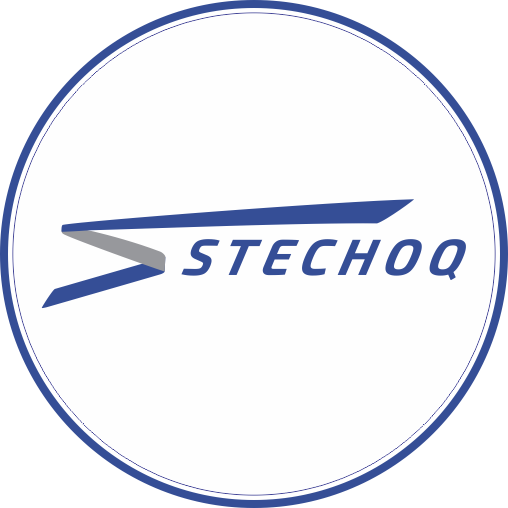
Quality Assurance
Lingkup pengendalian kualitas terdiri dari beberapa bagian seperti,
a. Total Quality Management : Bertujuan untuk perbaikan terus-menerus, Melibatkan pemasok dan pelanggan, melibatkan semua operasi, pengukuran kinerja, kerja sama tim, keterlibatan karyawan.
b. Quality Assurance: Persetujuan pihak ketiga, audit sistem, perencanaan kualitas lanjutan, manual kualitas komprehensif, penggunaan biaya kualitas, keterlibatan operasi non produksi, mode kegagalan dan analisis efek, pengendalian proses statistik.
c. Quality Control: mengembangkan manual kualitas, data kinerja proses, inspeksi diri, pengujian produksi, perencanaan kualitas dasar, penggunaan statistik dasar, kontrol dokumen.
d. Inspection: Menyelamatkan, menyortir, menilai, tindakan korektif, mengidentifikasi sumber ketidaksesuaian.
Perkembangan Mutu
Inspeksi (Inspection)
Pada Tahun 1920-an, Para inspector Mengukur Hasil Produksi Berdasarkan Spesifikasi. Namun, inspector Pada Zaman Tersebut Tidaklah Independen. Hal Ini Menyebabkan Adanya Kecurangan Akibat Adanya Beberapa Kepentingan. Seandainya inspector Melakukan Penolakan Terhadap Suatu Proses Produksi Akibat output Yang Dihasilkan Tidak Sesuai Dengan Spesifikasi, Maka Bagian Pabrik Akan Tetap Meloloskannya Tanpa Memperhatikan Mutu Dari output Yang Dihasilkan.
Pengendalian Mutu (Quality Control)
Adanya Perang Dunia II Pada Tahun 1924-an, Mengharuskan Dihasilkannya Produk Militer Yang Bebas Cacat. Cara Yang Digunakan Yaitu Adanya Pengendalian Mutu Selama Memproduksi Produk Militer Tersebut. Hal Ini Menyebabkan Para inspector Beralih Menjadi Para Pengendali Mutu. Untuk Mendapatkan Hasil Penilaian Mutu Produk Militer Yang Baik, Maka Para Pengendali Mutu Ini Merupakan Pihak Yang Independen.
Penjaminan Mutu (Quality Assurance)
Sehubungan Dengan Adanya Rekomendasi Yang Diajukan Oleh Para Teknik-teknik Statistik Terkait Dengan Pengendalian Mutu Produk, Perlu Adanya Pihak Yang Melakukan Pengambilan Keputusan. Hal Ini Kemudian Menyebabkan Adanya Perkembangan Pengendalian Mutu Menjadi Penjaminan Mutu (Quality Assurance). QA Bertanggung Jawab Memastikan Proses Yang Berjalan Dengan Produk Yang Dihasilkan Sesuai Dengan Spesifikasi Yang Telah Ditetapkan Melalui Pelaksanaan Audit, Pelatihan Dan Analisis Kinerja.
Manajemen Mutu Terpadu (Total Quality Management)
Mutu Fungsi Produksi Bukanlah Satu-satunya Hal Yang Mempengaruhi Kepuasan Pelanggan. Seiring Dengan Perkembangannya, Manajemen Mutu Tidak Hanya Menjadi Tanggung Jawab Bagian Tertentu, Tetapi Menjadi Tanggung Jawab Setiap Individu Dalam Perusahaan. Inilah Yang Disebut Dengan Total Quality Management.
Quality Assurance vs Quality Control
Quality Assurance (Penjaminan Mutu) Adalah Rangkaian tindakan terencana, sistematis yang ditujukan untuk meyakinkan pelanggan bahwa persyaratan yang telah ditetapkan akan dijamin tercapainya. QA lebih berperan sebagai analyst untuk memperbaiki suatu produk/service yang datanya diperoleh dari sampling bagian QC, feedback dari internal perusahaan maupun adanya komplain yang diterima dari customer.
Selain itu, QA juga umumnya berperan sebagai sertifikasi atas terjaminnya mutu suatu produk/service. QA memiliki kedudukan lebih tinggi dari QC, dimana QA bertugas menentukan layak tidaknya suatu produk/service. QA lebih kepada menjaga image perusahaan dengan mencegah defect kepada konsumen.
Siklus Quality Assurance
Proses dari quality assurance biasanya mengikuti sebuah cycle atau siklus yang disebut PDCA. Siklus tersebut akan diulang untuk memastikan bahwa proses yang dilakukan dalam perusahaan dievaluasi dan ditingkatkan secara berkala. Mari membahas lebih detail tentang siklus PDCA.
Sebuah perusahaan harus merencanakan menetapkan tujuan terkait proses yang diperlukan untuk menghasilkan dan memberikan produk atau layanan berkualitas tinggi
tim yang memegang tugas ini mengembangkan proses, menguji, dan memastikan berhasil atau tidaknya produk/layanan perusahaan
Tim check bertugas untuk memantau, memodifikasi, dan memeriksa apakah proses tersebut memenuhi tujuan awal perusahaan
Tim ini harus mengubah proses atau melakukan tindakan yang dirasa perlu untuk menghasilkan produk/layanan sesuai standar yang telah ditentukan. Tujuan dari salah satu metode evaluasi ini yaitu menghasilkan produk atau layanan berkualitas tinggi yang berfungsi dengan baik dan dapat bertahan lama.
Quality assurance adalah bagian penting dari proses pengembangan suatu perusahaan. Dengan memastikan bahwa lini produksi bekerja sesuai standar yang ditetapkan, hal ini membuat proses pengembangan produk berkualitas tinggi menjadi lebih mudah, cepat, dan berhasil. Hal ini akan berimbas pada kemudahan karyawan dalam melakukan pekerjaan dengan lebih optimal.
Bagaimana Mengurangi Variasi ?
Pertanyaan ini sering muncul pada saat akan meningkatkan kualitas dari suatu produk, berikut hal-hal yang dapat dilakukan untuk mengurangi variasi pada produk.
Tahapan dalam Quality Assurance
Siapa yang Bertanggung-Jawab ?
1. Pihak yang paling bertanggung jawab adalah manusia (operator, manajemen, siapa saja yang mengelola dan menjalankan operasi)
2. Kesalahan manusia (human error)
3. Pendekatan untuk memahami kesalahan manusia:
- Kesalahan dipandang sebagai kewajaran dan keterbatasan manusia. Idenya adalah bahwa "berbuat salah adalah manusiawi" dan wajar saja jika orang akan membuat kesalahan sesekali.
To err is human
- Membuat kesalahan adalah dosa. Dalam mengambil pendekatan ini, kita harus ingat untuk mengarahkan kritik kita pada kesalahan itu sendiri dan bukan pada orang yang membuatnya.
We can avoid it at least reduced it
Lima Elemen Pembentuk Kesalahan
Menurut Suyadi Prawirosentono (2001:12) mengemukakan faktor-faktor yang dapat mempengaruhi pengendalian kualitas, yaitu :
1. Manusia (Man) Dalam melaksanakan proses produksi, keberadaan operator juga sangatlah penting, Adapun penyebab tipisnya bending kabel dari segi manusia yaitu kesalahan dalam melakukan setting, tidak memahami pengoperasian mesin secara mendalam, dan tidak memahami SNPP (Standar Nilai Produk dan Proses). Perbaikan yang dapat dilakukan adalah dengan memberikan training dan pengawasan untuk operator, pengujian lapangan, dan pemberian pengetahuan mengenai pengoperasian mesin secara mendalam agar kesalahan dapat diminimalisir.
2. Metode (Method)
Berkaitan dengan metode kerja yang benar, mengikuti prosedur-prosedur kerja yang ditetapkan
3. Mesin (Machine) Berkaitan dengan sistem perawatan preventif terhadap mesin-mesin produksi, termasuk fasilitas dan peralatan lain
4. Bahan baku (Materials) Berkaitan dengan kualifikasi dan keseragaman bahan baku dan bahan penolong yang digunakan dalam proses produksi, serta penanganan terhadap bahan baku dan bahan penolong itu.
5. Ukuran (Measurement) Pada saat proses produksi, metode dalam pengoperasian mesin juga perlu diperhatikan. Penyebab tipisnya bending kabel dari segi metode adalah kesalahan setting mesin sehingga kabel yang dihasilkan tidak sesuai dengan spesifikasi. Perbaikan yang dapat dilakukan adalah dilakukannya briefing dan pengawasan operator agar kesalahan setting mesin dapat diminimalisir.
6. Lingkungan Lingkungan juga merupakan salah satu komponen penting dalam proses produksi karena akan menentukan kualitas dari produk yang dihasilkan. Penyebab tipisnya bending kabel dari segi lingkungan adalah lingkungan kerja dan tempat penyimpanan material yang lembab. Oleh karena itu, perbaikannya adalah mengatur kelembaban tempat penyimpanan material dan lingkungan kerja.
Penyebab Product Defect
Product Defect dapat disebabkan oleh beberapa hal, seperti.
Quality Assurance Matrix
Metode Quality Assurance Matrix (QAM) adalah sebuah alat kualitas yang didasarkan pada prinsip bahwa segala kegagalan terhadap proses manufaktur yang mempengaruhi pelanggan (yang mungkin merupakan proses produksi selanjutnya atau pelanggan akhir) harus dihilangkan. Metode ini akan membentuk suatu peringkat, untuk cacat potensial yang ada dan batas keandalan sistem kontrol dalam proses produksi sehingga memungkinkan untuk memberikan langkah-langkah perbaikan yang diperlukan dan mencapai dengan tujuan kualitas.
Tidak ada standar yang mengatur format QAM, dan setiap perusahaan atau organisasi menetapkan QAM sendiri secara berbeda-beda, tetapi pada dasarnya biasanya sama. Contoh berikut digunakan dalam industri otomotif:
QAM terdiri dari bagian utama berikut:
- Line Data : mencakup stasiun manufaktur dan langkah-langkah proses (termasuk pengujian).
- Information of failure / claim: berisi semua informasi utama tentang kegagalan eksternal/internal.
- Number of occurrences (before measures): berisi data statistik tentang terjadinya kegagalan (klaim dari pelanggan akhir, pemberitahuan internal oleh staf, dll.) sebelum penerapan tindakan baru.
- Stations with failure detection: berisi daftar stasiun manufaktur, termasuk stasiun pengujian dalam urutan aliran proses.
- Counter-measures: mendaftar semua tindakan, dengan data implementasi, verifikasi keefektifan, dan apakah informasi tersebut telah dialihkan ke lini/departemen/tanaman lain dalam kerangka Pelajaran yang Dipetik.
- Number of occurrences (after measures): berisi data statistik tentang terjadinya kegagalan (klaim dari pelanggan akhir, pemberitahuan internal oleh staf, dll.) setelah penerapan tindakan baru.
- Updated documents: berisi informasi apakah ada dokumen terkait yang diperbarui, seperti laporan FMEA, CP, 8D.
Tabel berikut membantu mengkategorikan efisiensi tindakan dan risiko terkait.
Built In Quality adalah membangun Kualitas Produk dari dalam proses-nya itu sendiri, atau dengan kata lain BIQ adalah konsep mencegah terjadinya cacat produk yang dilakukan oleh Operator langsung didalam dan disaat proses. Di dalam konsep ini, Operator bertindak pula sebagai Inspektor Kualitas dalam satu rangkaian proses produksi. Quality Assurance adalah serangkaian proses sistematis untuk menentukan apakah suatu produk atau jasa memenuhi syarat yang ditentukan. Matriks QA adalah tabel yang menggambarkan bagaimana cacat dibangun ke dalam produk dalam kondisi saat ini, dalam proses di mana seseorang ingin memastikan kualitas. Matriks ini memungkinkan manajer untuk melihat sekilas proses mana yang menghasilkan cacat, peralatan dan metode proses mana yang rusak, dan bagaimana keduanya terkait. Quality Engineering adalah disiplin ilmu teknik yang berkaitan dengan prinsip-prinsip dan praktik jaminan dan pengendalian kualitas produk dan layanan. Dalam pengembangan perangkat lunak, ini adalah manajemen, pengembangan, operasi, dan pemeliharaan sistem TI dan arsitektur perusahaan dengan standar kualitas tinggi.
Berikut merupakan rancangan QAM (Quality Assurance Matrix) pada BDI Injection yang dinilai pada 2 aspek quality assurance yaitu Prevention dan Detection:
Prevention BDI Factory
Penilaian Detection BDI Factory
Detection rate adalah rasio defect yang ditemukan saat proses QA dengan total keseluruhan defect yang ditemukan baik pada proses QC atau oleh customer.
Contoh: Misalnya, 90 cacat ditemukan selama QA/tahap pengujian dan 20 cacat ditemukan oleh pelanggan setelah rilis. DDP akan dihitung sebagai 90 dibagi (90+20) = 81,8%
Langkah-langkah yang dilakukan untuk perbaikan:
a. Penerapan QAM untuk BDI Injection
b. Implementasi 5S
c. Standarisasi Kerja
d. Pengurangan Kegiatan proses Quality Control yang Berulang
Berikut merupakan identifikasi kesulitan serta dampak positif dari setiap alternatif solusi yang dianalisis sesuai dengan kebutuhan perusahaan:
Proses Desain Operasional Quality Assurance (QA)
Berdasarkan gambar diatas dapat dilihat bahwa dengan penerapan Quality Assurance (QA) pada proses produksi dapat memperpendek alur proses produksi yang dapat diproyeksikan memperpendek waktu siklus (Cycle Time) yang semula sebesar 43 menit 40 detik menjadi lebih kecil yaitu sebesar 27 menit. Selain itu juga akan didapatkan pengurangan waktu tunggu (Lead Time) yang semula sebesar 1 menit 15 detik menjadi 45 detik untuk setiap produksi satu kanban produk.
Tingginya cost of quality diakibatkan oleh pola pikir bahwa quality menjadi tanggung jawab bagian dari quality control. Membangun kualitas pada proses merupakan langkah yang efektif dan lebih murah dibandingkan dengan melakukan inspeksi dan repair setelah produk dibuat. Pola pikir membangun kualitas pada sumbernya merupakan penerapan dari “Build In Quality” dengan cara melakukan hal yang benar sejak awal “making the product right from the first time” sebagai prinsip utamanya.
Kebutuhan perbaikan sistem Built In Quality perusahaan dapat kita peroleh dari hasil studi lapangan (Genba, Genbutsu, Genjitsu, Genri, dan Gensuko) yaitu terkait kebutuhan penerapan Quality Assurance (QA) pada operator produksi. Penerapan Quality Assurance (QA) pada operator ini akan mengurangi waktu total pada proses produksi sehingga pekerjaan di stasiun kerja lebih optimal serta peningkatan kemampuan operator untuk mencegah dan mendeteksi kecacatan produk sedini mungkin yang pada akhirnya akan mengurangi potensi pemborosan (waste) pada tahap berikutnya.
Berdasarkan uraian permasalahan yang telah dijelaskan diatas diperlukan penerapan Quality Assurance pada proses produksi di BDI Factory. Melihat kondisi saat ini yang pada proses pengendalian kualitas dilakukan sebanyak 2 kali pada QC Line dan QC Final. dapat dieliminasi menjadi hanya 1 kali pengecekan kualitas karena operator telah menjaga kualitas produk sedari awal, yaitu Sistem konsep Quality Assurance. Berikut ini adalah efisiensi yang akan didapatkan oleh BDI Factory dari penerapan Quality Assurance pada proses produksinya.