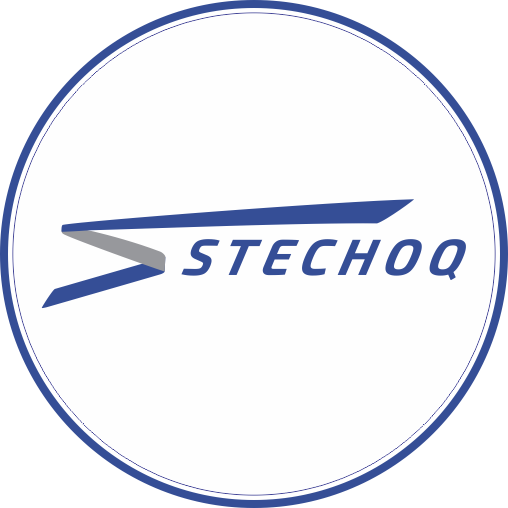
Built in Quality
Built In Quality adalah membangun Kualitas Produk dari dalam proses-nya itu sendiri, atau dengan kata lain BIQ adalah konsep mencegah terjadinya cacat produk yang dilakukan oleh Operator langsung didalam dan disaat proses. Di Dalam konsep ini, Operator bertindak pula sebagai Inspektor Kualitas dalam satu rangkaian proses produksi. Mungkin ini bisa dikategorikan sebagai Smart Sistem, dimana operator yang mengeksekusi pekerjaannya mengerti dan paham akan kualitas output yang mereka hasilkan. Sistem ini bukan tanpa kelemahan karena dalam Sistem BIQ operator dituntut untuk memiliki kemampuan sebagai pembuat (penginput) sekaligus inspektor, dengan demikian jika operatornya kurang mampu bertindak sebagai eksekutor dan inspektor ya sistem ini gak akan bisa jalan. Disamping itu juga diperlukan kejujuran dan disiplin yang tinggi, karena tidak ada manusia yang sempurna. Jadi jika operator melakukan kesalahan dengan meloloskan produk defect ke proses berikutnya yang kemudian tidak terdeteksi lalu berlanjut sampai final proses, seharusnya ya si operator yang melakukan kesalahan mau mengakui kesalahannya karena bagaimanapun juga dalam sistem BIQ ini biasanya dijalankan juga metode mampu telusur. Metode mampu telusur adalah metode yang bisa melakukan penelusuran balik kapan dan siapa yang mestinya bertanggung jawab membuat dan meloloskan defect hingga produk akhirnya Not Good. Ada beberapa Rule atau Control Point yang harus diperhatikan agar Sistem ini bisa berjalan dengan semestinya.
Built in Quality, kualitas pembuatan / proses pembuatan, yang
bukan melalui proses repair / perbaikan di proses selanjutnya.
Konsep, proses kerja yang benar, akan
menghasilkan produk yang sesuai dengan kualitas yang diharapkan.
a. Built in Quality (Kualitas dijaga atau dibuat di masing-masing proses)
Pencegahan defect / cacat input dan output dilakukan oleh Inspeksi, sedangkan didalam proses produksi dilakukan oleh operator sendiri. Quality dibuat di dalam proses , Operator bukan hanya mengerjakan , tetapi juga berfungsi sebagai Inspektur
Control Point : melakukan cara kerja dan proses kerja yang benar, meningkatkan kemampuan Operator, Mengembangkan metode Poka Yoke
Kelemahan : Tidak bisa dilakukan operator yang kurang mampu, diperlukan kejujuran dan disiplin yang tinggi
b. Total Quality (Seluruh Inspeksi dikerjakan oleh Operator)
Seluruh inspeksi ditiadakan
Operator dilatih untuk dapat menjadi Inspektur untuk dirinya sendiri dan proses sebelumnya Inspektur.
Control Point : Membudayakan Build in Quality diseluruh proses, baik proses produksi , maupun non produksi.
Kelemahan : Sangat tergantung dengan budaya organisasi, kemampuan operator menjadi sangat dominan, perlu perencanaan yang baik sebelum diimplementasikan, serta review tertarur baik hasil maupun proses.
c. Quality Control (Kualitas dikendalikan oleh bagian quality control)
Pencegahan defect/cacat/produk out dari proses penerimaan material sampai penyerahan ke konsumen, dilakukan secara berlapis (Quality Control) yang bertanggung jawab kepada pimpinan
Kelemahan : Banyak tenaga yang digunakan (cost up), Operator kurang peduli terhadap hasil kerjanya, dan kualitas produk yang diterima konsumen sepenuhnya tergantung kemampuan inspektur untuk mendeteksi
d. Quality By Inspection (Kualitas dipastikan melalui inspeksi)
Pencegahan defect/cacat/produk out dilakukan di penerimaan dan di output produk oleh bagian diluar produksi (quality assurance) QA bertanggung jawab dengan pimpinan organisasi
Kelemahan : Kesalahan baru diketahui pada akhir proses, bila terjadi produk tidak sesuai, akan melibatkan jumlah produk serta kerugian yang banyak, operator kurang peduli terhadap hasil pekerjaannya, kualitas produk yang diterima konsumen sepenuhnya tergantung kemampuan inspektur untuk mendeteksi.
Sebelum mengidentifikasi jenis cacat perlu diketahui terlebih dahulu perbedaan setiap kecacatan. Jenis cacat dan reject pada hasil produk injeksi plastik disajikan dalam Tabel 5.1 Jenis Cacat dan Reject Hasil Produksi. Berikut merupakan perbedaan setiap cacat:
Detection rate adalah rasio defect yang ditemukan saat proses QA dengan total keseluruhan defect yang ditemukan baik pada proses QC atau oleh customer.
Contoh: Misalnya, 90 cacat ditemukan selama QA/tahap pengujian dan 20 cacat ditemukan oleh pelanggan setelah rilis. DDP akan dihitung sebagai 90 dibagi (90+20) = 81,8%. Selanjutnya berikut ini adalah tabel penilaian risiko prevention.
Langkah-langkah yang dapat dilakukan untuk perbaikan adalah sebagai berikut:
Faktor-faktor yang mempengaruhi pelaksanaan sistem built in quality:
a. Mesin
Mesin memiliki pengaruh dalam pelaksanaan sistem built in quality. Pengaturan mesin yang dilakukan sangat berpengaruh terhadap produk yang dihasilkan, apabila suhu yang diatur terlalu panas maka akan menghasilkan produk yang cacat. Maka dari itu diperlukan standar pengaturan yang tertulis dan harus diterapkan dalam proses produksi injeksi plastik.
b. Metode Produksi
Metode produksi memiliki pengaruh dalam pelaksanaan sistem built in quality. Sistem produksi manual secara cenderung akan menghalangi proses built in quality karena sistem yang manual berarti melakukan segala proses dengan manual. Resiko human error sangat mungkin terjadi. Sumber Daya Manusia (SDM) atau tenaga kerja merupakan salah satu faktor produksi yang vital dalam proses produksi. Ketersediaan SDM yang baik akan sangat mempengaruhi kualitas produk atau jasa yang dihasilkan. Namun seberapapun baiknya kualitas SDM yang dimiliki perusahaan, tidak dapat menghilangkan human error yang memang sudah melekat dalam diri setiap manusia Hollnagel (1998). Berbeda dengan sistem otomatis dengan sistem produksi otomatis proses built in quality akan lebih mudah terlaksana dan terkontrol. Sebagai contoh saat suatu perusahaan melakukan proses QC, pada sistem manual QC akan dilakukan oleh operator atau manusia dimana kemungkinan human error dapat terjadi. Belum lagi persepsi manusia yang berbeda-beda sangat memugkinkan perbedaan. Pada sistem produksi otomatis proses QC dapat dilakukan menggunakan bantuan robot melalui sistem otomasi seperti penggunaan sensor. Hal ini memungkinan tidak ada persepsi yang berbeda antar mesin QC sehingga proses built in quality lebih terjaga.
c. Material
Material memiliki pengaruh yang cukup vital pada proses produksi, material sangat berpengaruh pada produk output pada proses produksi yang berjalan. Maka dari itu diperlukan standar pengaturan yang tertulis dan harus diterapkan dalam pemilihan bahan material yang akan digunakan pada proses produksi.
d. Sumber daya Manusia
Sumberdaya memiliki pengaruh dalam pelaksanaan sistem built in quality. karena manusia berperan vital pada proses produksi, mulai dari memilih bahan material, menjalankan mesin hingga melakukan pengecekan pada setiap lini produksinya. maka dari itu perlu adanya sumber daya manusia yang berkualitas pada proses produksi.
Terdapat beberapa teknik pengumpulan data dalam menyelesaikan persoalan built in quality, yaitu Genchi Genbutsu. Genchi (Go and See) adalah fakta atau kejadian yang sebenarnya terjadi, dan gembutsu adalah produk yang menjadi objek permasalahan. Pengambilan data dilakukan dengan cara melihat aktual di lapangan dan didasarkan pada acuan KPI yang ada. Konsep Genba Genchi Genbutsu (melihat secara langsung data dan fakta aktual di lapangan) selalu diutamakan dalam proses pemecahan masalah (Pratomo, 2017).
Selain metode diatas, terdapat metode lain yang dapat digunakan, yang diantaranya adalah Genri, Gensoku, Genba, Genbutsu, Genjitsu. Genri (Theory) dapat diartikan penyelesaian masalah dengan mengikuti atau berdasarkan pada prinsip teori umum dan pendekatan ilmiah, atau melakukan perbaikan proses secara terus menerus. Gensoku (Rules) memiliki pengertian untuk mematuhi Pedoman atau Prosedur dalam berpikir kritis dan perbaikan proses. Genba (Real Place) ialah sebuah kata yang berasal dari bahasa Jepang yang berarti ‘tempat sesungguhnya’ atau dalam bahasa Inggris sering disebut ‘actual place’. Secara istilah gemba adalah tempat dimana value ditingkatkan atau tempat dimana pekerjaan diselesaikan. Genbutsu (Actual Things) adalah hal atau kondisi yang sebenarnya. Di sini Manajemen diharapkan untuk melihat suatu peristiwa atau artikel dengan mata kepala sendiri atau merasakannya sendiri dan menyentuhnya dengan tangan mereka sendiri. Sedangkan Genjitsu (Reality) merupakan suatu kenyataan yang harus dirasakan, seperti gejala (symptoms) masalah dan pengaruhnya terhadap proses penciptaan dan proses kerja dalam suatu industri.
Dengan menerapkan prinsip 5 Gen ini, manajemen produksi diharapkan tidak hanya mengambil suatu keputusan melalui informasi atau laporan dari bawahannya, tetapi harus melihat dan merasakan setiap permasalahan secara langsung. Dengan begitu setiap keputusan yang diambil menjadi lebih akurat, efektif, dan efisien.
Pengumpulan data dilakukan mengikuti prinsip teori umum dan pendekatan ilmiah, kemudian memecahkan masalah serta melakukan peningkatan proses, kemudian meninjau secara langsung dimana suatu permasalahan terjadi, melihat suatu kejadian atau benda dengan matanya sendiri, serta merasakan kenyataan seperti gejala-gejala adanya permasalahan serta pengaruhnya terhadap proses produksi maupun proses kerja di dalam suatu industri. Pengumpulan data ini bertujuan untuk mengetahui apakah ada cacat produk, dengan adanya built in quality dapat mencegah terjadinya cacat produksi yang dilakukan oleh operator secara langsung di dalam dan saat proses produksi.