengimplementasikan solusi ini untuk proses PBF logam.