Material Information Flow Chart (MIFC)
Prespective Sejarah
Pada semester pertama tahun 1980-an pada waktu itu divisi jishuken di supplier temanya adalah meningkatkan produktivitas dengan cara motion kaizen. Dilanjutkan pada semester kedua divisi jishuken mengambil tema untuk meningkatkan Just In Time, untuk itulah digunakan layout yang kemudian diberi nama aliran barang dan informasi. Sekitar tahun 90-an para Toyota Production System berkumpul untuk merumuskan cara penggambaran aliran material dan informasi.
Tujuan
Untuk mengetahui aliran dari Material/Part secara lengkap Untuk menguraikan / menggambarkan aktual kondisi yang terjadi di genba berikut sinkronisasinya secara Timing dan Volume Untuk mengetahui apakah airan material dari sistem yang berjalan sudah baik atau masih banyak masalah atau kekurangan (Complicated Flow) Untuk mengetahui point-point stagnasi yang ada dalam suatu sistem rangakain sistem produksi (akibat tidak seiramanya antara Timing dan Volume)
Tujuan pembuatan MIFC
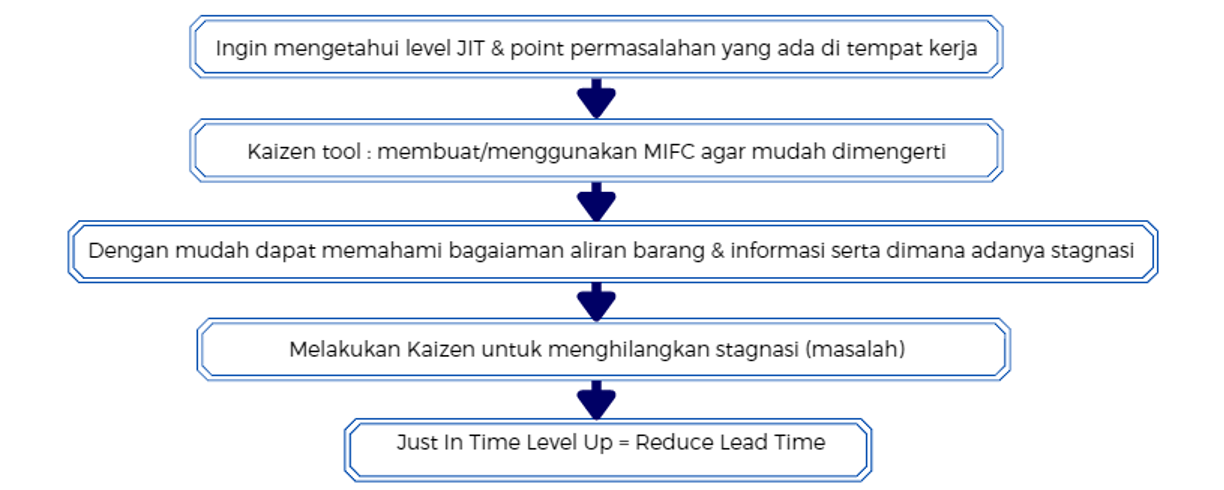
- Untuk mengetahui dimana adanya stagnasi dan berapa jumlahnya dari barang dan informasi.
- Sebagai alat untuk menunjukan dimana adanya dan jenis muda (stagnasi) apa yang ada.
Membuat Material Flow Chart
Material flow Chart sering disebut dengan Part Flow Chart (PFC) merupakan bagan/ilustrasi yang menggambarkan/ mendeskripsikan aliran material yang dimulai dari awal (Raw Material) hingga menjadi produk di proses terkahir. Melalui penggambaran MFC akan memudahkan kita dalammemahami suatu bentuk ilustrasi yang menggambarkan cara berfikir, pemahaman dan proses analisa terhadap kondisi aktual. Apa dan bagaimana pemhaman kita terhadap aliran barang/material secara "Genchi Genbutsu"
Tujuan Pembuatan Material Flow Chart
Untuk mengethaui aliran material secara lengkap Untuk mengetahui apakah aliran material dari sistem yang berjalan sudah baik atau masih banyak masalah/kekurangannya (Complicated Flow) Untuk mengetahui point-point stagnasi yang ada dalam satu aliran material sebagai alat bantu kaizen dalam mencapai aliran material yang mengalir/Seiryuka (searah) dan untuk mewujudkan Just in Time
Prinsip Dasar Material Flow Chart
Membuat part dengan konsep Just in Time, dengan mekanisme aliran yang mengalir searah/seiryuka dengan lokasi yang dekat Membuat part dengan konsep Just in Time, dengan mekanisme proses kerja yang meminimalkan atau menghilangkan stagnasi material/part antar proses (ada atau tidaknya dimana stagnasi/store itu diperlukan) Mengetahui kapasitas maksimum produksi dan kemampuan line yang dilewati oelh aliran part/material secara lengkap. Berikut merupakan data-data yang harus di ambil untuk pembuatan Material Flow Chart.
- Menggambarkan aliran proses secara umum (General Flow Process) dengan gambaran yang sederhana.
- Pengumpulan data-data pendukung seperti data teknis mesin atau proses kerja.
- Membuat daftar semua mesin dan proses yang digunakan.
- Membuat rincian sub-komponen dan menentukan mesin dari setiap proses untuk part yang terkait.
- Membuat Process Flow Table (PFT).
- Pengelompokan part yang mempunyai aliran proses yang sama.
- Visualisasi gambaran Value Stream Mapping berdasarkan Process Flow Table (PFT).
- Pengambilan data atau informasi penting setiap mesin atau proses seperti Takt Time, Line Takt Time, Cycle Time dan Machine Cycle Time, Loading Average dan Dandori data.
- Penentuan area yang akan menjadi prioritas untuk observasi, mecakup part, process, dan orang yang mempunyai hubungan dengan area kaizen.
- Identifikasi dan visualisasi masalah yang terkait dengan Material Issue dan Machine Issue.
- Melakukan pengaturan untuk fixed part-fixed machine berdasarkan data loading dan kapasitas dari setiap mesin dan proses.
- Melakukan pengecekan loading vs capacity untuk setiap mesin/proses berdasarkan aliran part yang baru dan buat Value Stream Mapping target berdasarkan kondisi aliran yang lancar.
Teknik Pengumpulan data untuk pembuatan material information flow chart bisa dilakukan dengan dua metode yaitu metode observasi dan metode wawancara, lebih lengkapnya dapat di simak pendapat sebagai berikut.
Observasi merupakan salah satu kegiatan ilmiah empiris yang mendasarkan fakta- fakta lapangan maupun teks, melalui pengalaman panca indra tanpa menggunakan manipulasi apapun. Tujuan dari observasi adalah deskripsi, pada penelitian kualitatif melahirkan teori dan hipotesis, atau pada penelitian kuantitatif digunakan untuk menguji teori dan hipotesis (Hasanah, 2017).
Menurut Fadhallah (2021) dalam bukunya mendefinisikan wawancara sebagai komunikasi antara dua pihak atau lebih yang bisa dilakukan dengan tatap muka dimana salah satu pihak berperan sebagai Interviewer dan pihak lain sebagai narasumber dengan tujuan memperoleh informasi atau mengumpulkan data.
Langkah Pembuatan MIFC
1. Menggambarkan aliran proses secara umum (General Flow Process) dengan gambaran yang sederhana.
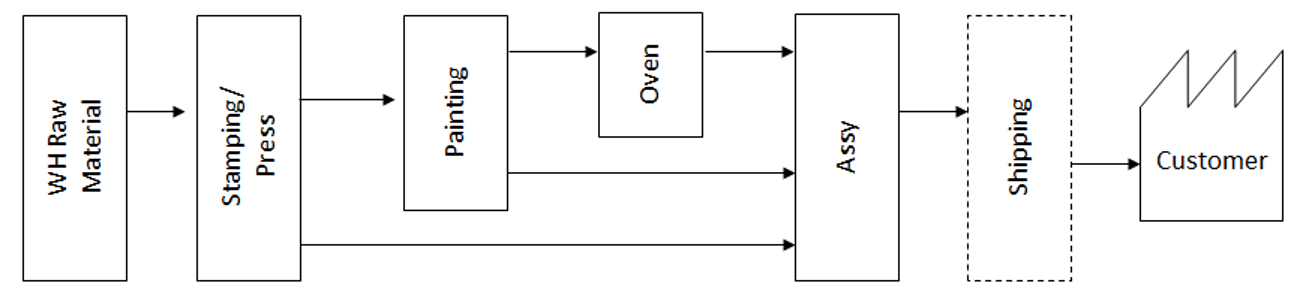
Catatan untuk menggambarkan aliran proses secara umum
- Banyaknya jumlah line/proses pada langkah ini belum perlu digambarkan secara detail penggambaran berdasarkan hasil genba.
- Mengecek gambar part dengan aktual proses bila diperlukan.
2. Kumpulkan data-data pendukung seperti data teknis mesin atau proses kerja.
- Master Part List dan Bill of Material (BOM)
- Nama Customer
- Nama proses dan urutan setiap proses
- Nama/Nomor Mesin dari setiap proses
- Data dan Spesifikasi mesin
- Volume/hari loading time
- Working hour/schedule time
- Takt Time, Line Takt Time, Cycle Time dan Machine Cycle Time
- Loading average
- Dandori data
Identifikasi data ditujukan untuk mengetahui aliran proses yang harus diperbaiki dan mengetahui waktu dari setiap proses sistem aliran yang sudah berlaku untuk dirampingkan dan disusun untuk pembuatan Material Flow Chart.
3. Membuat daftar semua mesin dan proses yang digunakan.
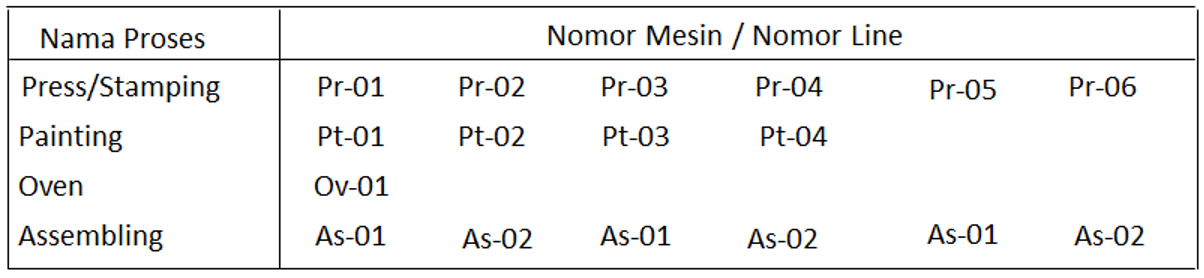
Tabel diatas merupakan contoh pembuatan daftar mesin yang dipakai pada saat produksi dan ada juga beberapa proses. Dapat dilihat pada tabel diatas bahwa nama proses Press, Painting, Oven dan Assembling dan untuk contoh nomer mesinnya adalah singkatan atau kode dari proses itu sendiri sebagai contoh Pr-01 menunjukkan Proses Press pada mesin nomor 01, begitu seterusnya.
4. Membuat rincian sub-komponen dan menentukan mesin dari setiap proses untuk part yang terkait.
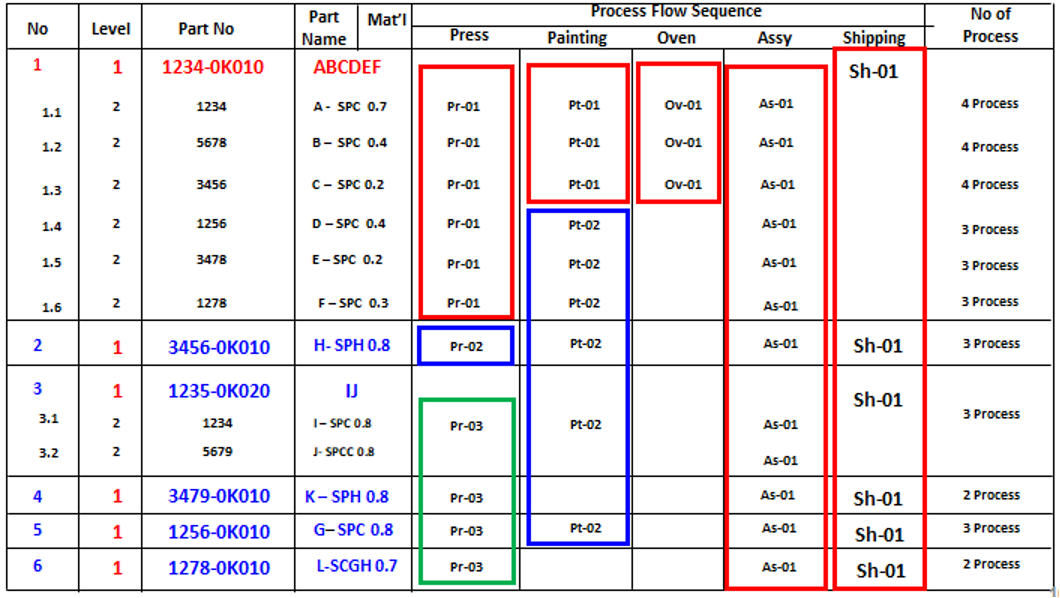
5. Membuat Process Flow Table (PFT)
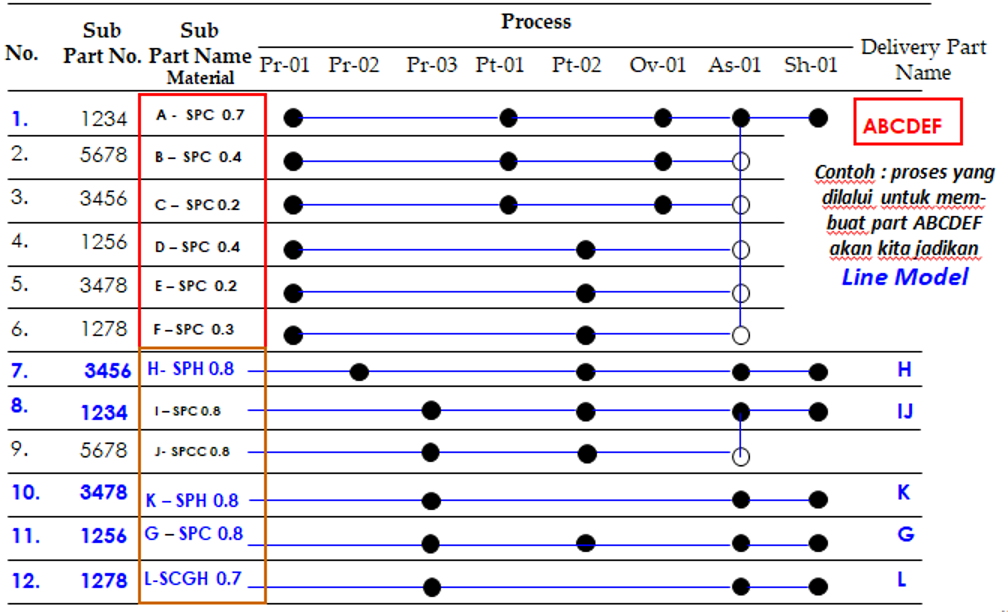
Key Point dalam penggambaran dan pembuatan PFT
- Berdasrkan Bill of Material (BOM), lakukan pengecekan untuk semua komponen part dan sub-komponen dari shipping ke progress sebelumnya sampai ke warehouse.
- Tentukan dan putuskan mesin yang dipakai untuk setiap part dan komponen partnya.
- Lihat jenis proses dan cara pembuatan terkait dengan Jig, Die atau peralatan yang mendukung proses dalam pembuatan part jadi.
- Lakukan pengecekan dan analisa terhadap loading, termasuk part lain yang diproses atau dibuat di mesin yang sama.
- Didalam PFT fokus dan konsentrasikan pada part model, berikut part yang terlibat dalam proses yang sama, dan check di genba, apakah proses-proses yang terkait sebelumnya.
6. Pengelompokan part yang mempunyai aliran proses yang sama
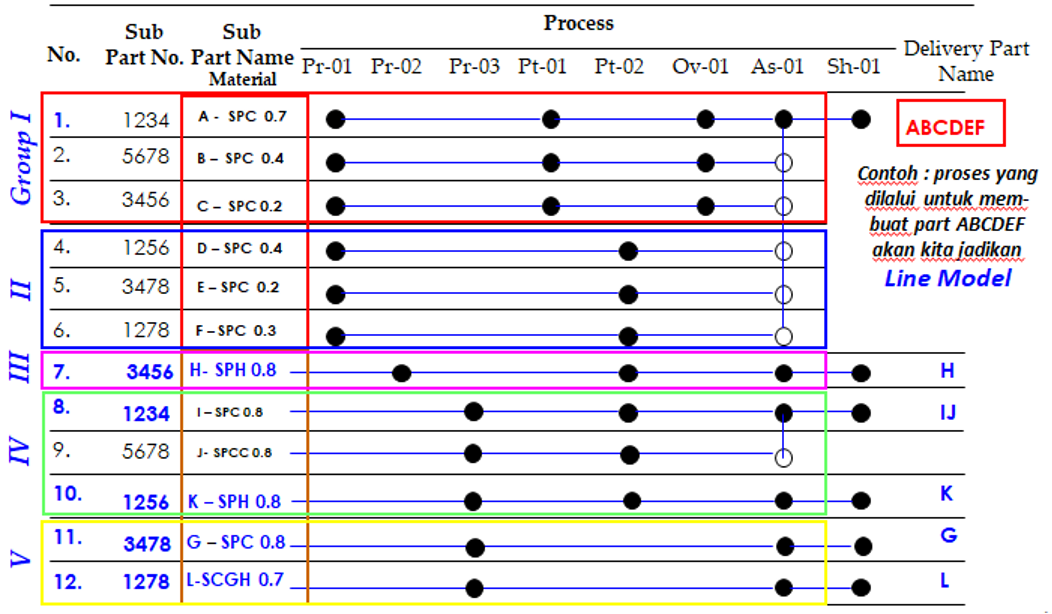
Pada tabel diatas adalah proses grouping atau pengelompokan part yang mempunyai alirna proses yang sama. Pada contoh diatas terdapat 5 group yang mempunyai aliran proses yang sama dan dikelompokkan sesuai aliran proses (Press, Painting, Oven, Assembling)
7. Menggambarkan MFC sesuai dengan PFT
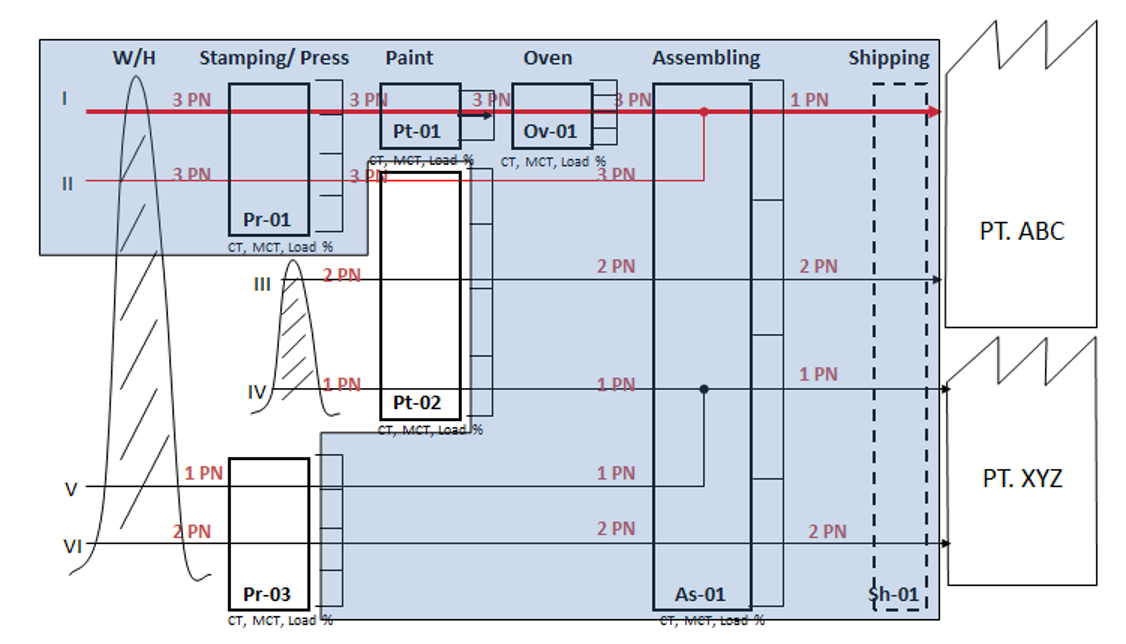
Key Point dalam penggambaran MFC
- Berdasrkan Process Flow Table buatlah Material Flow Chart untuk setiap grouping part-nya.
- letakkan part model pada posisi paling atas dan beri warna merah tebal dari area Shipping sampai Warehouse
Simbol-simbol dan point penting dalam pembuatan MFC
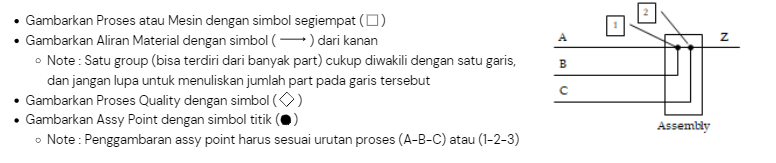
Simbol-simbol dan point penting dalam pembuatan MFC
- Gambarkan jig, tool, equipment yang mendukung terkait dalam proses (tidak menjadi part, tapi bagian dari proses) dengan simbol segiempat dalam proses.
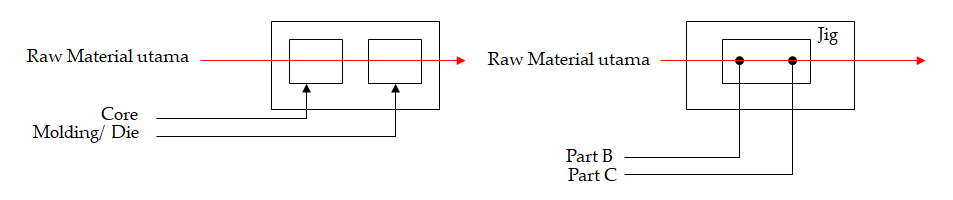
Note : Untuk proses Casting ( Molding, Core, Stamping, Assembling Manual, dsb.)
Simbol-simbol dan point penting dalam pembuatan MFC
- Gambarkan proses dengan garis putus-putus bila ada part yang mengalami proses bolak-balik.
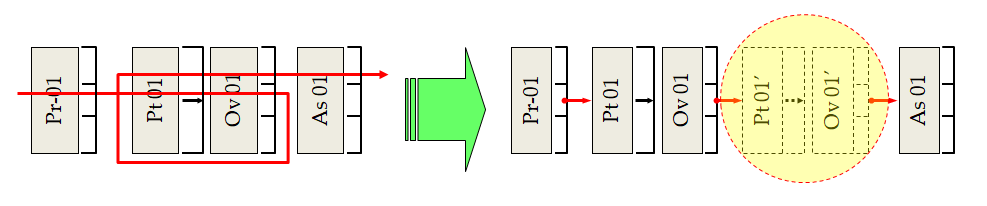
Note : Pastikan part yang mengalami proses bolak-balik dengan menggunakan mesin yang sama di dalam PFT agar tidak terjadi miss-calculation dalam perhitungan loadingnya.
Apabila terjadi perpecahan aliran dari satu proses menuju banyak proses lakukan penggambaran sebagai berikut :
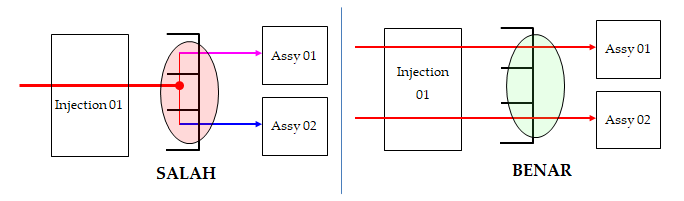
- Gambarkan simbol penyimpanan/menunggu proses berikutnya :
- Note : Pastikan semua part yang melewati antar proses mempunyai jenis penyimpangan/stagnasi yang benar
8. Menuliskan informasi penting tambahan untuk setiap Mesin atau Proses
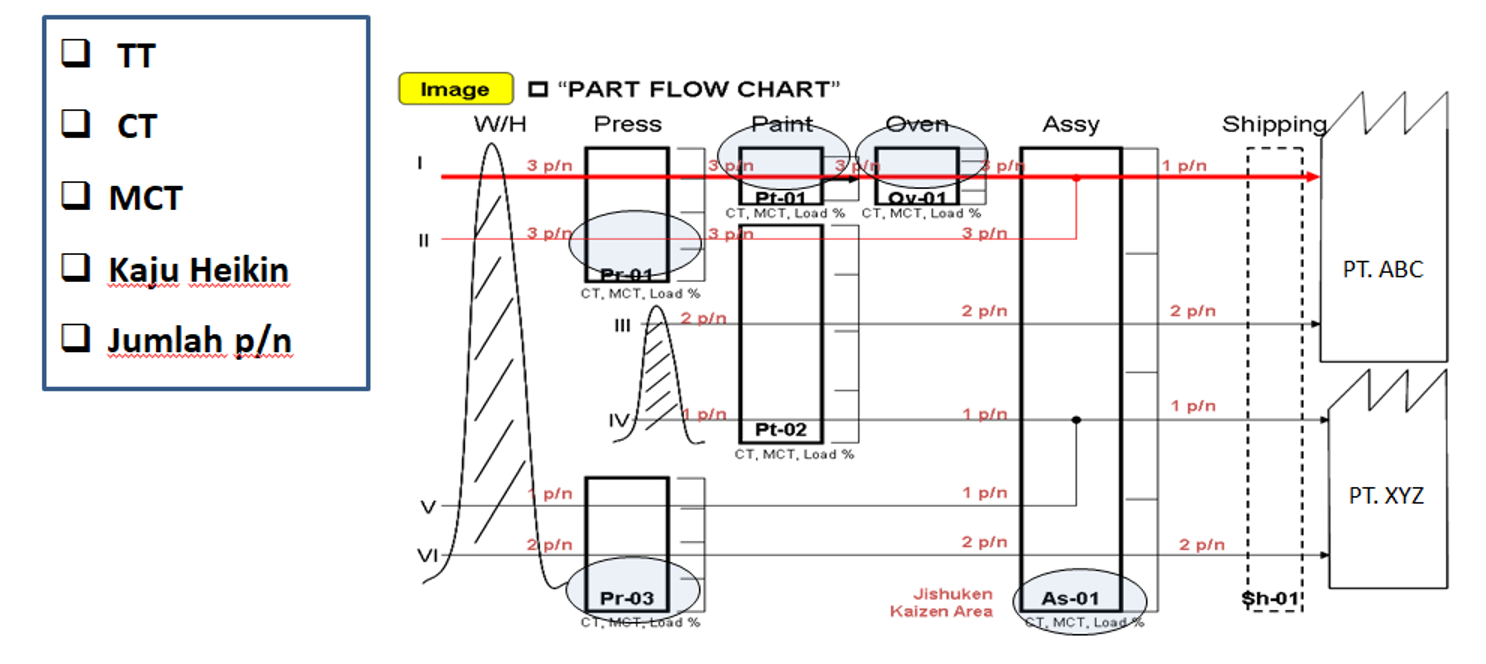
Data pendukung yang di butuhkan :
- Volume / day (Total Loading)
- Working time / day
- Loading time
- Loading Average
- Line Takt Time
- Cycle Time & M.C/T
- Dandori Time
9. Menentukan area yang akan diobservasi
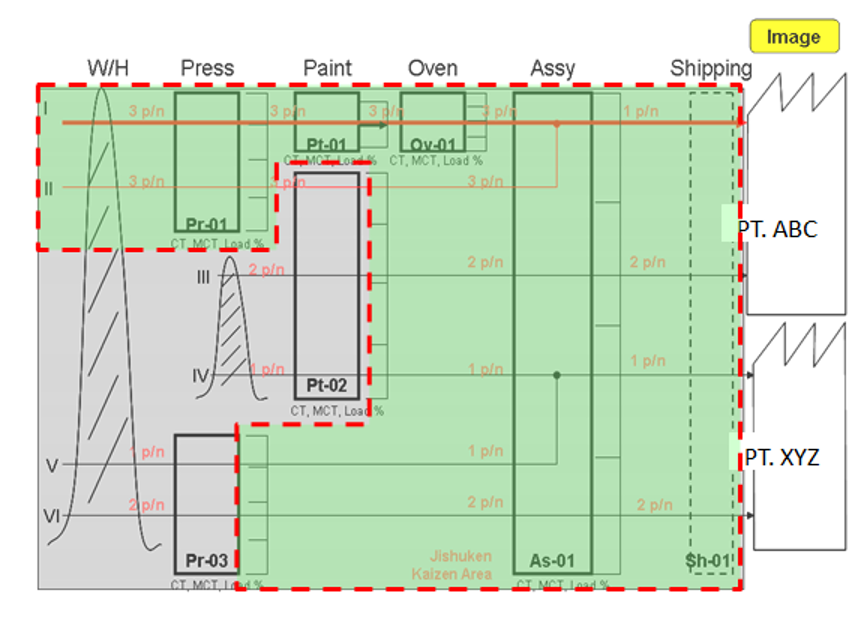
Key point penentuan area Jishuken (Area Observasi)
- Membuat garis merah tebal dan garis putus-putus sebagai batasan area dalam melakukan observasi dari area Shipping sampai area Warehouse
- Area yang sudah dibatasi adalah batasan dalam menghitung lead-time dan pembuatan MIFC
- Harus dipahami betul area sudah ditandai adalah tidakmenggangu area lain yang masih menjadi "grey area
- Jelaskan akar masalah secara jelas terhadap area observasi
10. Menampilkan masalah yang terkait dengan Material Issue dan Machine Issue Key Point dalam menampilkan masalah (Material Issue)
Key Point dalam menampilkan masalah (Material Issue)
- Aliran part yang tidak jelas/lancar, bebas, saling bertabrakan (complicated/cross flow)
- Tidak ada kontrol terhadap volume/stock/stagnasi
- Dalam MFC tidak perlu di perjelas dalam masalah -masalah yan terkait dengan "waktu/timming" seperti :
- Lot Produksi yang besar (Big Lot Size)
- Schedule vs Delivery Unfixed Timming (Push System)
- Quantity / kanban yang besar
- Sinkronisasi level antar proses / line
- Lakukan pengecekan berdasarkan MFC yang sudah dibuat sebelumnya
- Pastikan data-data / informasi yang terkait Loading Mesin, Part List, Jumlah Order, Jumlah Mesin dan Spesifikasi Mesin sudah lengkap
- Berdasarkan MFC, lakukan pengecekan terhadapa spesifikasi mesin dan karakter prosesnya, kemudian analisa kemungkinan dilakukannya pemindahan mesin atau proses
- Beri tanda (bulat dengan titik-titik) untuk mesin/proses yang memungkinkan untuk di-subtitusi atau diisi loadingnya
- Beri tanda (segita dengan titik-titik) untuk mesin/proses yang memungkinkan untuk di-subtitusi atau diisi loadingnya akan tetapi perlu improvement dan modifikasi dalam aplikasinya.
- Buat PFT dengan penambahan kemungkinan-kemungkinan tersebut diatas.
Note :
- Di dalam PFT, sebagai acuan dalam membentuk aliran yang seiryuka/searah, kita di perkenankan memberi simbol tambahan untuk mesin - mesin yang memungkinkan dengan proses yang sama (langsung/perlu memodifikasi dengan simbol yang perlu sudah ditetapkan)
- Ini juga digunakan sebagai informasi/data pendukung dalam melakukan antisipasi apabila terjadi kondisi abnormal (mesin bermasalah/rusak)
11. Pengaturan Fixed Parts-Fixed Machine
Key Point dalam Fixed Parts-Fixed Machine
- Lakukan perpindahan part dengan melihat loading dan kapasitasnya berikut kemungkinannya dengan metode YOSEDOME (lebih baik menggunakan satu mesin dengan loading sesuai dengan kapasitasnya, daripada menggunakan banyak mesin dengan loading yang masih dibawah kapasitasnya) dengan membuat Proses Flow Tabel baru.
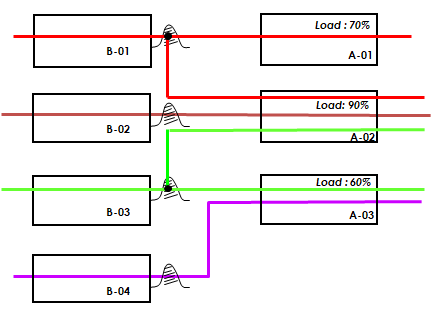
- Seiryuka mempunyai dua arti :
- Aliran yang lancar/smooth flow menuju ideal
- Fixed Parts, Fixed Machine
- Apabila tidak Seiryuka maka akan sulit untuk mengkontrol, dan sulit untuk mengapilkasikan Just-In-Time.
12. Pengecekan Loading vs Capacity untuk setiap Proses/Mesin berdasarkan aliran material yang baru dan buat MFC target berdasarkan kondisi aliran yang lancar
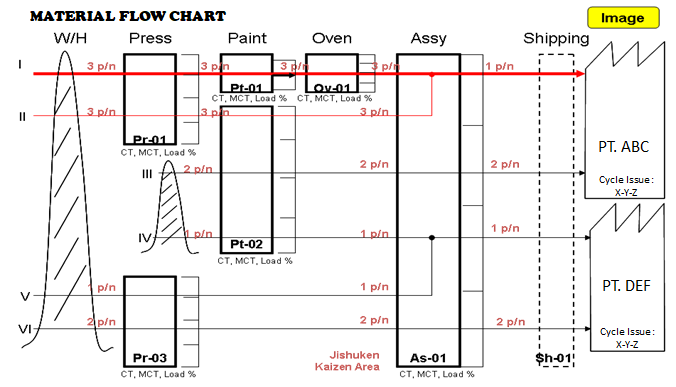