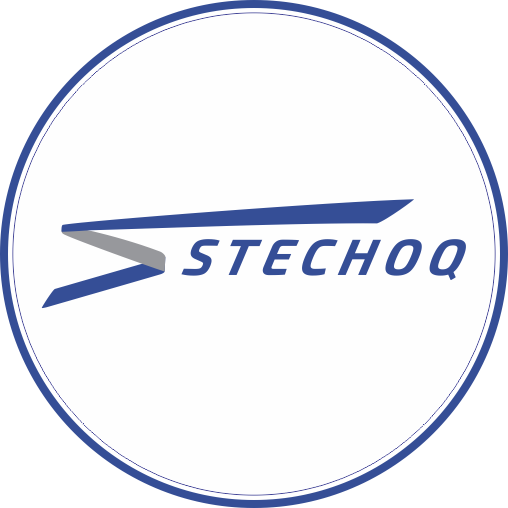
FLOW PRODUCTION
1. Flow Production
Produksi merupakan salah satu bagian terpenting dari perusahaan yang berkaitan dengan transformasi input menjadi output sesuai dengan standar kualitas yang telah ditentukan.
Sistem Produksi terlaksana dengan mempergunakan sumber daya untuk mengolah input menjadi output dengan fungsional sumber daya yang spesifik terspesialisasi sesuai dengan pembagian kerja atau prosesnya. Berdasarkan keragaman fungsional dari sumber daya dan aliran proses dari produk yang dihasilkan akan mempengaruhi pengaturan sumber daya dalam sistem produksi tersebut.
Aliran produksi merupakan cara yang digunakan dalam memproduksi bahan baku sehingga menjadi produk jadi yang melibatkan pengetahuan, tenaga kerja, mesin dan faktor faktor produksi lainnya.
Jenis flow production:
2. Just In Time
Just In Time atau sering disingkat dengan JIT adalah suatu sistem produksi yang digunakan untuk memenuhi kebutuhan pelanggan tepat pada waktunya sesuai dengan jumlah yang dikehendakinya.Tujuan sistem produksi Just In Time (JIT) adalah untuk menghindari terjadinya kelebihan kuantitas/jumlah dalam produksi (overproduction), persediaan yang berlebihan (excess Inventory) dan juga pemborosan dalam waktu penungguan (waiting). Dengan adanya sistem JIT, kita telah dapat mengatasi 3 pemborosan (overproduction, excess inventory dan waiting) diantara 7 pemborosan (7 Waste) yang harus dihindari dalam sistem produksi Toyota.
3. Tata Letak Peralatan Sesuai Urutan Proses
A. Pada penerapan sistem ONE PIECE FLOW, setelah proses 1 selesai benda kerja segera dipindahkan ke proses selanjutnya. Itu berarti setiap benda kerja harus dipindahkan melalui alat angkut yang ada sistem. Yang membuat terjadinya pemborosan waktu ataupun alat angkut.
B. Ide tata letak peralatan yaitu untuk meminimalkan pengangkutan atau menghilangkan. Sebagai contoh melakukan pengaturan peralatan sesuai dengan urutan pemrosesan. Jenis line up ini adalah standar untuk semua tokoh aliran dan jalur produksi berorientasi aliran.
4. Sinkronisasi
● Setelah kita menyiapkan peralatan untuk Flow Production, kita perlu mempertimbangkan seberapa cepat aliran yang seharusnya Kecuali jika kita memiliki ritme yang sama di antara proses, benda kerja akan terakumulasi pada proses yang lebih lambat dan menyebabkan aliran "membanjiri proses tersebut.
● Sinkronisasi berarti mempertahankan ritme yang sama di antara berbagai proses. Dalam analisis akhir, ritme harus ditentukan (dalam hitungan menit dan detik) dengan jumlah pesanan dari pelanggan. Angka waktu ini disebut waktu siklus. Waktu siklus mengatur ritme untuk "musik" manufaktur.
5. Operasi Multi-Proses
Produksi ONE-PIECE FLOW dapat dicapai tanpa operasi multi-proses. Sebagai gantinya, kita dapat dengan mudah: tetapkan satu pekerja untuk setiap proses dan minta mereka memproses dan serahkan benda kerja sesuai dengan yang ditetapkan atau dengan kata lain adalah hand-transferred one-piece flow., dimana ilustrasinya ada pada gambar diatas.
6. Pelatihan bagi pekerja multi-proses
Pekerja multi-proses adalah pekerja yang dilatih untuk menangani beberapa proses bersama. Melatih pekerja multi-proses adalah langkah kunci menuju pencapaian produksi aliran JIT. Pelatihan ini dapat diperluas ke seluruh perusahaan dalam jangka pendek untuk mencakup:
● Standarisasi mesin dan peralatan lainnya secara menyeluruh sehingga siapa pun dapat lebih mudah belajar mengoperasikannya;
● Standarisasi operasi yang sama menyeluruhnya, menghilangkan kasus-kasus khusus atau luar biasa;
● Pelatihan multi-keterampilan di seluruh perusahaan sebagai bagian penting dari perbaikan di seluruh perusahaan.
7. Berdiri saat bekerja
Pekerja di sebagian pabrik mesin secara tradisional berdiri saat bekerja. Di sisi lain, Jalur perakitan biasanya dioperasikan oleh pekerja yang duduk sambil bekerja, seperti pada pabrik elektronik rumah dan peralatan listrik. Transisi dari duduk ke berdiri saat bekerja dapat menyebabkan masalah serius di lingkungan tersebut. Perlu waktu yang cukup lama bagi pekerja di bidang perakitan untuk diyakinkan akan pentingnya berdiri saat bekerja.
Satu-satunya cara agar berhasil dalam transisi yang sulit ini dan mengatasi keengganan pekerja untuk berdiri adalah dengan melibatkan seluruh perusahaan, termasuk pemimpin dan manajer atas lainnya dalam menekankan manfaat berdiri sambil bekerja, seperti :
● Pergerakan menjadi lebih mudah
● Dapat mudah membantu satu sama lain ketika diperlukan
● Membantu dalam koreksi operasi yang tidak seimbang
● Operasi multi-proses
8. Buat Peralatan Menjadi Ringkas
Jika satu benda kerja seukuran kepalan tangan, maka besar dari 100 benda kerja akan seukuran mesin cuci.Untuk menangani sebuah lot seukuran 100 benda kerja, maka dibutuhkan conveyor yang dapat dengan mudah memindahkan sebuah mesin cuci. Demikian pula dengan mesin pengolah dan peralatan lainnya, harus mampu menangani lot seukuran mesin cuci. Dengan kata lain, mesin akan berukuran besar, bahkan banyak yang tidak muat pada lini produksi kecil. Dalam kebanyakan kasus, kita harus menyisihkan peralatan besar seperti "pulau" pemrosesan.
Terkadang, mesin serba guna dengan harga tinggi yang diiklankan mampu melakukan hampir semua hal sering kali tidak berjalan dengan baik. Mesin-mesin ini bahkan tidak berguna dalam produksi JIT. Sebaliknya, kita harus berusaha untuk hanya menggunakan mesin yang ringkas serta dapat diatur ulang ke dalam lini produksi saat itu juga dengan harga yang murah sehingga kita tidak khawatir tentang tingkat pemanfaatan kapasitasnya.
9. U-Shaped Manufacturing cells
Dalam beberapa kasus, tidak apa-apa untuk menggunakan straight line untuk flow production. Namun, jika kita memiliki produksi one-piece flow yang menggunakan operasi multi-proses maka akan terjadi pemborosan waktu pekerja dimana ia harus berjalan kembali dari proses akhir ke proses awal untuk mendapatkan benda kerja berikutnya. Di sinilah sel manufaktur berbentuk U berfungsi.
LEVELING
Leveling/ Heijunka merupakan metode yang digunakan untuk mengupayakan agar seluruh proses pekerjaan berlangsung pada level tertentu yang sama rata pada setiap kondisi. Agar mencapai tingkat produktivitas yang tinggi dengan biaya yang rendah, tepat waktu, dan tepat jumlah.
Production Leveling berusaha mengatasi:
2. Metode Penjadwalan Produksi.
Sering terjadi ketika produk tertentu memiliki permintaan yang rendah.
Metode ini membutuhkan data berapa banyak produk yang harus dibuat dalam sebulan, kemudian dilakukan penghitungan output harian standar yang akan bertambah per harinya hingga total produksi per bulan yang diinginkan terpenuhi.
Jumlah output produksi per bulan dibagi menjadi empat total produksi mingguan yang sama dengan jadwal produksi terpisah dan dibuat untuk setiap minggu hingga total produksi per bulan yang diinginkan dapat terpenuhi
Jumlah produksi per hari didapatkan dari hasil pembagian antara jumlah produksi per bulan dengan jumlah hari kerja yang dibutuhkan selama sebulan. Sehingga, produksi dari berbagai macam model varian dilakukan sekali sehari.
3. Teknik Leveling
Waktu rata-rata yang dibutuhkan untuk menyelesaikan 1 unit produk dari lini perakitan dengan asumsi setiap proses perakitan mempunyai kecepatan yang konstan.
Dalam JIT, kita mendapatkan waktu siklus dengan membagi total output produksi yang dibutuhkan untuk memenuhi kebutuhan pasar saat ini dengan: jumlah waktu kerja (dinyatakan dalam menit) dalam sehari.
Daftar siklus adalah ilustrasi seperti roda yang menunjukkan pola produksi konstan yang berulang sepanjang hari untuk menghasilkan variasi dan volume produk yang dibutuhkan. Jika bagian proporsional dari model produk adalah 50 persen untuk produk X, 30 persen untuk produk Y, dan 20 persen untuk produk Z, kita dapat mengekspresikan pola itu dalam daftar siklus seperti gambar disamping. Yang terbaik adalah mengikuti daftar siklus sedekat mungkin.
Namun, berbagai masalah terkadang muncul ketika menentukan variasi dalam waktu siklus. Ketika variasi seperti itu biasa terjadi, bisa mengadopsi versi "Nonreserved Seat" dari Cycle List. Maksud dari nonreserved seat cycle list adalah untuk memiliki bagian Nonreserved Seat dari daftar kompensasi variasi yang disebabkan oleh akumulasi kecil dari inventaris dalam proses, yang terbukti dari penyesuain kanba yang terpisah.
Umumnya, jika pabrik sedang memproduksi tiga model produk (X, Y, dan Z), ini proses akan menangani benda kerja untuk setiap model dalam batch tingkat terpisah.
Gambar dibawah menunjukkan bagaimana permasalahan ketidakefisienan diatas diselesaikan dengan meratakan produksi pada proses pengecatan melalui metode Reserved Seat.
Konfigurasi Reserved Seat dari benda kerja di gantungan menghilangkan kebutuhan inventaris. Bahkan pekerjaan memasang benda kerja di gantungan dan menghapusnya telah diratakan untuk meningkatkan kelancaran operasional dan stabilitas
Metode ini namanya diambil dari cara pelari estafet mengoper tongkat dalam suatu zona untuk menghindari kesulitan passing "pekerjaan" membawa tongkat pada setiap penyelesaian titik tertentu. Di pabrik, zona sentuh tongkat adalah kisaran tertentu operasi di mana operator dapat meneruskan atau pekerjaannya ke operator berikutnya. Fleksibilitas yang diberikan oleh zona sentuh tongkat seperti itu membantu menjaga keseimbangan lini ketika model produk diubah.
Ketika jumlah pekerjaan manual sangat berbeda dari model produk ke model produk, dimana Baton Touch Zone tidak akan berfungsi. Kita dapat menggunakan metode Bypass untuk buat jalur "bypass" terpisah yang dapat mengakomodasi perubahan model.
Namun, kita tidak bisa membuat garis bypass dari sembarang garis. Pertama-tama kita harus membangun produksi aliran model campuran dan menyeimbangkan lini berdasarkan jenis produksi tersebut. Metode bypass hanya boleh digunakan sebagai pilihan terakhir ketika metode zona sentuh tongkat tidak layak.
REALIZING PRODUCTION LEVELING
1. Developing Flow Production
Jika produksi diratakan hanya untuk satu kelompok proses produksi pabrik, seperti hanya jalur perakitan, mungkin tidak akan berhasil meningkatkan efisiensi pabrik secara keseluruhan. Untuk melakukan itu, seluruh sistem produksi harus dikembangkan sebagai sistem flow production
Gambar disamping menunjukkan proses persiapan pintu dari produsen lemari wastafel sebelum perbaikan. Untuk melakukan perbaikan ini, para manajer pabrik memindahkan proses persiapan pintu dari lantai dua ke lantai satu. Mereka menyinkronkan produksi di sel ini agar sesuai dengan leveled mixed-model flow line. Akibatnya, mereka mengurangi persediaan menjadi hampir nol, mencapai pengurangan besar dalam tenaga kerja.
2. Improved (Kaizen) Retooling
Pabrik umumnya mencakup jalur pemrosesan dan jalur perakitan. Poin kunci untuk perataan produksi dari jalur pemrosesan adalah untuk meningkatkan retooling. Mampu beralih di antara model produk dan untuk meningkatkan keseimbangan operasi jalur perakitan adalah perhatian utama dari perataan produksi di jalur perakitan.
Gambar Dibawah ini menunjukkan bagaimana suatu pabrik meningkatkan operasi pengambilan pengirimannya sehingga barang yang diselesaikan oleh jalur perakitan diambil delapan kali sehari (sekali setiap jam), bukan hanya sekali sehari.
Untuk memungkinkan pengambilan setiap jam, jalur perakitan terutama harus meningkatkan prosedur pergantian model produknya untuk mempersingkat waktu pergantian. Begitu mereka melakukan ini, persediaan pasca-perakitan turun menjadi seperdelapan dari tingkat sebelumnya dan akumulasi persediaan dalam proses setelah langkah-langkah persiapan dan pemrosesan dihilangkan, sehingga menghasilkan produksi aliran yang lancar.