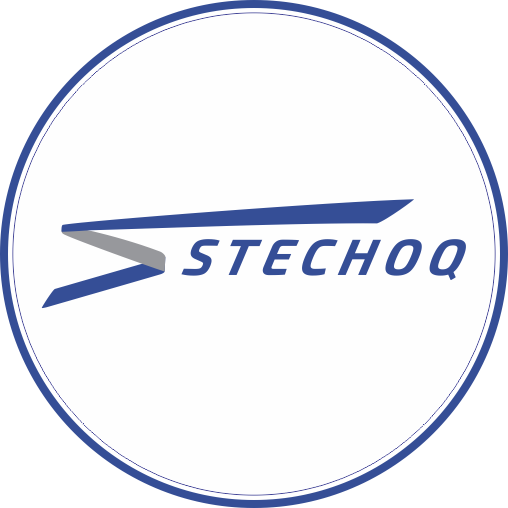
DAY 1
PENDAHULUAN
A. Definisi DFMA
Definisi DFMA (Design for Manufacture and Assembly) adalah pendekatan desain yang mengintegrasikan pertimbangan DFM (Design for Manufacture) dan DFA (Design for Assembly) untuk memudahkan proses pembuatan dan perakitan suatu produk.
DFM (Design for Manufacture) berfokus pada desain produk yang mempertimbangkan kemudahan dalam proses pembuatan komponen individual. Dalam DFM, desainer berusaha untuk mengoptimalkan bentuk, material, toleransi, dan fitur lainnya dalam desain produk untuk meminimalkan kesulitan dan biaya produksi. Tujuan utamanya adalah untuk memastikan bahwa komponen-komponen produk dapat diproduksi dengan efisien, mengurangi kesalahan produksi, dan mengoptimalkan penggunaan sumber daya.
DFA (Design for Assembly) berkaitan dengan desain produk yang mempertimbangkan kemudahan dalam proses perakitan. Dalam DFA, desainer berusaha untuk mengurangi kompleksitas perakitan, meminimalkan jumlah langkah perakitan, mengoptimalkan urutan perakitan, dan mempertimbangkan keterjangkauan komponen-komponen yang akan dirakit. Tujuan utamanya adalah untuk mempercepat waktu perakitan, mengurangi kesalahan perakitan, dan meningkatkan efisiensi produksi.
Dengan menggabungkan DFM dan DFA dalam DFMA, desainer dapat mengoptimalkan desain produk secara menyeluruh untuk memudahkan proses pembuatan dan perakitan. Dengan mempertimbangkan kedua aspek ini dalam tahap awal desain, perusahaan dapat mengurangi biaya produksi, meningkatkan kualitas produk, dan mengurangi waktu siklus produksi.
DFMA digunakan untuk tiga kegiatan utama:
a. DFMA sebagai dasar untuk studi teknik bersama (concurrent engineering)
DFMA memberikan panduan kepada tim desain dalam menyederhanakan struktur produk untuk mengurangi biaya pembuatan dan perakitan. Dengan mengintegrasikan pertimbangan DFM dan DFA sejak awal, tim desain dapat bekerja secara bersama-sama dengan tim manufaktur dan perakitan untuk menciptakan produk yang lebih mudah diproduksi dan dirakit. Hal ini memungkinkan adanya kolaborasi yang efektif antara berbagai departemen, mengurangi biaya, dan mempercepat waktu pengembangan produk.
b. DFMA sebagai alat benchmarking
DFMA dapat digunakan untuk mempelajari produk pesaing dan mengukur kesulitan dalam pembuatan dan perakitan. Dengan menganalisis produk pesaing, perusahaan dapat memperoleh wawasan tentang praktik terbaik dalam desain produk yang memudahkan pembuatan dan perakitan. Ini dapat membantu perusahaan untuk melakukan perbaikan dan inovasi dalam desain mereka sendiri.
c. DFMA sebagai alat penentuan perkiraan biaya (should-cost tool)
DFMA dapat digunakan sebagai alat untuk menghitung perkiraan biaya produksi dan perakitan. Dengan mempertimbangkan faktor-faktor seperti material, proses pembuatan, dan kompleksitas perakitan, perusahaan dapat menggunakan DFMA sebagai pedoman untuk menentukan perkiraan biaya yang lebih akurat. Ini membantu perusahaan dalam mengendalikan biaya produksi, melakukan negosiasi kontrak dengan pemasok, dan membuat keputusan yang informasinya berdasarkan analisis yang lebih mendalam.
Dengan menggunakan DFMA dalam kegiatan-kegiatan ini, perusahaan dapat mengoptimalkan desain produk, mengurangi biaya produksi dan perakitan, meningkatkan efisiensi, dan mengambil keputusan yang lebih baik dalam pengembangan dan produksi produk mereka.
B. Sejarah
Pada akhir 1970-an, konsep Desain untuk Manufakturabilitas dan Perakitan Otomatis (DFMA) mulai muncul sebagai pendekatan yang lebih terstruktur untuk mempertimbangkan efisiensi manufaktur dalam desain produk. William D. McMinimee dan Richard B. Stone dari Boothroyd Dewhurst, Inc. berperan penting dalam pengembangan DFMA. Mereka mengembangkan metode dan alat untuk membantu perancang menganalisis desain produk dari perspektif manufaktur dan perakitan.
Pada tahun 1983, Boothroyd Dewhurst, Inc. meluncurkan perangkat lunak DFMA pertama, yang memungkinkan perancang untuk menganalisis dan memperbaiki desain produk dengan mempertimbangkan biaya produksi dan perakitan. Sejak itu, DFMA telah menjadi pendekatan yang umum digunakan dalam industri manufaktur.
DFMA juga menjadi bagian penting dari pendekatan rekayasa bersama (concurrent engineering), di mana desain, manufaktur, dan perakitan dipertimbangkan secara bersamaan dalam pengembangan produk. Pendekatan ini memungkinkan kolaborasi antara departemen yang berbeda dan mempercepat waktu pengembangan produk, sambil mengoptimalkan biaya produksi dan perakitan.
Dengan perkembangan teknologi komputer dan perangkat lunak, implementasi DFMA menjadi lebih mudah dalam praktik desain. Perusahaan dapat menggunakan perangkat lunak DFMA untuk menganalisis desain produk, mengidentifikasi potensi perbaikan, dan memperkirakan biaya produksi. Hal ini memungkinkan perancang membuat keputusan yang lebih terinformasi dalam merancang produk yang efisien dan mudah diproduksi.
DFMA telah menjadi pendekatan penting dalam industri manufaktur, membantu perusahaan mengoptimalkan desain produk, mengurangi biaya, meningkatkan kualitas, dan mempercepat waktu pemasaran.
Sistem pengkodean yang digunakan untuk pemakanan dan penyetelan otomatis pada bagian-bagian kecil yang berputar. (Diturunkan dari Boothroyd, G. Assembly Automation and Product Design, Edisi ke-2, CRC Press, Boca Raton, FL, 2005.)
C. Implementasi Desain untuk Assembly
Implementasi desain untuk perakitan (DFA) memiliki tujuan untuk menyediakan alat-alat yang dapat digunakan oleh perancang produk. Alat-alat ini membantu perancang atau tim desain dalam mengidentifikasi masalah yang mungkin ada dalam desain yang diusulkan. Namun, hanya mengembangkan alat-alat desain saja tidak cukup; penting juga untuk mengajak para perancang untuk menggunakan alat-alat tersebut.
Pada tahun 1980, Peter Dewhurst bergabung dengan Boothroyd di UMass. Mereka segera bekerja sama dalam mengembangkan versi komputer dari buku panduan DFA. Mereka menggunakan komputer pribadi terbaru, seperti Apple II Plus, dan merilis paket perangkat lunak yang disebut "Design for Automatic and Manual Assembly". Ternyata, perancang di Amerika Serikat lebih memilih menggunakan komputer baru daripada melakukan perhitungan manual untuk menganalisis desain agar mudah dirakit, berbeda dengan rekan-rekan mereka di Eropa atau Jepang. Perusahaan-perusahaan seperti IBM dan Digital Equipment mendukung upaya penerjemahan perangkat lunak tersebut sehingga dapat berjalan pada komputer mereka sendiri, termasuk komputer pribadi terbaru dari IBM.
Ketersediaan perangkat lunak komputer untuk analisis DFA secara signifikan berkontribusi pada keberhasilan implementasi DFA di industri Amerika Serikat. Pada tahun 1981, Boothroyd Dewhurst Inc. didirikan sebagai perusahaan yang terus mengembangkan perangkat lunak untuk DFA serta estimasi biaya manufaktur untuk berbagai proses (DFM Concurrent Costing).
Terobosan besar dalam implementasi DFA terjadi pada tahun 1988 ketika Ford Motor Company melaporkan bahwa perangkat lunak DFA telah membantu mereka menghemat miliaran dolar dalam produksi mobil Taurus. Kemudian, General Motors (GM) melakukan perbandingan antara pabrik perakitan mereka di Fairfax, Kansas, yang memproduksi Pontiac Grand Prix, dengan pabrik perakitan Ford untuk model Taurus dan Mercury Sable di dekat Atlanta. GM menemukan adanya kesenjangan produktivitas yang signifikan dan menyimpulkan bahwa 41% kesenjangan tersebut dapat diatribusikan pada kemampuan manufaktur dari dua desain tersebut. Sebagai contoh, mobil Ford memiliki jumlah komponen yang lebih sedikit, seperti hanya 10 komponen pada bumper depan dibandingkan dengan 100 komponen pada Pontiac GM, dan komponen-komponen Ford dapat dipasang dengan lebih mudah.
Melalui implementasi DFA dan penggunaan perangkat lunak yang tepat, perusahaan seperti Ford dan General Motors dapat mengoptimalkan desain produk mereka, mengurangi biaya produksi, dan meningkatkan efisiensi perakitan.
D. Implementasi Desain for Manufaktur
Implementasi desain for manufaktur melibatkan penerapan konsep-konsep dan metode-metode yang mempertimbangkan aspek manufaktur dalam proses pengembangan produk. Berikut adalah beberapa langkah umum dalam implementasi desain for manufaktur:
a. Kolaborasi antar departemen
Penting untuk memastikan kolaborasi yang erat antara departemen desain, manufaktur, dan perakitan. Tim-tim dari berbagai departemen harus bekerja bersama untuk mempertimbangkan persyaratan manufaktur dan memastikan bahwa desain produk dapat diproduksi dengan efisien.
b. Pemahaman tentang proses manufaktur
Tim desain harus memiliki pemahaman yang mendalam tentang proses manufaktur yang akan digunakan untuk memproduksi produk. Mereka perlu mempelajari langkah-langkah yang diperlukan dalam proses manufaktur, memahami kendala teknis, dan mengidentifikasi potensi masalah yang dapat timbul selama produksi.
c. Analisis Desain untuk Manufakturabilitas (DFM)
Metode DFM digunakan untuk menganalisis desain produk dari perspektif manufaktur. Tim desain menggunakan alat-alat dan perangkat lunak yang tersedia untuk memeriksa desain produk dan mengidentifikasi area-area yang memungkinkan adanya kesulitan dalam proses manufaktur. Mereka melakukan perubahan desain yang diperlukan untuk meningkatkan manufakturabilitas.
d. Pemilihan bahan dan komponen yang sesuai
Tim desain harus mempertimbangkan pemilihan bahan dan komponen yang sesuai dengan proses manufaktur yang akan digunakan. Mereka harus memperhatikan ketersediaan bahan, kecocokan dengan proses produksi, dan faktor-faktor lain yang mempengaruhi manufakturabilitas produk.
e. Penggunaan teknologi dan perangkat lunak
Kemajuan teknologi dan perangkat lunak telah memungkinkan implementasi desain for manufaktur menjadi lebih efektif. Tim desain dapat menggunakan perangkat lunak simulasi dan analisis untuk memeriksa dan memvalidasi desain produk sebelum memasukkannya ke dalam proses manufaktur. Mereka juga dapat menggunakan teknologi otomasi untuk meningkatkan efisiensi dan kualitas produksi.
f. Evaluasi biaya manufaktur
Selama proses desain, tim harus melakukan evaluasi biaya manufaktur untuk memperkirakan biaya produksi dan mengidentifikasi area-area yang dapat dioptimalkan. Ini melibatkan mempertimbangkan biaya bahan, biaya tenaga kerja, biaya peralatan, dan faktor-faktor lain yang mempengaruhi biaya produksi.
g. Pengujian dan perbaikan berkelanjutan
Setelah implementasi desain for manufaktur, penting untuk terus menguji dan memonitor proses manufaktur. Tim harus mengumpulkan data dan umpan balik dari produksi untuk mengidentifikasi masalah dan melakukan perbaikan berkelanjutan dalam desain produk dan proses manufaktur.
Dengan mengikuti langkah-langkah ini, perusahaan dapat mengimplementasikan desain for manufaktur yang efektif, yang dapat membantu meningkatkan efisiensi, mengurangi
biaya produksi, meningkatkan kualitas produk, dan mempercepat waktu ke pasar.
E. Pertimbangan DFMA
DFMA (Design for Manufacture and Assembly) adalah pendekatan yang mempertimbangkan aspek manufaktur dan perakitan sejak awal dalam proses desain produk. Berikut adalah beberapa pertimbangan penting dalam implementasi DFMA:
a. Standardisasi Komponen
Meminimalkan jumlah komponen yang berbeda dalam desain produk dapat mengurangi kompleksitas manufaktur dan perakitan. Dengan menggunakan komponen standar yang tersedia secara luas, perusahaan dapat mengurangi biaya pembelian, persediaan, dan pelatihan tenaga kerja.
b. Reduksi jumlah komponen
Meminimalkan jumlah komponen dalam desain produk dapat mengurangi biaya produksi, waktu perakitan, dan risiko kesalahan. Dengan mengintegrasikan fungsi beberapa komponen menjadi satu komponen, perusahaan dapat meningkatkan efisiensi manufaktur dan perakitan.
c. Simplifikasi Proses Perakitan
Memperhatikan kemudahan perakitan adalah pertimbangan penting dalam DFMA. Desain produk harus mempertimbangkan aksesibilitas, kebutuhan alat khusus, dan urutan perakitan yang efisien. Dengan menyederhanakan proses perakitan, perusahaan dapat mengurangi waktu perakitan, biaya tenaga kerja, dan risiko cacat.
d. Optimisasi Desain Komponen
Desain komponen harus mempertimbangkan kemudahan manufaktur dan perakitan. Aspek-aspek seperti toleransi, penggunaan bahan yang sesuai, dan kekuatan struktural harus diperhitungkan agar komponen dapat diproduksi dengan efisien dan dirakit dengan mudah.
e. Integrasi Modul
Menggunakan modul yang terintegrasi dalam desain produk dapat mempermudah manufaktur dan perakitan. Dengan menggabungkan beberapa komponen menjadi satu modul, perusahaan dapat meningkatkan efisiensi, mengurangi risiko kesalahan, dan mempercepat waktu perakitan.
f. Penilaian Biaya Awal
Mengidentifikasi dan mengevaluasi biaya manufaktur dan perakitan sejak awal dalam proses desain adalah penting dalam DFMA. Dengan melakukan estimasi biaya awal, perusahaan dapat memprioritaskan perubahan desain yang mengarah pada efisiensi manufaktur dan penghematan biaya.
g. Memanfaatkan Alat DFMA
Menggunakan perangkat lunak dan alat analisis DFMA dapat membantu tim desain dalam menganalisis desain produk dari perspektif manufaktur dan perakitan. Alat DFMA dapat membantu mengidentifikasi masalah dan memperkirakan biaya produksi, sehingga memungkinkan perancang untuk membuat keputusan yang lebih informasional dalam merancang produk yang efisien dan mudah diproduksi.
Dengan mempertimbangkan aspek-aspek ini dalam implementasi DFMA, perusahaan dapat meningkatkan efisiensi manufaktur, mengurangi biaya produksi, meningkatkan kualitas produk, dan mempercepat waktu ke pasar.